Simulation of residual stress using thermomechanical analysis on wire EDM cut surface
Materials Today: Proceedings(2019)
摘要
Wire EDM is widely used for machining precision components. In WEDM process, the heat of plasma spark generated between the cathode and anode is responsible for the melting of work piece material in controlled shape through series of coordinated spark in “ON” and “OFF” cycle. The part of material which melted forms cater and some melted material gets redeposited on the work piece before completely ejecting out in cooling cycle due to sudden cooling by surrounding fluid. The heat affected zone (HAZ) also contains this redeposited molten metal and forms a recast layer with complex surface texture. The recast layer exhibits residual stress at surface like other cutting process. Residual stresses limit the service life of component since it initiates cracks and which may propagate to the base metal under favorable condition. This limits performance of the engineering components. This is important to predict such stresses. In this study the FE method has been applied to simulate residual stresses generated the during WEDM cutting on the HAZ of P91 steel. The FE simulation consists of a thermal analysis, revealing the temperature profile of the machined surface during the WEDM process followed by a sequentially-coupled structural analysis, giving residual stress pattern. In FEM analysis user defined subroutine is added to simulate the volumetric strain change due to phase transformation with temperature. Metallurgical phase changes were accommodated in the form of thermal expansion in the FEM analysis. This paper also describes the size of craters and heat affected zone. Residual stresses obtained from the analysis are shown in the form of stress contours as a function of distance from the cutting edge. Trends of behavior of residual stresses shows good prediction with experimental data obtained from XRD.
更多查看译文
关键词
WEDM: Wire electro discharge machining,XRD: X-ray diffraction,SSPT: Solid state phase transformation,HAZ: Heat affected zone,Lower critical temperature Ac1,Ac3 Upper critical temperature,Dilatometry
AI 理解论文
溯源树
样例
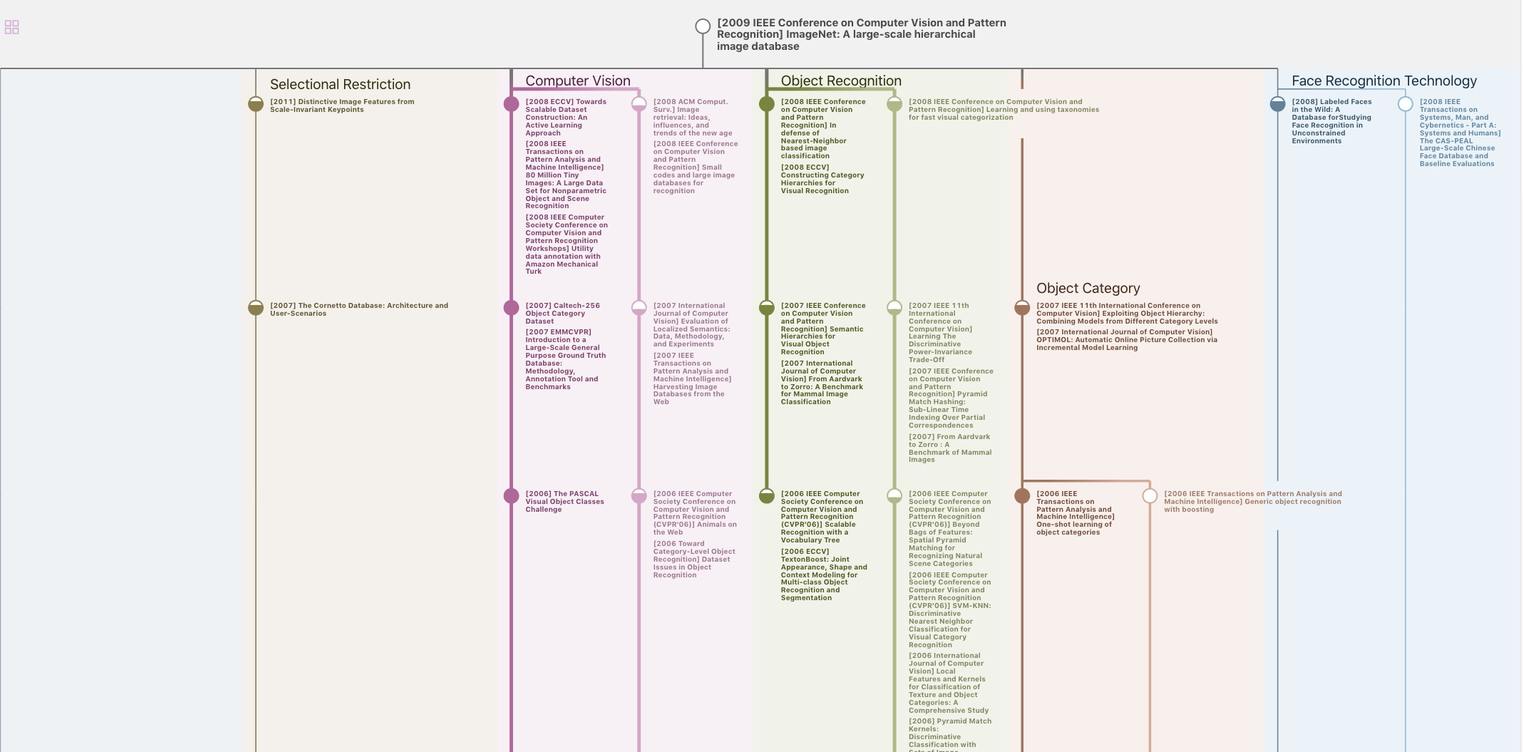
生成溯源树,研究论文发展脉络
Chat Paper
正在生成论文摘要