Identification of process-induced residual stresses in 3D woven carbon/epoxy composites by combination of FEA and blind hole drilling
Composites Part A: Applied Science and Manufacturing(2020)
摘要
Process-induced residual stresses in 3D woven carbon-epoxy composites are studied by blind hole drilling experiments interpreted with finite element (FE) modeling. It is assumed that residual stresses are primarily caused by the difference in thermal expansion coefficients of the constituents which are modelled as temperature-dependent linear elastic solids. The impact of residual stresses is quantified by drilling blind holes in the composite panels and mapping the resulting in-plane surface displacements by electronic speckle pattern interferometry. Mesoscale finite element models are used to correlate these surface displacements with the volumetric distribution of the residual stresses in the composite. This is done by determining the effective temperature drop ΔTeff that results in the same predictions for the surface displacements as experimentally measured. The effective temperature drop approach allows to use linear elastic models while approximately accounting for various nonlinear effects occurring in the material during processing. The models are also used to establish the sensitivity of the predicted results to the exact location of a hole and its depth.
更多查看译文
关键词
A. Fabrics/textiles,A. 3-Dimensional reinforcement,B. Residual/internal stress,C. Finite element analysis (FEA)
AI 理解论文
溯源树
样例
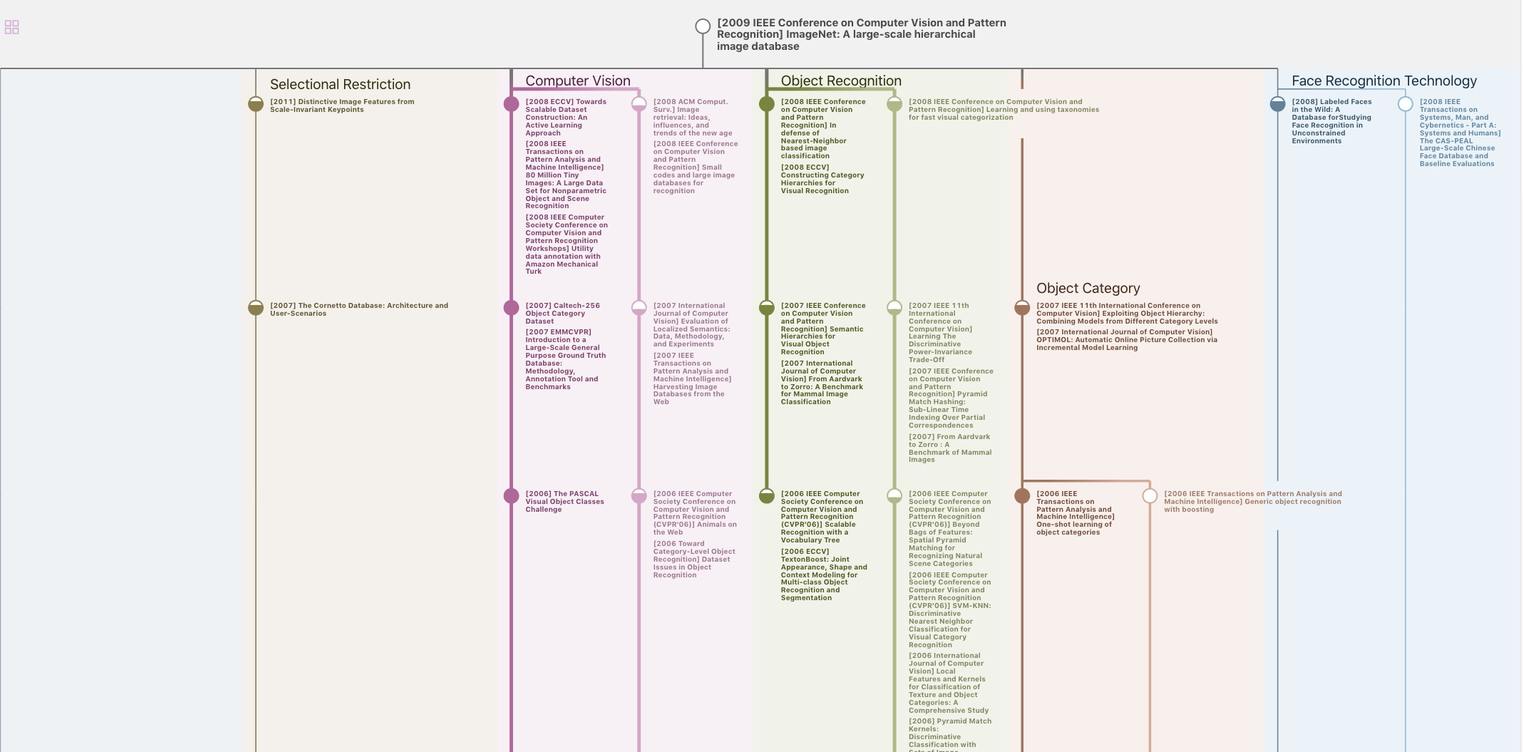
生成溯源树,研究论文发展脉络
Chat Paper
正在生成论文摘要