DESIGN OF FLEXIBLE IMPLANTS FOR PRESERVATION OF PHYSIOLOGICAL MOBILITY EXPLOITING ADDITIVE MANUFACTURING
Journal of Bone and Joint Surgery-british Volume(2017)
摘要
Due to tumours or bone fractures caused by high mechanical impact, the affected tissue has to be removed. Preserving the physiological mobility after the treatment could prevent stress shielding or overload of the surrounding muscles and ligaments. In case of a critical vertebral body defect, the body and its attached disks have to be removed. Thereafter the adjacent vertebral bodies are braced together resulting in limited physiological spine movability. A flexible implant adapted to and preserving the patient-specific physiological spine mobility would be a desirable solution. Since Ti6Al4V is a common material for medical implants as well as in AM, it is used in this scientific study. Using design methodology tools, a systematic generation of possible solutions is achieved. Furthermore, already existing solid state hinges made of plastics with AM are taken as archetype and their design is adapted to the metal laser powder bed fusion (L-PBF) process. Therefore, an initial geometry design, based on a solid state hinge demonstrator made by TNO was created with Inventor 2016. By abstracting the vertebrae body segment, two contact surfaces, two joints with rotational degree of freedom (DOF) and axial suspension as well as one solid connection could be identified. As a first implant design, the abstracted joints are replaced by the designed hinges. By the application of simulation software tools the flexion behaviour of the solid state hinge can be analysed. Initial results show that the simulation of the flexion behaviour corresponds with the AM specimen. The applied force necessary for bending the specimen depends on the thickness of the struts.
更多查看译文
AI 理解论文
溯源树
样例
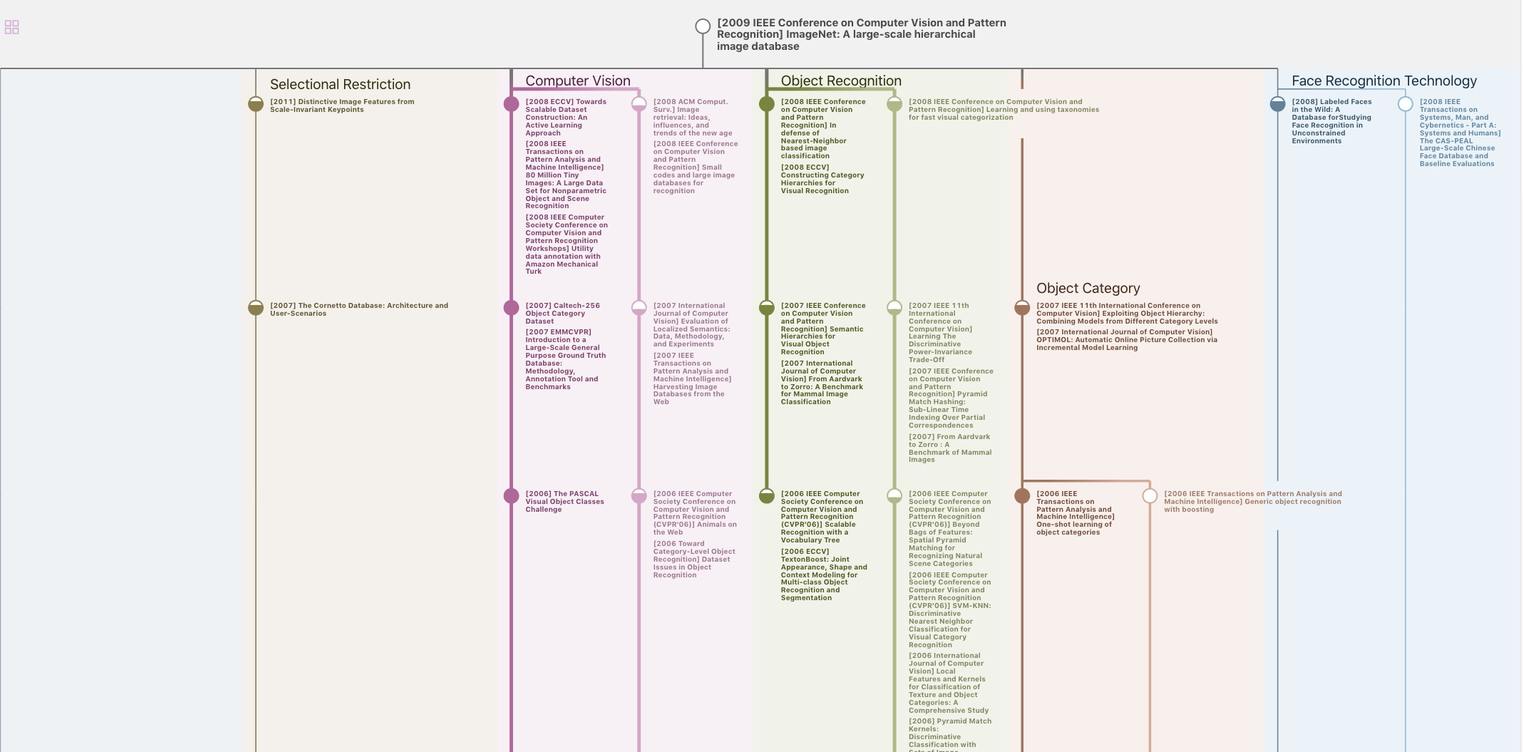
生成溯源树,研究论文发展脉络
Chat Paper
正在生成论文摘要