Research on layout and operational pose optimization of robot grinding system based on optimal stiffness performance
JOURNAL OF ADVANCED MECHANICAL DESIGN SYSTEMS AND MANUFACTURING(2017)
摘要
In a robot grinding system, the change of the robot's pose affects the overall stiffness of the whole machining system, which indirectly leads to the irregularity of the grinding surface. For this purpose, we propose a method to enhance the stiffness of the robot. The robot grinding system layout is usually based on the experience of the designer without any quantitative selection criteria. With the introduction of the stiffness performance evaluation index, we decouple the stiffness-couple relationship between the robot pose and layout of the robot system and calculate the value of the stiffness index for evaluating the performance of each layout point as a quantization selection basis. Using Rayleigh quotient as the stiffness performance evaluation index for the manipulator, we obtain a relationship between the stiffness performance and the installation position of the grinding tool. Based on the chosen layout point, we proposed the length of the semi axis along the direction of the grinding force in the stiffness ellipsoid as the optimization objective and obtain the optimal configuration in the entire processing workspace through a genetic algorithm method. Theoretical and numerical simulation is presented to demonstrate the effectiveness of the proposed approach. The results demonstrate that the optimization improves the stiffness performance significantly.
更多查看译文
关键词
Robot grinding system,Stiffness performance,Layout,Stiffness performance evaluation index,Robot configuration optimization
AI 理解论文
溯源树
样例
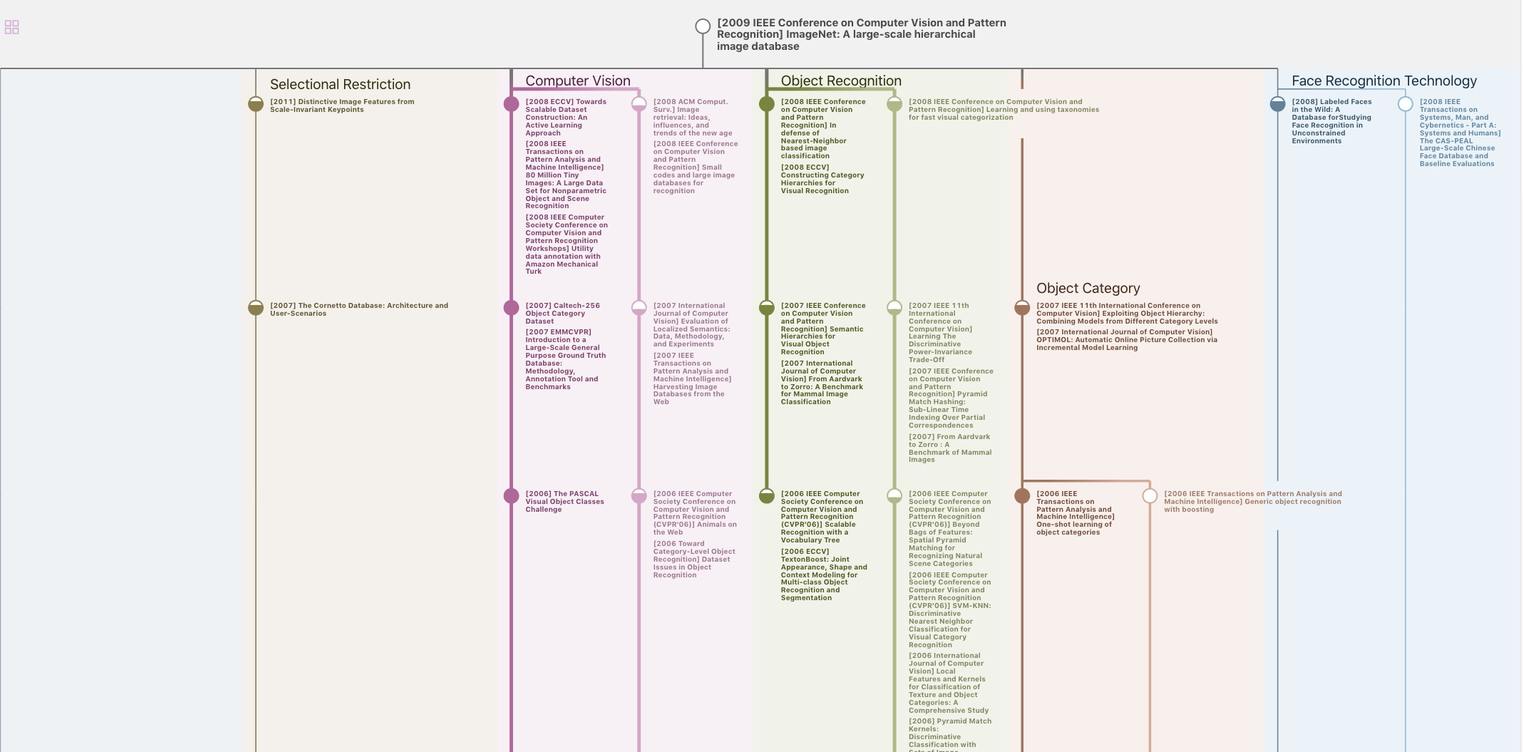
生成溯源树,研究论文发展脉络
Chat Paper
正在生成论文摘要