Kinematics for a six-axis EDM machine by screw theory and its application in feedrate planning in EDM for shrouded blisks
The International Journal of Advanced Manufacturing Technology(2019)
Abstract
In multi-axis electrical discharging machining (EDM), to maintain a stable discharging gap, a gap width controller regulates the feedrate of a tool electrode with respect to a workpiece. However, in the existing EDM machine, feedrates in G-codes are computed with an extended linear displacement which takes 1 ∘ as 1 mm and does not take the diameters of rotational axes into account. To adjust feedrates with actual distances between an electrode and a workpiece, kinematics from the tool frame to the workpiece frame is needed. In this paper, screw theory is utilized to derive the kinematics of a six-axis EDM machine consisting of three translational axes and three rotational axes. With the rigid transformation of each axis described by an exponential of a twist, the overall kinematics is obtained as a product of exponentials of twists. With the forward kinematics, the feedrate post-processing algorithm (FPPA) is used to plan feedrates in G-code blocks. Experimental results showed that the feedrate planning according to the forward kinematics can reduce the machining time by 23.5% in the EDM for a shrouded blisk. Discharge gap statistics showed that the use of the FPPA algorithm increases the normal discharge ratio.
MoreTranslated text
Key words
Kinematics,Multi-axis electrical discharging machining (EDM),Feedrate planning
AI Read Science
Must-Reading Tree
Example
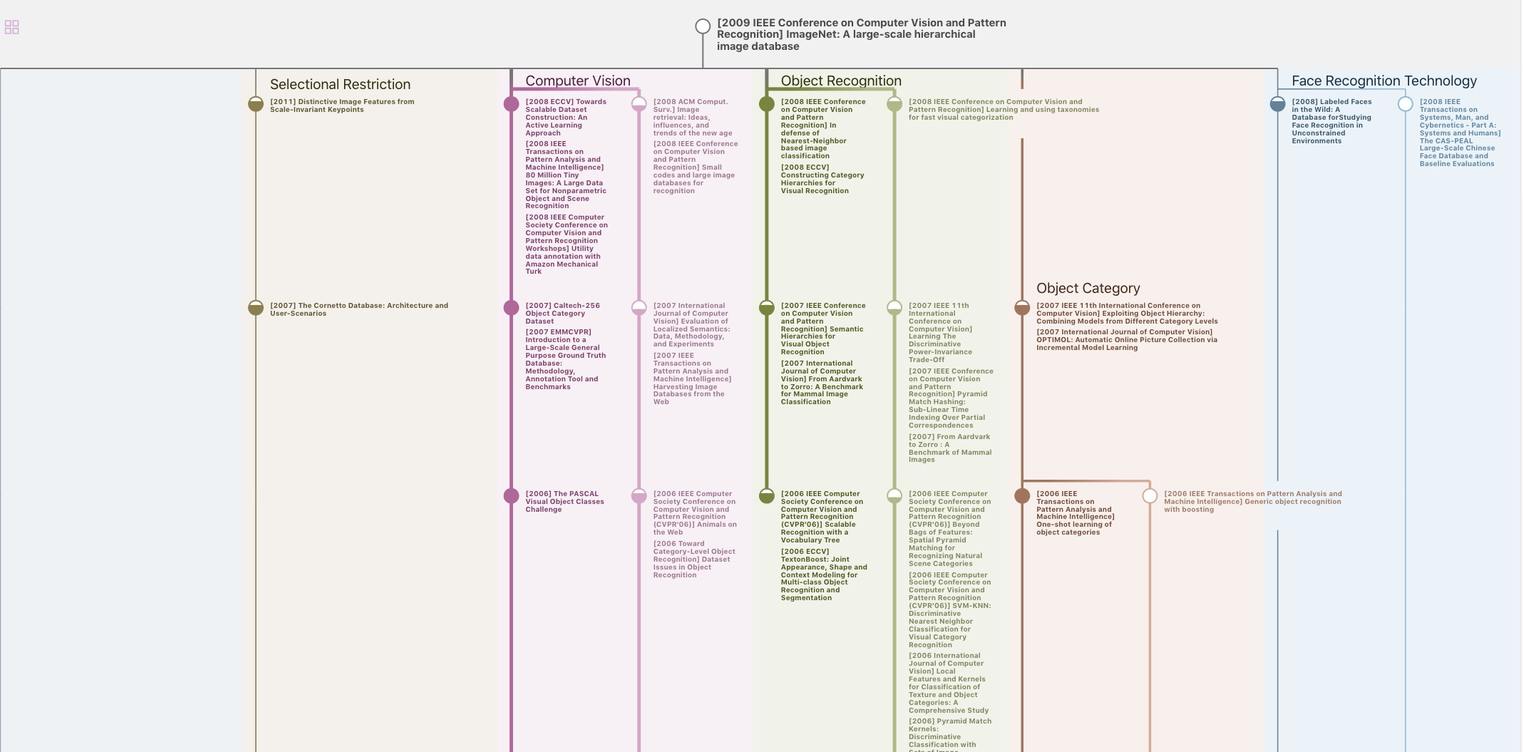
Generate MRT to find the research sequence of this paper
Chat Paper
Summary is being generated by the instructions you defined