Back injection molding of polymer films with capillary filled sub-micron silver wires
semanticscholar(2019)
摘要
Monolithic integration of integrated circuits onto macroscopic polymer parts can be done by adding individual electronic elements after the polymer part has been molded or by adding a film with the entire circuit prepared in advance. In the first case, the patterning of non-flat surfaces requires a patterning method with tools that can follow the outline of a 3D topography, in the second case a flexible film that needs to be deformed. This approach has been used for thermoforming and is now also favored for printed electronics [1,2]. This way, fabrication methods for low-cost flexible electronics can be used to prepare the polymer films. We placed a 175 μm-thick polymeric film into the crowned mold of an injection-molding tool that constitutes a concave cylinder lens with a radius of 30 mm and a depth of 10 mm, with a convex cylinder at the opposite side. The film (PMMA: Evonik Plexiglas film 99524, Tg 113°C) was patterned by thermal nanoimprint (T-NIL) at 180°C and was pressed into this crowned surface by the viscous polymer (Evonik Plexiglas 7N, Tg 110°C) injected onto the backside of the film. The tool temperature (40°C) was low enough that the 260°C hot melt was cooled down to ~100°C when it reaches the film upon entering the mold cavity, thus it was able to deform the thermoplastic film without erasing its topography. The resulting back-injected cylinder-like element consists of the film that is covering the top of a 3 mm thick convex polymer body. Two cases were implemented: When the film is patterned towards the mold surface, the resulting cylinder has a surface topography constituted by the film. When it is patterned towards the injecting polymer, the surface structures are embedded. The latter is an interesting alternative if not only surface structures are used, but films that are already processed, e.g., covered with electrodes. We used both cases for the fabrication of components covered with a metal wire array (Fig. 1). Our process has, in comparison to inkjet printing used for printed electronics, resolutions down to sub-μm and relies on nanoparticle self-confinement in V-grooves [3]. Similarly, films with open microchannels were back-injection molded (Fig. 2). The shape of the 3.1 μm wide Vgrooves is slightly flattened by the process, thus enabling capillary filling in an open microfluidic approach [4]. In both cases, the wires are electrically conducting. Combining nanoimprint lithography and additive patterning techniques may be a viable strategy to create low-cost devices on large areas or even free-form components. Such strategies can be applied to various designs of electrical circuits that enable to build complex devices as planned within the SFA project FOXIP [5]. Applications would be LEDs and sensors embedded in polymer components.
更多查看译文
AI 理解论文
溯源树
样例
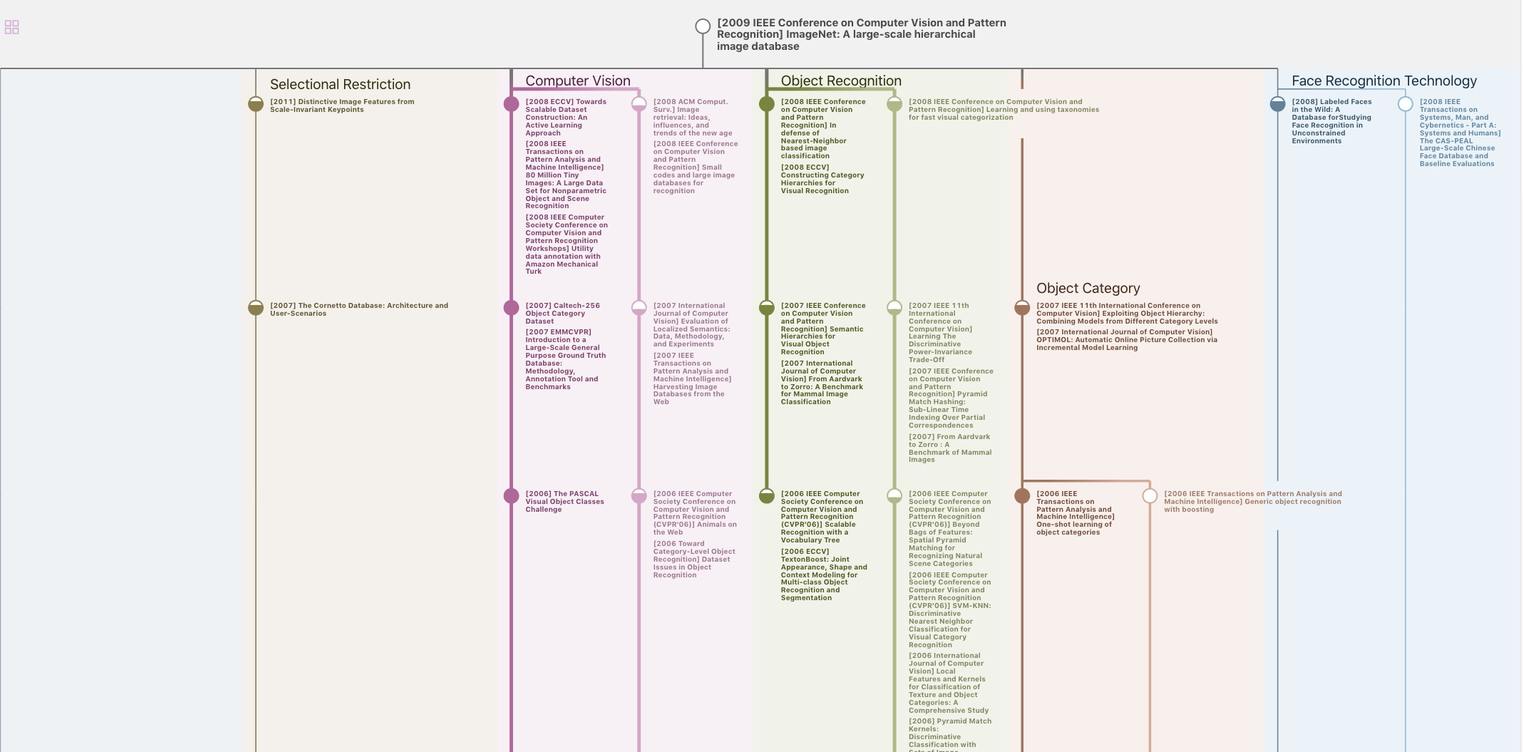
生成溯源树,研究论文发展脉络
Chat Paper
正在生成论文摘要