Experimental validation of thermo-mechanical simulations of ITER diagnostic pressure gauges
Fusion Engineering and Design(2018)
摘要
Diagnostic Pressure Gauges (DPG) shall provide measurements of the neutral gas pressure in ITER in 4 lower ports, 4 divertor cassettes and 2 equatorial ports. The DPG is a hot cathode ionization gauge where the filament (hot cathode) is heated up by a high electric current in order to reach a temperature sufficient for emission of electrons. The DPG will operate in an environment with strong magnetic field (up to 8 T). Hence, under mentioned operational conditions the filament of the gauge will be under high thermal stress and the influence of j→×B→ forces. Finite element analyses (FEA) of the DPG sensor have been executed with the aim to determine the temperature distribution and to assess stress level and structural integrity of the filament and other gauge components. In cases where boundary conditions and material constants were not exactly defined, assumptions have been made accordingly. This, however, reduces the reliability of simulation results. In order to gain benchmarking data for validation of the performed simulations, experimental investigation of the filament temperature profile has been executed. Reliability tests are envisaged to investigate the operational margin of the gauge by identifying the minimum heating current required to produce sufficient emission current over a long period of time and the maximum current in a high magnetic field causing structural damage to the filament. Results of these tests allow measuring the accurateness of FEA, which delivers predictions of stability thresholds with respect to the heating current and magnetic field. Comparison of experimental data with results of FEA simulations are discussed in this paper.
更多查看译文
关键词
ITER,Plasma diagnostics,Pressure gauge,Tungsten filament,FEA,Testing
AI 理解论文
溯源树
样例
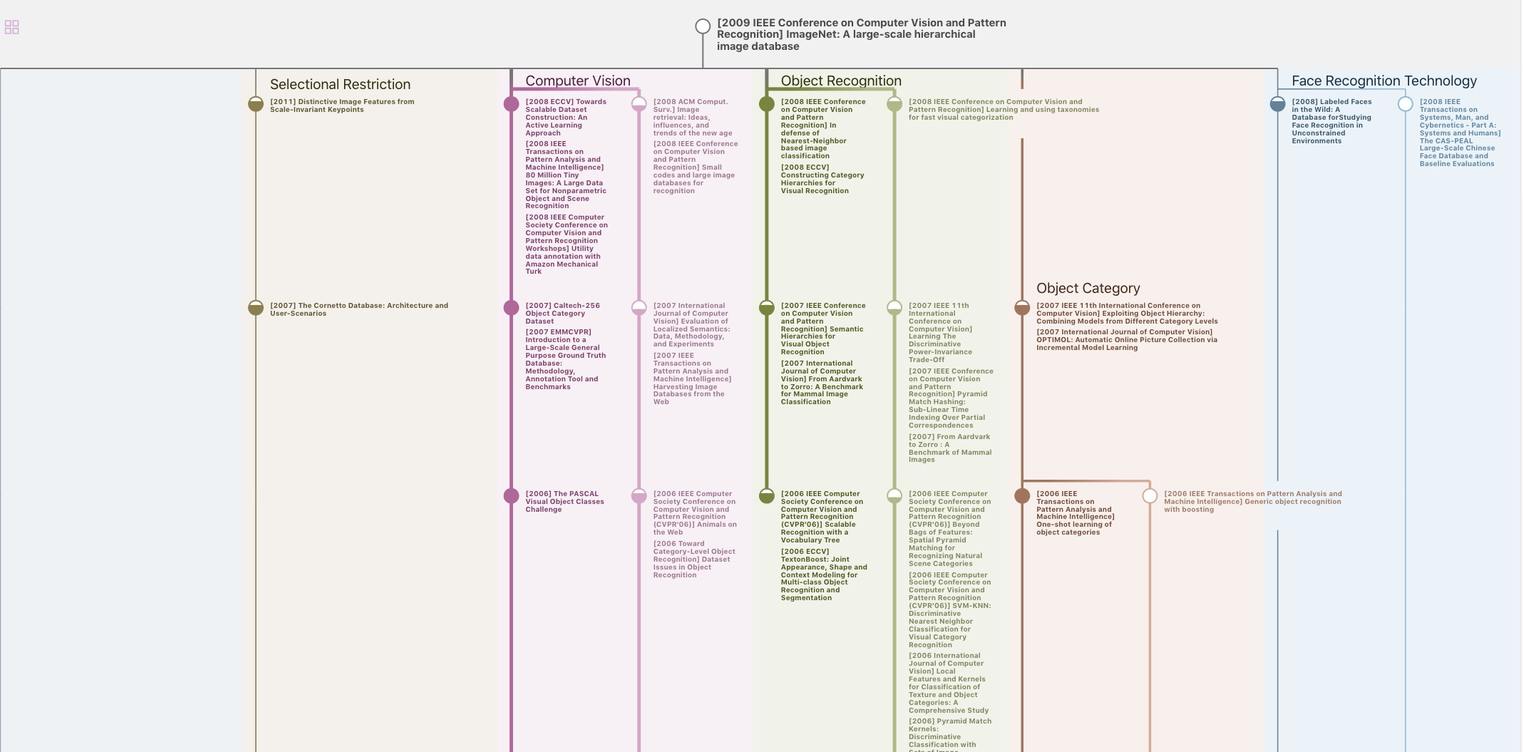
生成溯源树,研究论文发展脉络
Chat Paper
正在生成论文摘要