CFD-simulation-based optimization of superheater for steam production from waste heat of SRF combustor
ENERGY SOURCES PART A-RECOVERY UTILIZATION AND ENVIRONMENTAL EFFECTS(2019)
摘要
A superheater uses waste heat from a combustor or an incinerator to produce superheated steam through heat exchange between saturated steam and exhaust (flue) gas. Superheaters predominantly use thin tube-type pipes, which makes it difficult to experimentally determine internal phenomena such as the flow, pressure distribution, and temperature distribution. Computational fluid dynamics (CFD) has recently been used to successfully analyze superheaters. In this study, steam at 180 degrees C and 3.4 bars was converted via a cylindrical superheater into superheated steam above 700 degrees C and 3bars using exhaust gas at 900 degrees C from a solid refuse fuel combustor. The superheated steam was then supplied to a high-temperature solid oxide electrolyte cell to increase the hydrogen production efficiency of water electrolysis. CFD analyses were also conducted using a commercial Fluent simulator to study the effects of the furnace size, superheater size, inlet and outlet diameters, and steam generation amount on the exit temperature. The CFD simulation results were determined to be valid by a pilot experimental apparatus, which showed that the error rate between the experimental measurements and the simulation results was less than 2%. For the same volume, the superheater with the largest surface area (0.4-m diameter and 1-m length) produced the highest exit temperature. For steam inlet and outlet diameters of 8 mm, the highest exit temperature was 652 degrees C. By reducing the flow rate to 70 kg/h, steam at over 700 degrees C and 3 bars could be obtained under these optimal conditions.
更多查看译文
关键词
Computational fluid dynamics (CFD),superheater,heat exchange,high-temperature steam,radiation,exit temperature
AI 理解论文
溯源树
样例
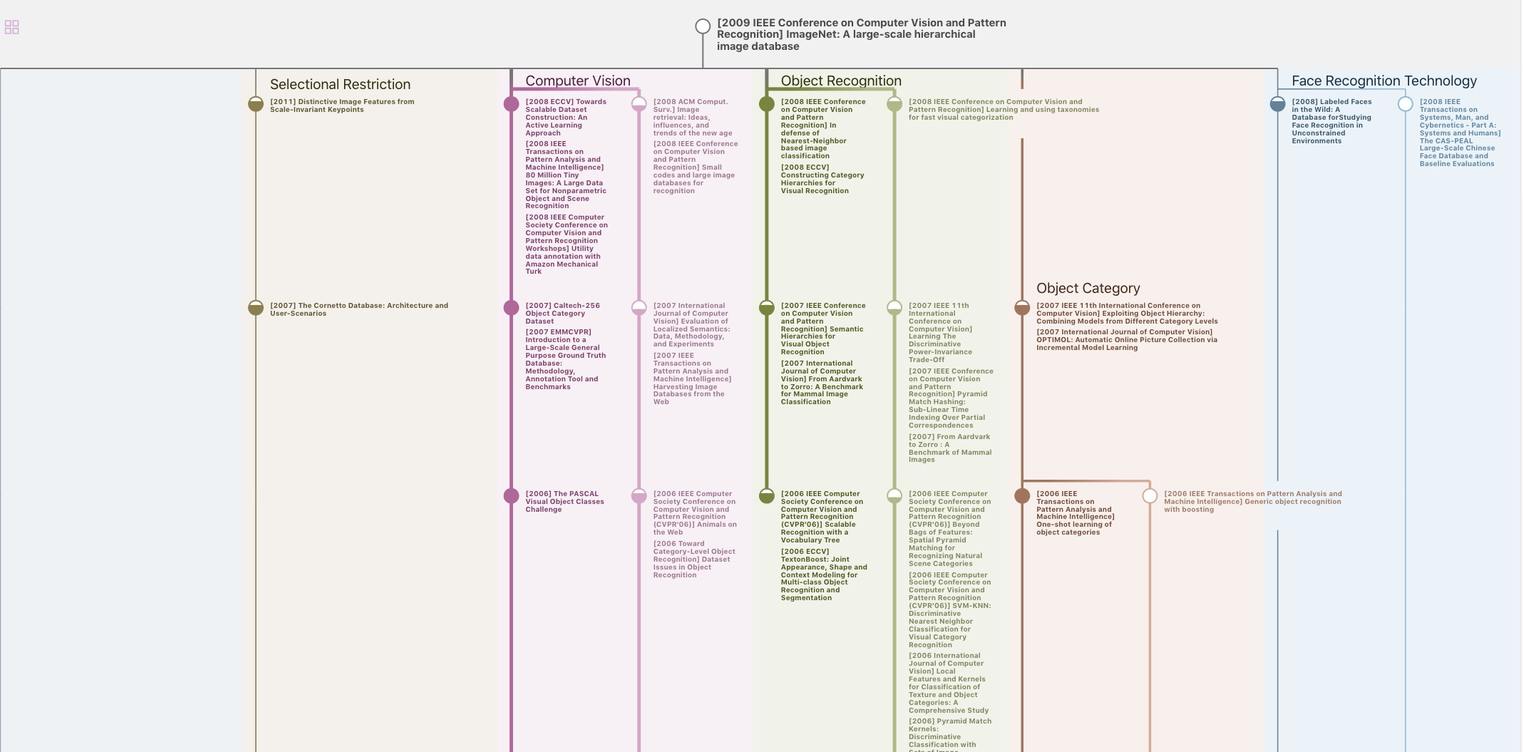
生成溯源树,研究论文发展脉络
Chat Paper
正在生成论文摘要