Numerical simulation and experimental research on the comprehensive performance of the shell side of the spiral wound heat exchanger
Applied Thermal Engineering(2019)
摘要
In this paper, the spiral wound heat exchanger (SWHE) partial geometric models with different tube diameters (6 mm < d0 < 14 mm), tube pitches(2 mm < Z < 14 mm) and spacing bar thickness (2 mm < S2 < 4.5 mm), were established. Numerical simulation and performance comparison were carried out using water as the heat transfer fluid. The numerical results showed that the heat transfer performance of the shell side was optimized when the tube diameter, the tube pitch, and the spacing bar thickness was 6, 14, and 3.5 mm, respectively. Moreover, the experimental research on the heat transfer of Y-type and K-type SWHEs was conducted on the water vapor at a constant volume flow rate in the tube side and the liquid water at volume flow rates in the range of 1.5–7 m3/h in the shell side.. The experimental data showed that the heat transfer coefficient of Y-type SWHE was 3.4–17.9% higher than K-type SWHE under the same condition. The pressure drop of Y-type SWHE is 9.8–61% lower than K-type SWHE. The ratio of performance evaluation factors (PEC) of the Y-type to K-type SWHE is was greater than 1, so the heat transfer performance of Y-type was better than K-type SWHE. Additionally, the comparisons between experimental data and the numerical results show that the relative errors are in the acceptable range. Therefore, the numerical results are correct and trustable.
更多查看译文
关键词
SWHE,Heat transfer characteristic,Inlet and outlet structure,Numerical simulation,Experimental research
AI 理解论文
溯源树
样例
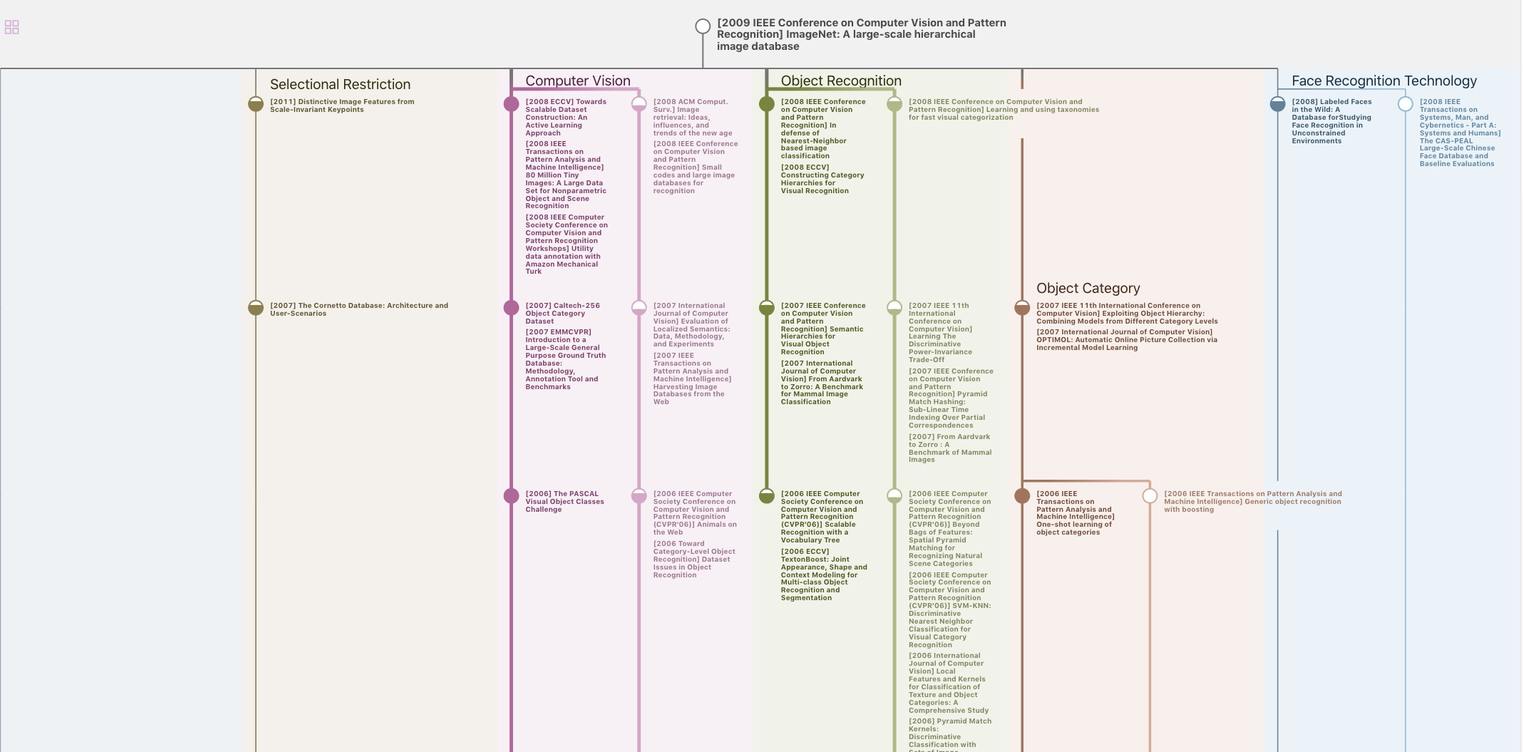
生成溯源树,研究论文发展脉络
Chat Paper
正在生成论文摘要