REGENERATIVE HYDRAULIC ASSISTED TURBOCHARGER
JOURNAL OF ENGINEERING FOR GAS TURBINES AND POWER-TRANSACTIONS OF THE ASME(2018)
摘要
Engine downsizing and down-speeding are essential in order to meet future U.S. fuel economy (FE) mandates. Turbocharging is one technology to meet these goals. Fuel economy improvements must, however, be achieved without sacrificing performance. One significant factor impacting drivability on turbocharged engines is typically referred to as "turbolag." Since turbolag directly impacts the driver's torque demands, it is usually perceptible as an undesired slow transient boost response or as a sluggish torque response. High throughput turbochargers (TC) are especially susceptible to this dynamic and are often equipped with variable geometry turbines (VGT) to mitigate some of this effect. Assisted boosting techniques that add power directly to the TC shaft from a power source that is independent of the engine have been shown to significantly reduce turbolag. Single unit assisted turbochargers are either electrically assisted or hydraulically assisted. In this study, a regenerative hydraulically assisted turbocharger (RHAT) system is evaluated. A custom-designed RHAT system is coupled to a light duty diesel engine and is analyzed via vehicle and engine simulations for performance and energy requirements over standard test cycles. Supplier-provided performance maps for the hydraulic turbine, hydraulic turbopump were used. A production controller was coupled with the engine model and upgraded to control the engagement and disengagement of RHAT, with energy management strategies. Results show some interesting dynamics and shed light on system capabilities especially with regard to the energy balance between the assist and regenerative functions. Design considerations based on open-loop simulations are used for sizing the high-pressure accumulator. Simulation results show that the proposed RHAT turbocharger system can significantly improve engine transient response. Vehicle level simulations that include the driveline were also conducted and showed potential for up to 4% fuel economy improvement over the FTP 75 drive cycle. This study also identified some technical challenges related to optimal design and operation of the RHAT. Opportunities for additional fuel economy improvements are also discussed.
更多查看译文
关键词
Battery Life Optimization
AI 理解论文
溯源树
样例
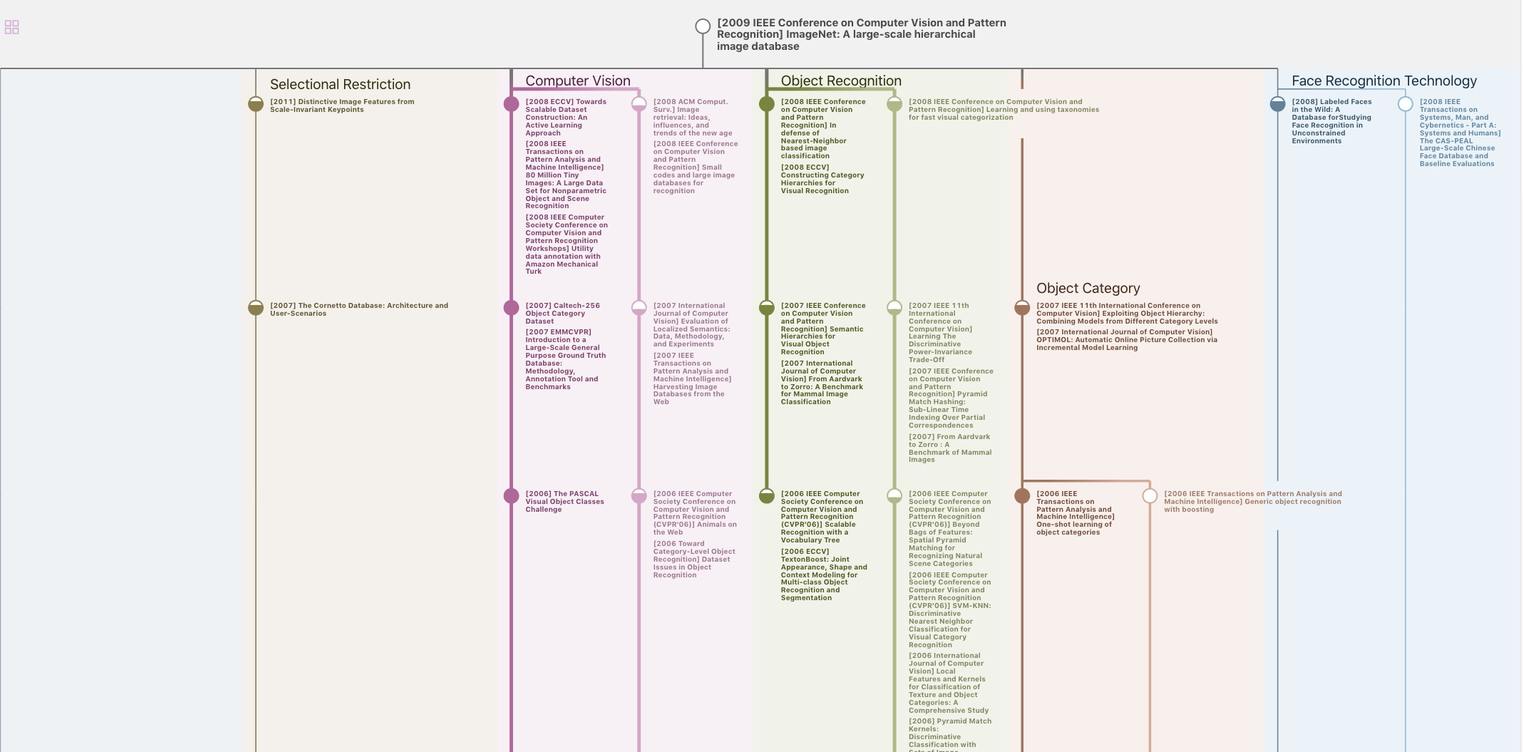
生成溯源树,研究论文发展脉络
Chat Paper
正在生成论文摘要