A Cyber-Physical System For Smart Fixture Monitoring Via Clamping Simulation
INTERNATIONAL JOURNAL OF SIMULATION MODELLING(2019)
Abstract
This paper presents a cyber-physical fixturing system (CPFS) that provides a new way for smart fixture monitoring in milling processes through cloud based simulation and optimization applications. The purpose of the CPFS is to improve the fixture-workpiece stability and thus to prevent deformations of the machined thin-wall workpiece by controlling the simulated clamping and reaction forces at locators. An equilibrium analysis is employed to model and simulate the behaviour of the fixture-workpiece system with respect to the actual cutting tool position. The simulation is incorporated with an optimization routine to minimize the clamping and locating forces. The smart fixture condition monitoring system is developed by connecting the machine tool to the simulation resources in the fixturing platform which performs instant fixture condition monitoring based on signal processing, cutting force signal feature extraction, fixture layout simulations, clamping forces optimization, simulation of clamping/locating forces and process corrective control actions. A prismatic workpiece with slot milling operation is considered to validate the proposed CPFS system.
MoreTranslated text
Key words
End Milling, Fixture Condition, Smart Monitoring, On-Line Simulation, Optimization, Clamping/Locating Forces
AI Read Science
Must-Reading Tree
Example
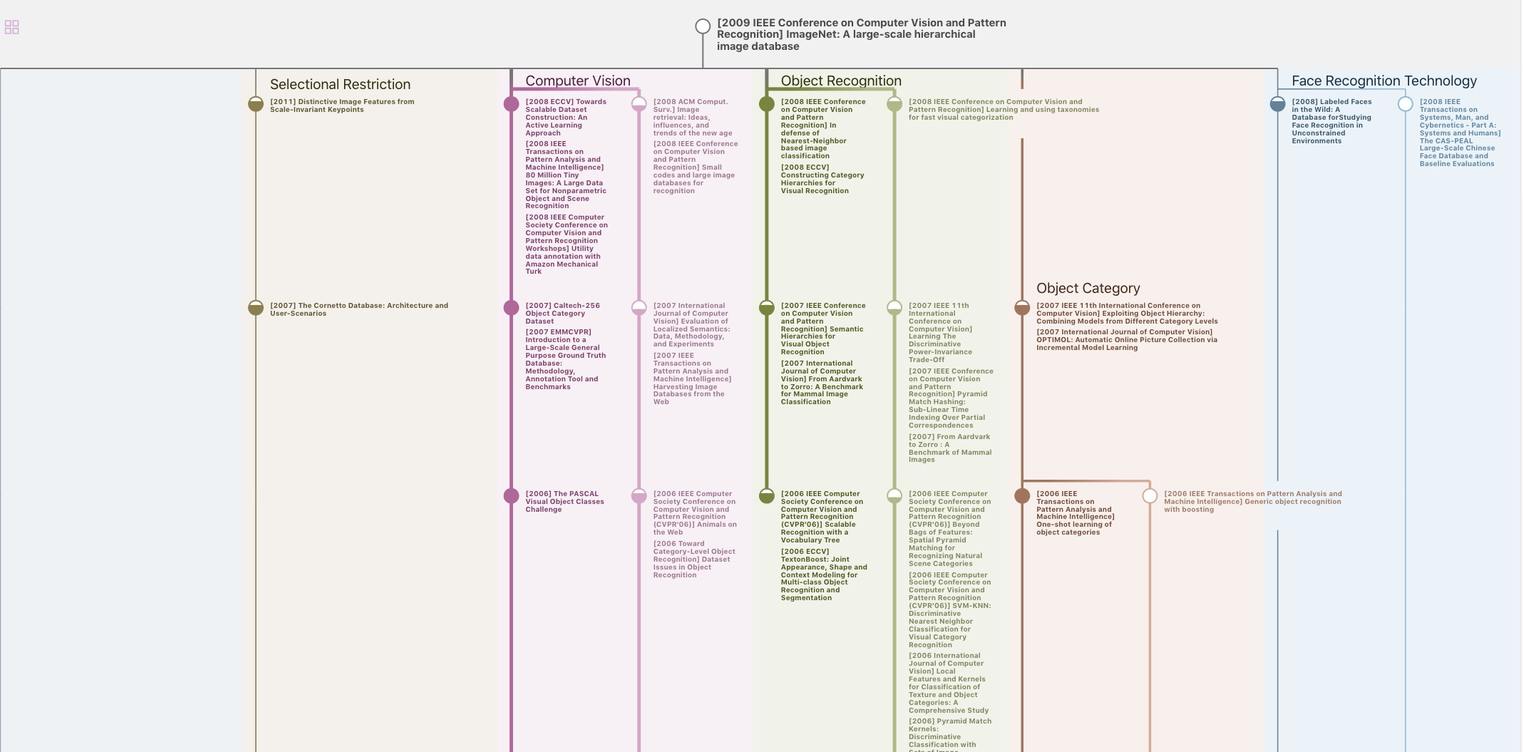
Generate MRT to find the research sequence of this paper
Chat Paper
Summary is being generated by the instructions you defined