Finite element simulation of the micromachining of nanosized-silicon-carbide-particle reinforced composite materials based on the cohesive zone model
Nanotechnology and Precision Engineering(2018)
摘要
A finite element method based on the cohesive zone model was used to study the micromachining process of nanosized silicon-carbide-particle (SiCp) reinforced aluminum matrix composites. As a hierarchical multiscale simulation method, the parameters for the cohesive zone model were obtained from the stress-displacement curves of the molecular dynamics simulation. The model considers the random properties of the silicon-carbide-particle distribution and the interface of bonding between the silicon carbide particles and the matrix. The machining mechanics was analyzed according to the chip morphology, stress distribution, cutting temperature, and cutting force. The simulation results revealed that the random distribution of nanosized SiCp causes non-uniform interaction between the tool and the reinforcement particles. This deformation mechanics leads to inhomogeneous stress distribution and irregular cutting force variation.
更多查看译文
关键词
Multiscale,Cohesive zone model,Nanosized silicon carbide particles,Composite materials,Micromachining
AI 理解论文
溯源树
样例
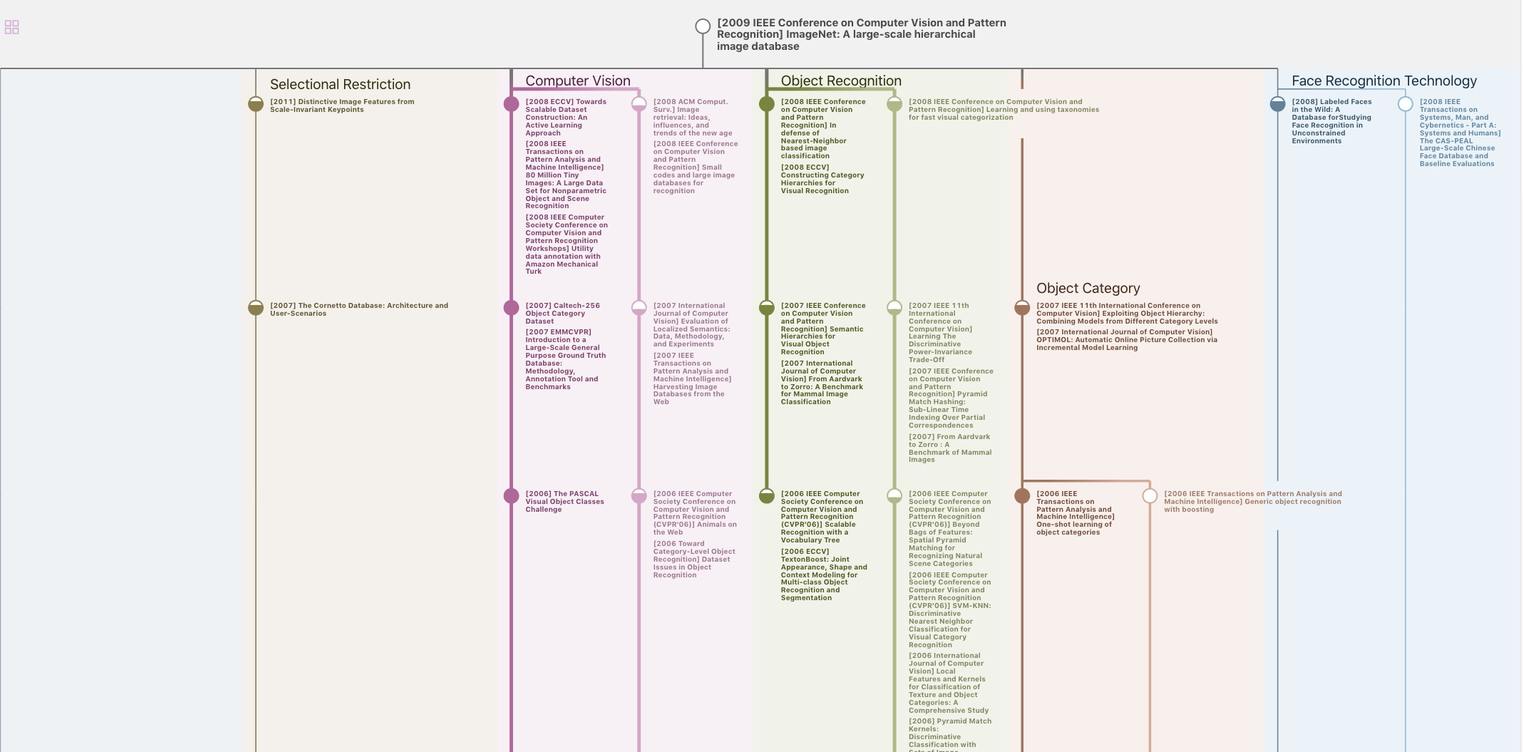
生成溯源树,研究论文发展脉络
Chat Paper
正在生成论文摘要