Effects of Dry Sliding Conditions on Wear Properties of Al-Matrix Composites Produced by Selective Laser Melting Additive Manufacturing
JOURNAL OF TRIBOLOGY-TRANSACTIONS OF THE ASME(2018)
摘要
The friction and wear properties of in situ Al-matrix composites prepared by selective laser melting (SLM) were evaluated on a ball-on-disk tribometer by sliding against GCr15 steel at room temperature. The influence of the applied load, sliding speed, and long-time continuous friction on the friction and wear properties of Al-matrix composites was systematically investigated. It showed that the wear rate and coefficient of friction (COF) increased when the applied load increased, due to the higher contact stress and larger extent of particle fracturing. As the sliding speed increased, the elevated rate of the formation of Al-oxide layer and the transfer of Fe-oxide layer from the counterface to the worn surface led to a significant reduction in wear rate and COF. As the sliding distance prolonged, the worn surface successively experienced the adhesive wear, the abrasive wear, the particle fracturing and crack nucleation, and the delaminated wear. The above processes were repeated on each exposed fresh surface, resulting in the fluctuation of COF. In the later stage of wear process, a large amount of oxides were produced on the worn surface, caused by the long-time accumulated frictional heat, which reduced the fluctuation of COF. The wear mechanisms of SLM-processed Al-matrix composite parts under various loads were dominated by abrasive wear and oxidation wear, whereas the predominant wear mechanisms were oxidation wear and delamination wear at different sliding speeds. For the long-time friction, all of these wear mechanisms were operational.
更多查看译文
关键词
selective laser melting,additive manufacturing,aluminum-matrix composites,dry sliding,friction and wear,sliding speed,wear mechanism
AI 理解论文
溯源树
样例
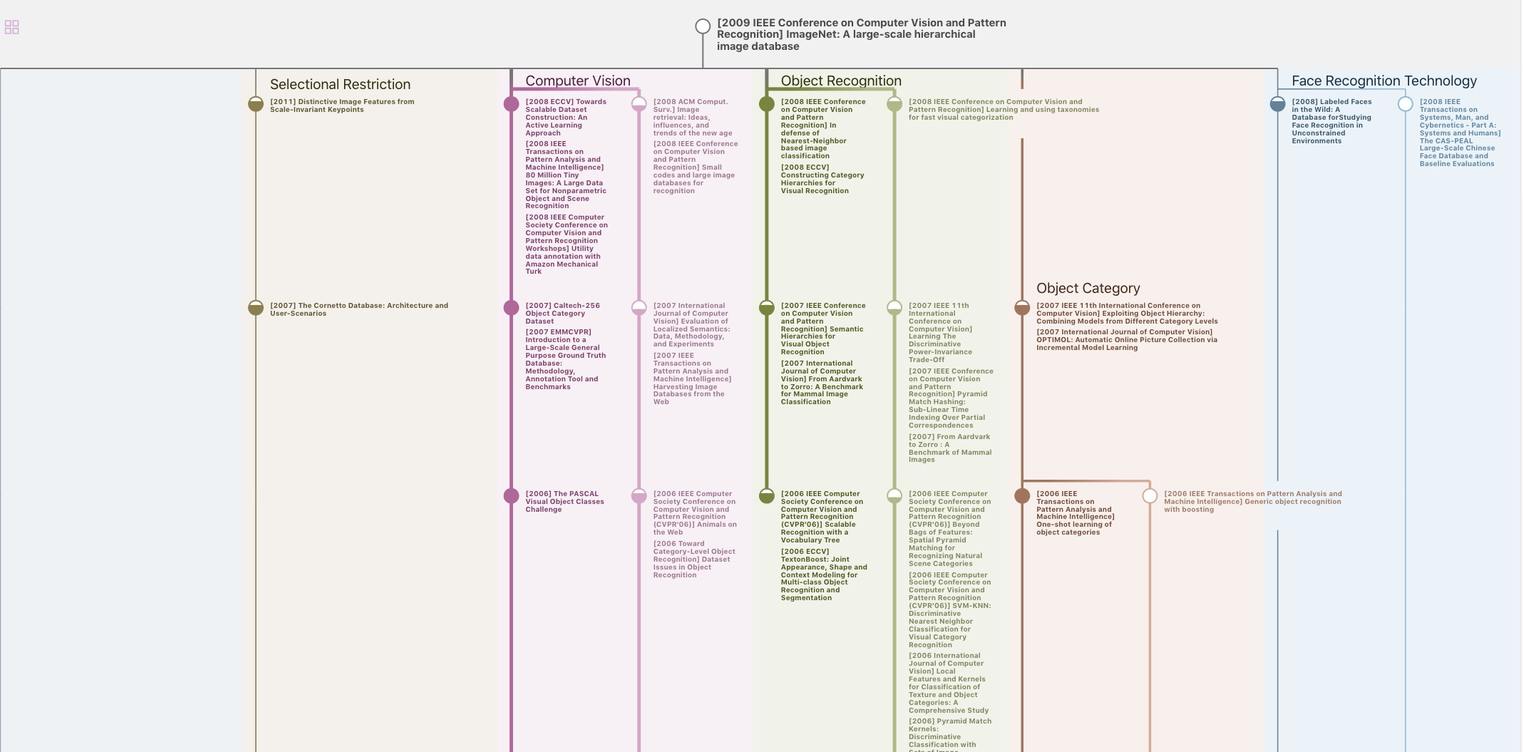
生成溯源树,研究论文发展脉络
Chat Paper
正在生成论文摘要