Robot-Based Machining Of Unmodeled Objects Via Feature Detection In Dense Point Clouds
2019 IEEE/RSJ INTERNATIONAL CONFERENCE ON INTELLIGENT ROBOTS AND SYSTEMS (IROS)(2019)
摘要
Machining applications using robots are still not common in industrial settings. Reasons are the unintuitive programming concepts which typically require expert knowledge and the inflexibility regarding small alterations of the workpieces. We present a prototypical solution for an intuitive and flexible robotic machining concept for unmodeled work pieces. For this we use a high resolution laser scanner to record very dense point clouds. Algorithms to detect linear edges with obtuse angled corners, linear edges with acute angled corners, linear inner edges and circular edges were developed, demonstrated and validated. To accurately execute generated trajectories in practice, an algorithm to directly calibrate the transformation between the sensor and the milling tool was developed. For the algorithms and the calibration process a repeatability tolerance of 0.2 mm is achieved.
更多查看译文
关键词
industrial settings,expert knowledge,high resolution laser scanner,dense point clouds,obtuse angled corners,acute angled corners,linear inner edges,circular edges,robot-based machining,unmodeled objects,feature detection,unintuitive programming,milling tool,calibration process,sensor,size 0.2 mm
AI 理解论文
溯源树
样例
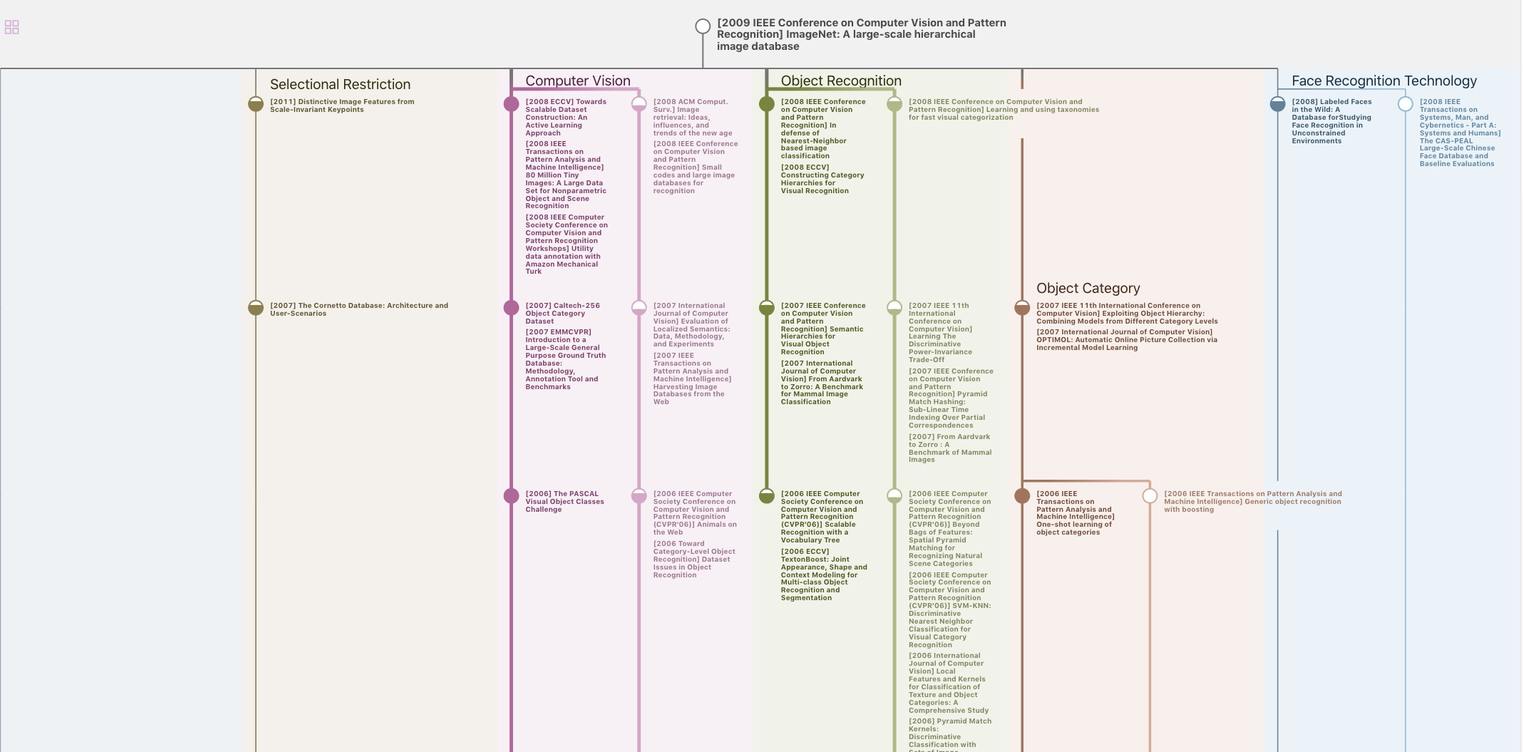
生成溯源树,研究论文发展脉络
Chat Paper
正在生成论文摘要