FE Simulation for stress distribution and surface deformation in Ti-6Al-4 V induced by interaction of multi scale laser shock peening parameters
Optik(2020)
摘要
The article investigates the residual stress distribution and surface deformation induced with Laser Shock Peening (LSP) using Finite Element Method (FEM) model.LSP surface treatment is complex phenomenon with huge number of parameters interaction in nanosecond span of time to induce deep residual stress. ABAQUS Explicit Dynamic FEM is used with Johnson-Cook material model for analysing non linear constitutive behaviour of Ti6Al4V and compared with published experimental results. A fine correlation is observed for simulated model and literature results at particular peening condition. A Design of Experiment based simulation of LSP is performed to analyse the effect of Laser spot diameter, laser spot overlapping rate, Laser power density, Number of laser shots and laser pulse time on residual stress distribution and surface deformation. Fractional factorial design is adopted for designing the experiments with five factors having three levels each. Equal in levels of laser spot overlap, laser power density and number of shots will gradually increase in residual stress induced and huge surface deformation with respect to laser pulse duration. Random interactions of these parameter levels have two different type of results; deep compressive stress with minimum deformation and reversal of compressive to tensile stress with huge deformation on surface followed by deep compressive stress.
更多查看译文
关键词
Multi scale laser parameter,FEM modeling,Residual stress,Surface deformation,Design of experiments (DoE)
AI 理解论文
溯源树
样例
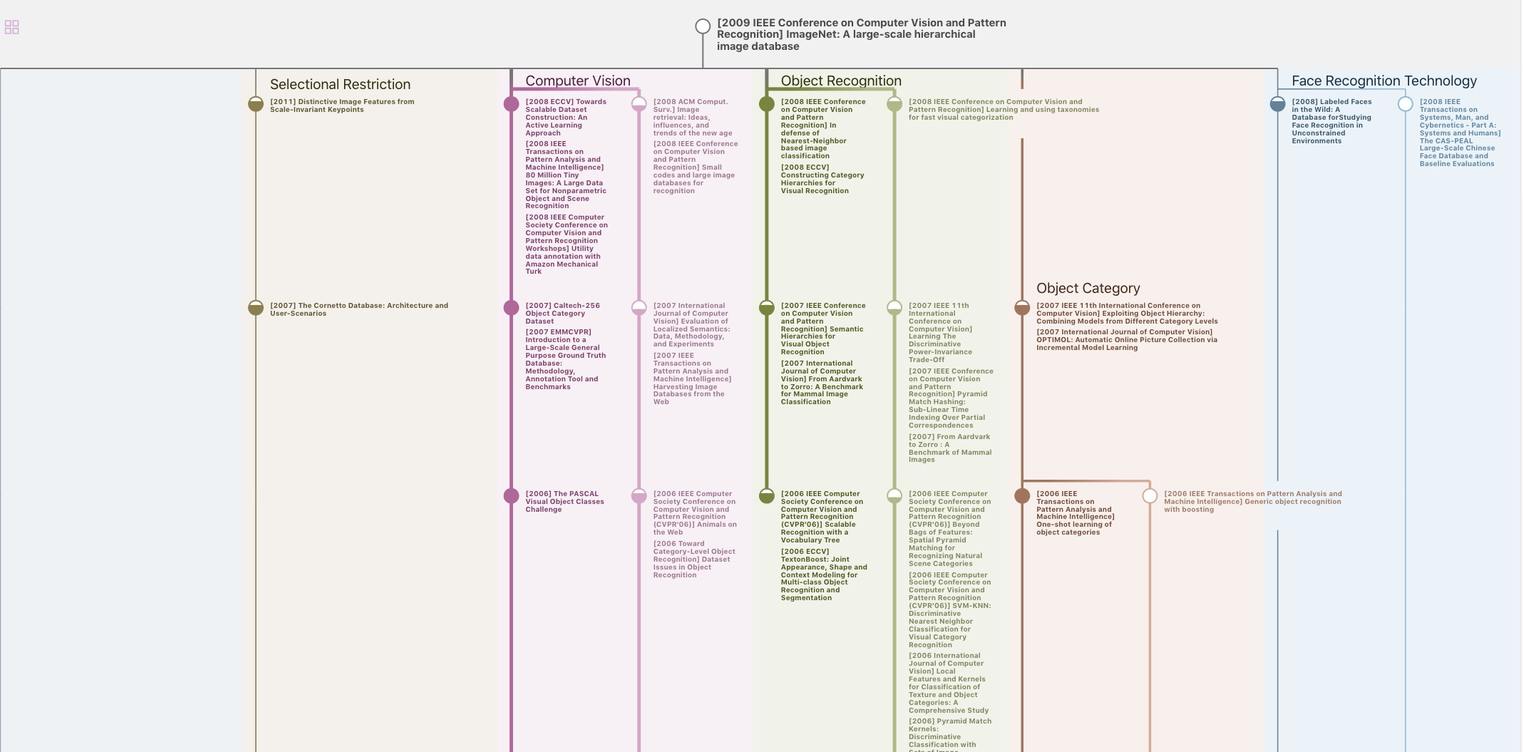
生成溯源树,研究论文发展脉络
Chat Paper
正在生成论文摘要