Ultra Precision Surface Finishing Processes
INTERNATIONAL JOURNAL OF AUTOMATION TECHNOLOGY(2019)
Abstract
Surfaces of different complex shapes are aspirated part of many scientific measuring devices, medical, astronomical, and other precision activity utilizations. Components at miniaturized level should meet required surface roughness for the intended applications. Surface finishing of freeform and miniaturized components are always difficult and need to look for a new way out. In this study, an attempt was made to improve surfaces roughness of selected, most frequently used, engineering materials using different innovative processes, which can be integrated with CNC machine centers. An advanced automated surface finishing tools such as ball burnishing embedded with load cell, vibration assisted polishing, and self-propelled abrasive multi-jet polishing tools are proposed. Ball burnishing is advantageous for pre-machining process of ball polishing. Using the polishing device embedded with load cell, the constant force polishing is achieved. To reduce the volumetric wear of a polishing ball, vibration assisted polishing device is also integrated. Moreover, self-propelled abrasive multi-jet polishing tool, which achieves 93.33% improvement of surface roughness for lapped optical glass of BK7 has been subjugated from Ra 0.300 mu m to 0.020 mu m. These tools can be miniaturized and applicable in small micro CNC machining centers.
MoreTranslated text
Key words
surface finishing, ball burnishing, ball polishing, vibration assisted polishing, abrasive multi-jet polishing
AI Read Science
Must-Reading Tree
Example
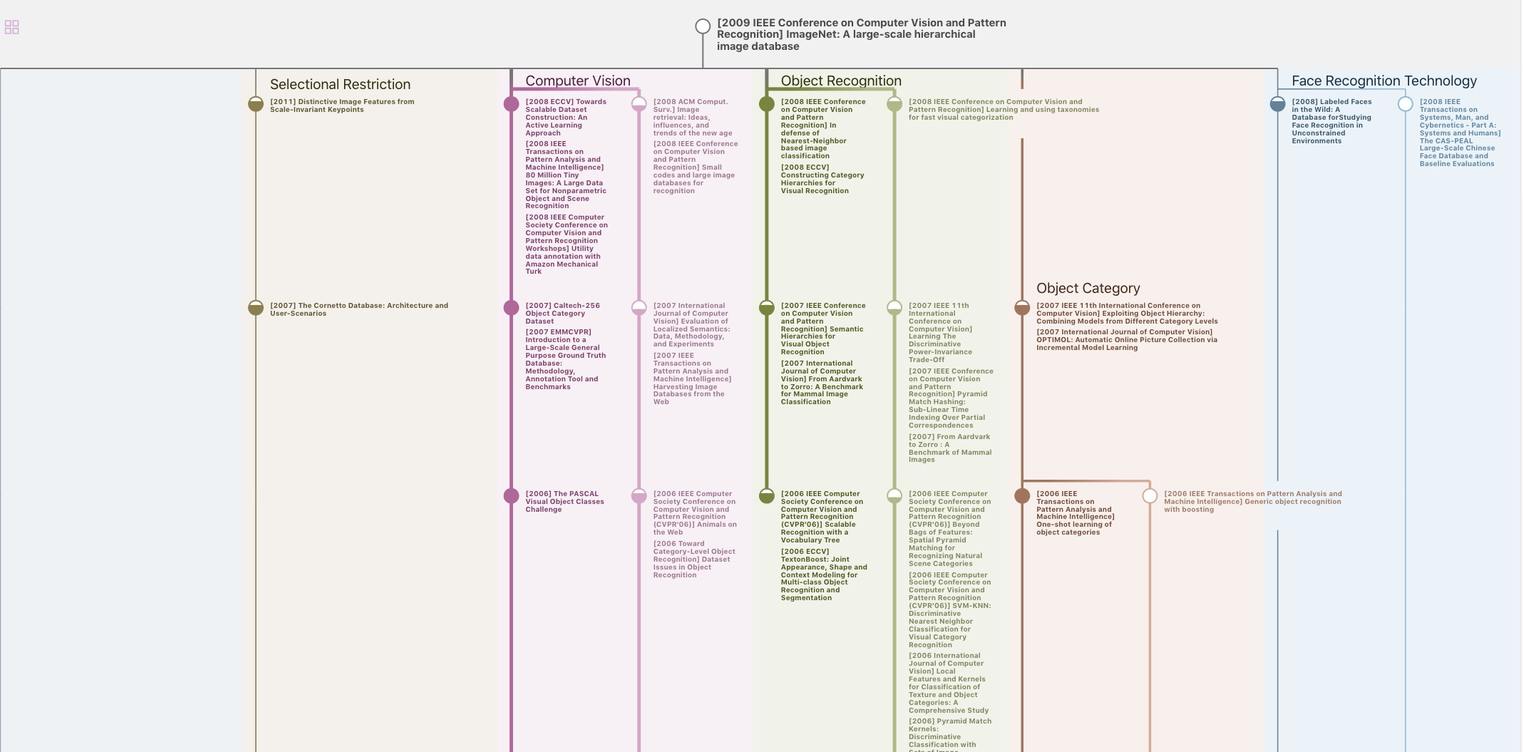
Generate MRT to find the research sequence of this paper
Chat Paper
Summary is being generated by the instructions you defined