Inverse Design Strategies for 3D Surfaces Formed by Mechanically Guided Assembly.
Advanced materials (Deerfield Beach, Fla.)(2020)
摘要
Deterministic transformations of 2D patterns of materials into well-controlled 3D mesostructures serve as the basis for manufacturing methods that can bypass limitations of conventional 3D micro/nanofabrication. Here, guided mechanical buckling processes provide access to a rich range of complex 3D mesostructures in high-performance materials, from inorganic and organic semiconductors, metals and dielectrics, to ceramics and even 2D materials (e.g., graphene, MoS ). Previous studies demonstrate that iterative computational procedures can define design parameters for certain targeted 3D configurations, but without the ability to address complex shapes. A technical need is in efficient, generalized inverse design algorithms that directly yield sets of optimized parameters. Here, such schemes are introduced, where the distributions of thicknesses across arrays of separated or interconnected ribbons provide scalable routes to 3D surfaces with a broad range of targeted shapes. Specifically, discretizing desired shapes into 2D ribbon components allows for analytic solutions to the inverse design of centrally symmetric and even general surfaces, in an approximate manner. Combined theoretical, numerical, and experimental studies of ≈20 different 3D structures with characteristic sizes (e.g., ribbon width) ranging from ≈200 µm to ≈2 cm and with geometries that resemble hemispheres, fire balloons, flowers, concave lenses, saddle surfaces, waterdrops, and rodents, illustrate the essential ideas.
更多查看译文
关键词
3D assembly,3D mesostructures,analytic modeling,inverse design
AI 理解论文
溯源树
样例
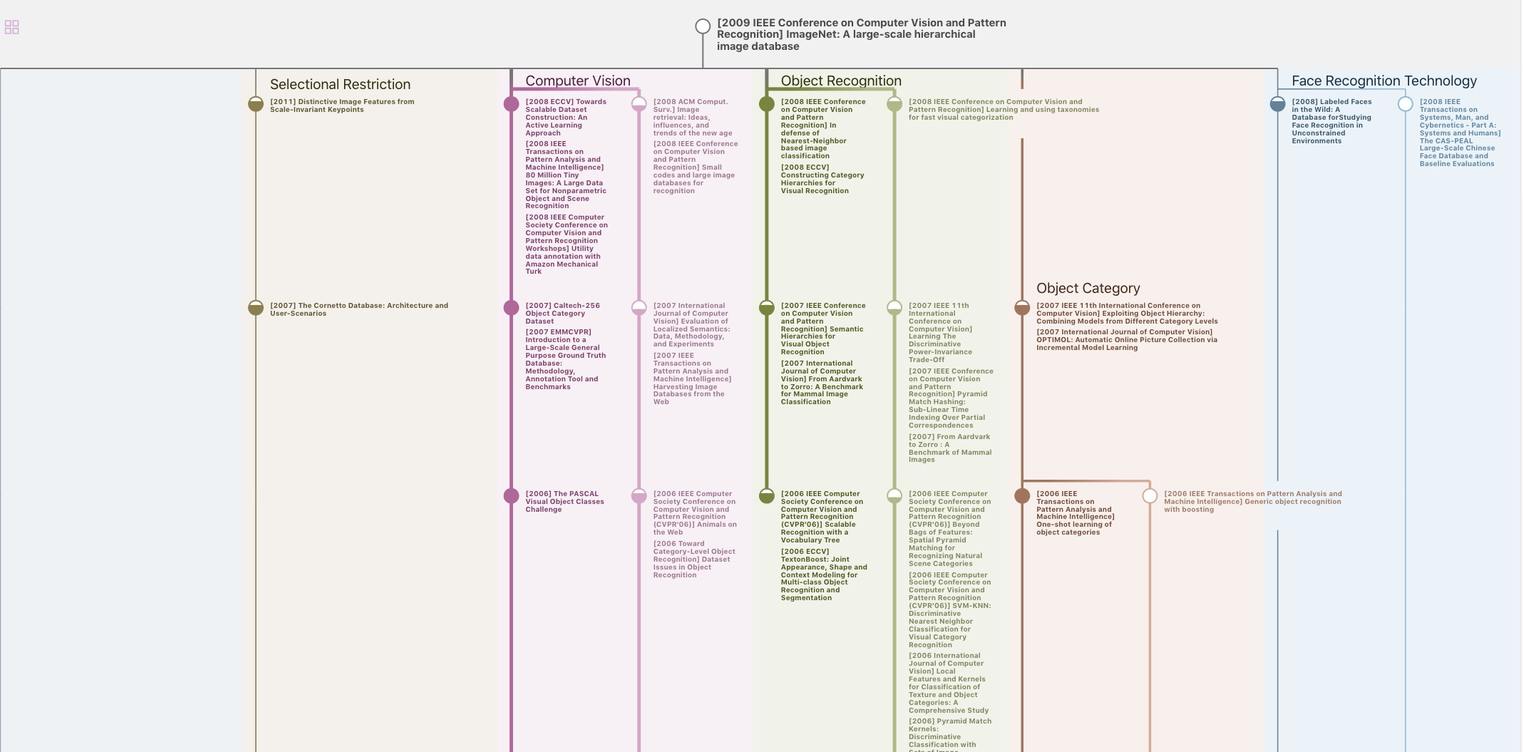
生成溯源树,研究论文发展脉络
Chat Paper
正在生成论文摘要