Effects of flow structure on heat transfer of squealer tip in a turbine rotor blade
International Communications in Heat and Mass Transfer(2020)
Abstract
Consideration heat transfer while organizing the flow structure in the turbine blade tip region is important to improve the turbine aerodynamic performance and turbine blade reliability. Numerical methods were conducted to investigate the flow physics and the heat transfer characteristic in high pressure turbine squealer tip. The impacts of some geometric parameters and aerodynamic conditions on heat load distribution were also discussed. Based on the above results, a heat transfer model for squealer tip was developed. The results show that the high heat transfer occurred in certain tip region is mainly caused by the leakage jet impingement on these surfaces. The velocity direction and magnitude of the leakage are determined by the characteristic of flow structures, especially the scraping vortex in the cavity. Different squealer height, relative casing velocity and blade loading can change the heat load distribution of tip region by varying the characteristic of the scraping vortex. Through simplifying the process of the leakage jet flowing into the cavity as a backward step flow, a heat transfer model is established which provides a useful tool to predict heat load distribution of the squealer tip.
MoreTranslated text
Key words
Squealer tip,Tip leakage flow,Heat transfer model
AI Read Science
Must-Reading Tree
Example
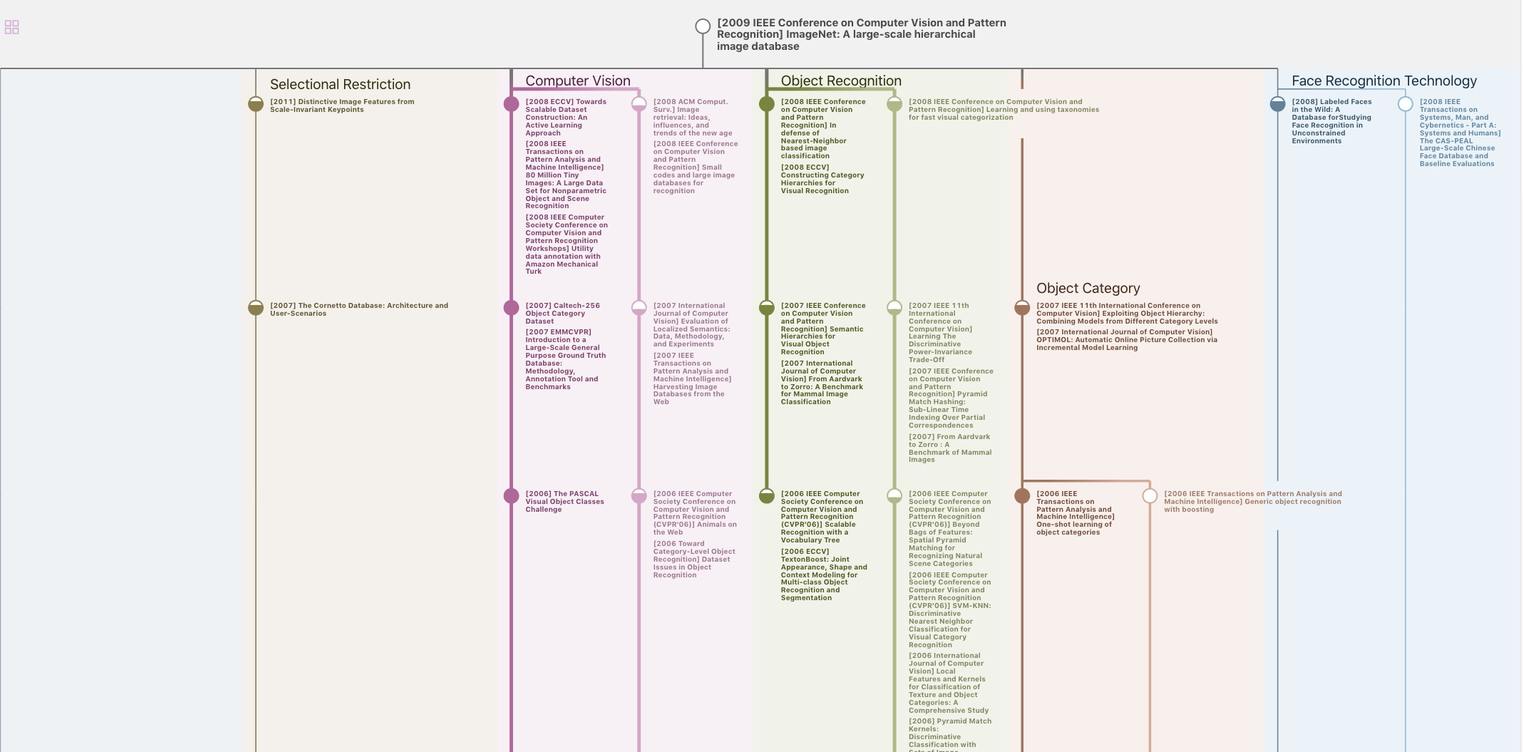
Generate MRT to find the research sequence of this paper
Chat Paper
Summary is being generated by the instructions you defined