Reduced-Order Analysis Of An Oil-Fuel Furnace Vibration And Comparison With The Finite Element Method
JOURNAL OF VIBRATION AND CONTROL(2019)
Abstract
Thermoacoustic oscillation occurs in modern industrial furnaces, gas turbines, and liquid rockets. However, the thermoacoustic prediction tools for furnaces vibration are less developed. This paper presents a one-dimensional (1D) linear acoustic approach to analyze the three-dimensional acoustic modes of a 660 MWe oil-fuel furnace. The interaction between the flame and acoustic field is described with the flame transfer function. The global time delay is evaluated through a Reynolds averaged simulation. The results of the 1D acoustic approach are compared with real furnace test data. The unstable modes are close to the natural modes of the furnace, and the 30 Hz in the longitudinal mode is the strongest vibration frequency. The effects of inlet length reduction and separation plate removal are also examined. When the separation plates are removed, the time lag of flame in response to inlet flow decreases from 52.5 milliseconds (ms) to 43.8 ms. The results of the 1D approach and finite element method (FEM) show a same safe operation window. The reduced-order procedure and FEM adopted in this study give us a solution to mitigate the vibration in the furnace.
MoreTranslated text
Key words
Vibration,thermoacoustic instability,industrial furnace,linear approach,finite element method
AI Read Science
Must-Reading Tree
Example
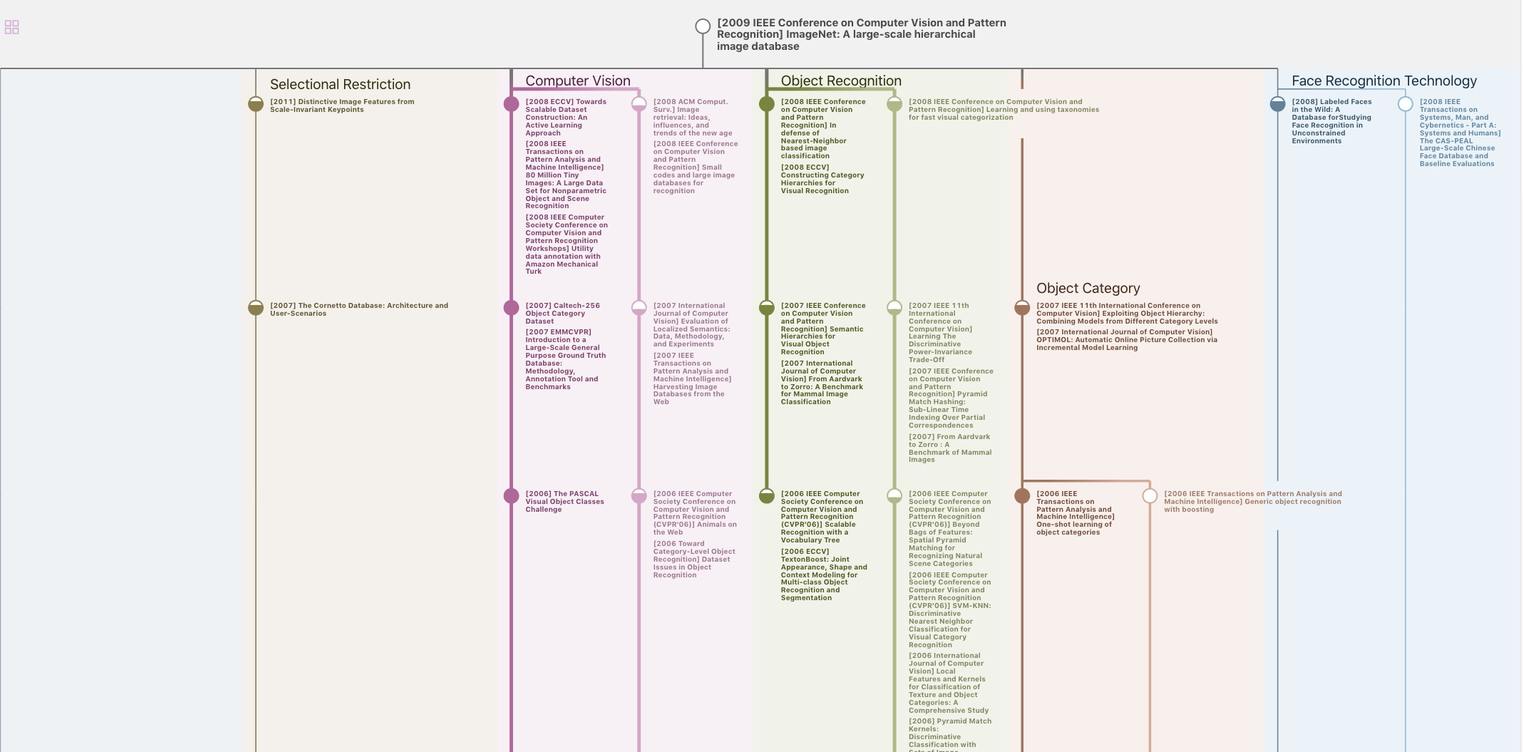
Generate MRT to find the research sequence of this paper
Chat Paper
Summary is being generated by the instructions you defined