Analysis of Wear Particles Formed in Boundary-Lubricated Sliding Contacts
Tribology Letters(2016)
Abstract
The wear process in a sliding contact results in generation of wear debris, which affects the system life. The impact depends on the wear particle properties, such as size, shape and number. In this paper, the wear particles formed during a cylinder-on-disk wear test were examined. PAO additive-free oil, steel–brass and steel–steel contact pairs were employed. A particle isolation procedure was applied, and SEM/EDS analysis was used to validate it. DLS measurements indicated the wear particles radius to be in the range from 230 to 260 nm for both materials under applied nominal pressures from 87 to 175 MPa. AFM data revealed the wear particles size to be in the range from 133 to 175 nm. A slight increase in particles size with load was observed by AFM for both materials and confirmed by DLS for steel samples. AFM measurements were taken to determine thickness, length and width distributions of the wear particles. The number of wear particles per sliding distance and per unit load was estimated to be in the range from 150 to 750 particles/mm N for steel and approximately 1600–1900 particles/mm N for brass.
MoreTranslated text
Key words
Steel and brass wear particles, Dynamic light scattering, Atomic force microscopy
AI Read Science
Must-Reading Tree
Example
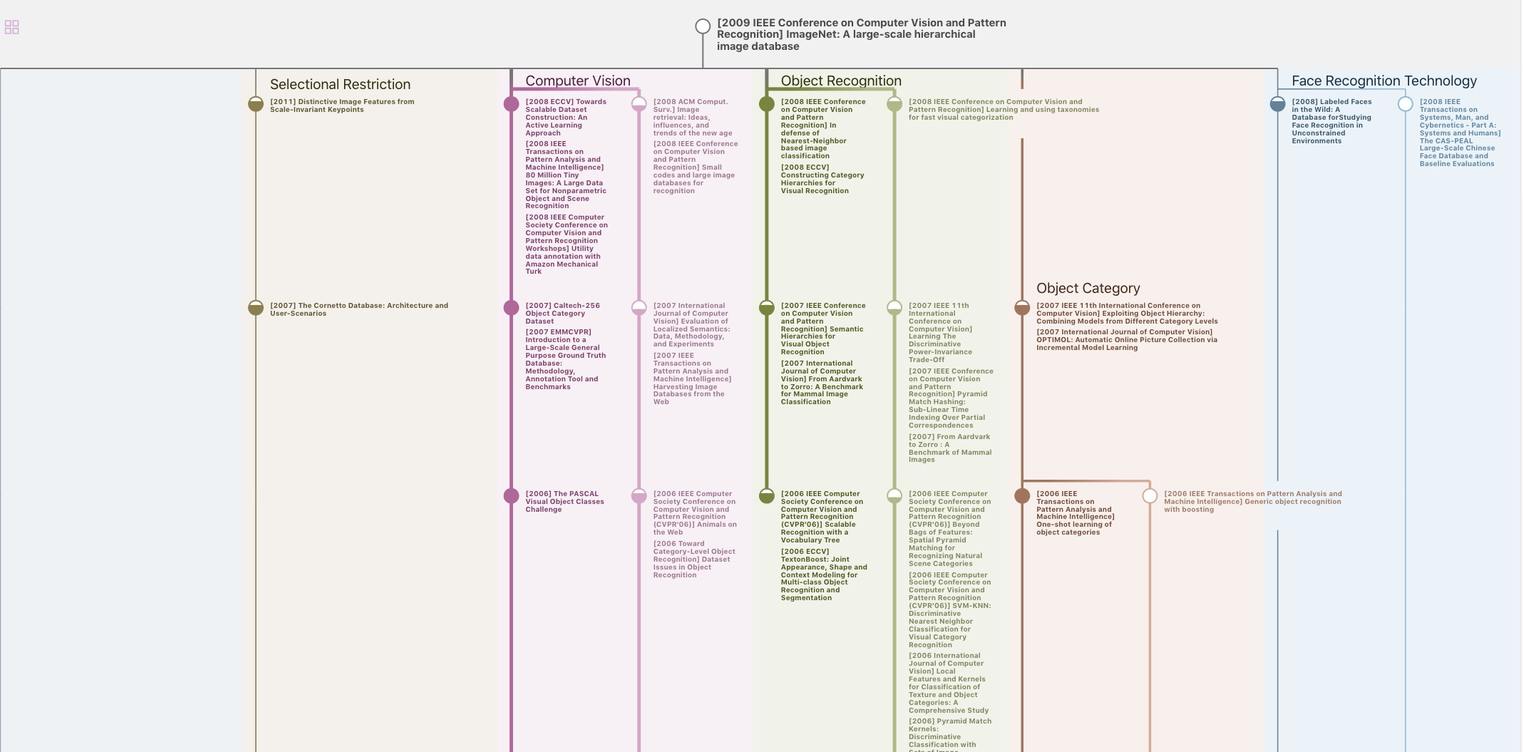
Generate MRT to find the research sequence of this paper
Chat Paper
Summary is being generated by the instructions you defined