Design Of A Distributed Compliant Mechanism Using Spring-Lever Model And Topology Optimization For Piezoelectrically Actuated Flapping Wings
MECHANICS OF ADVANCED MATERIALS AND STRUCTURES(2021)
摘要
We present a distributed compliant mechanism, which acts like a transmission between a flapping wing of a micro air vehicle and a laminated piezoelectric actuator. The piezoelectric bimorph actuator is connected in cantilever configuration with the compliant mechanism at its free end. The mechanism takes translational deflection at its input from the piezoelectric actuator to provide angular deflection at its output, which causes flapping. We used spring-level model and topology optimization to obtain the design of the mechanism. The design of the mechanism has been finalized by analyzing the design considering beam model with geometric nonlinearity. The final mechanism is a planar structure of 1 mm thickness and 40 mm x24 mm in-plane footprint. The input stiffness of the compliant mechanism is 711 N/m and the output torsional stiffness is 0.014 Nm/rad. The compliant mechanism is tested with a piezoelectric bimorph actuator. The mechanism takes +/- 1 mm deflection with +/- 0.2 N block force at 30 Hz as an input and produces +/- 6 degrees flap angle at 30 Hz as an output. The first fundamental frequency of the mechanism is 391 Hz, which is almost 13 times greater than our assumed wing flapping frequency 30 Hz. The final mechanism is prototyped with a 3D printer using VeroWhitePlus RGD835 material and tested with a piezoelectric bimorph actuator using a bench-top experimental set-up.
更多查看译文
关键词
Mechanism, flapping, distributed compliant mechanism, topology optimization, spring-lever model, piezo-actuated flapping mechanism, flapping wing micro air vehicle
AI 理解论文
溯源树
样例
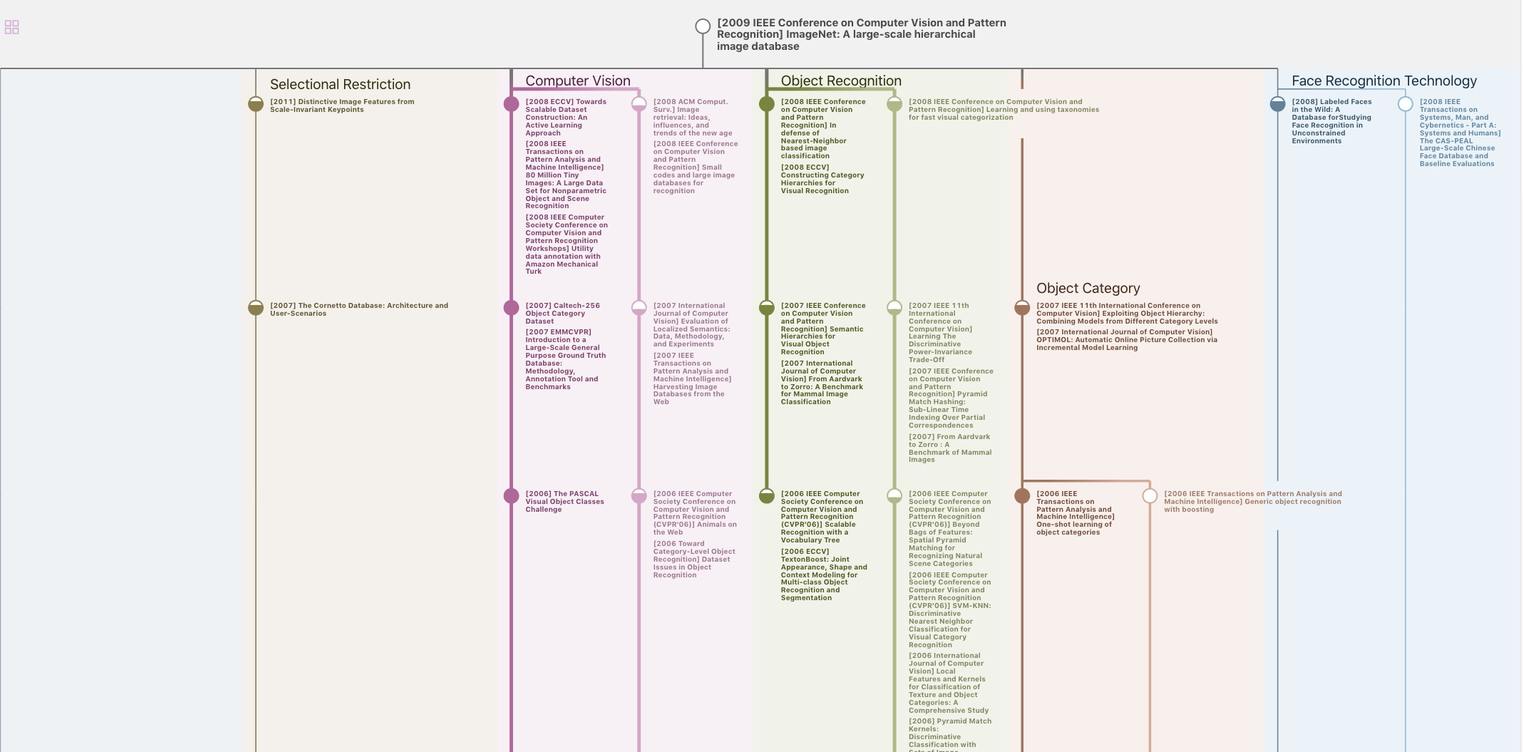
生成溯源树,研究论文发展脉络
Chat Paper
正在生成论文摘要