Interim feature-based cutting parameter optimization for aircraft structural parts
The International Journal of Advanced Manufacturing Technology(2014)
摘要
The geometric state of a workpiece is changing dynamically during the machining process. Such geometric changes lead to changes of the rigidity of workpiece features. Knowing the feature rigidity during the machining process is very crucial for the selection of right cutting parameters especially for aircraft structural parts with complex structures. This issue has rarely been addressed in the literature for cutting parameter optimization. In order to address this issue, an interim feature concept is introduced and the interim feature is modeled by using geometric information of final state and machining process information for aircraft structural parts. The interim feature rigidity is evaluated by simplifying the structures of interim feature. By considering the constraints of the interim feature rigidity, machine tool characteristics, and cutting tool performance, the cutting parameters are optimized using a genetic algorithm. A prototype system is developed based on the proposed approach, and a case study is performed. The experiment results show that the machining efficiency can be improved by 26 % after cutting parameter optimization, while the same machining quality is maintained.
更多查看译文
关键词
Cutting parameter optimization, Interim feature, Aircraft structural part, Genetic algorithm, Rigidity
AI 理解论文
溯源树
样例
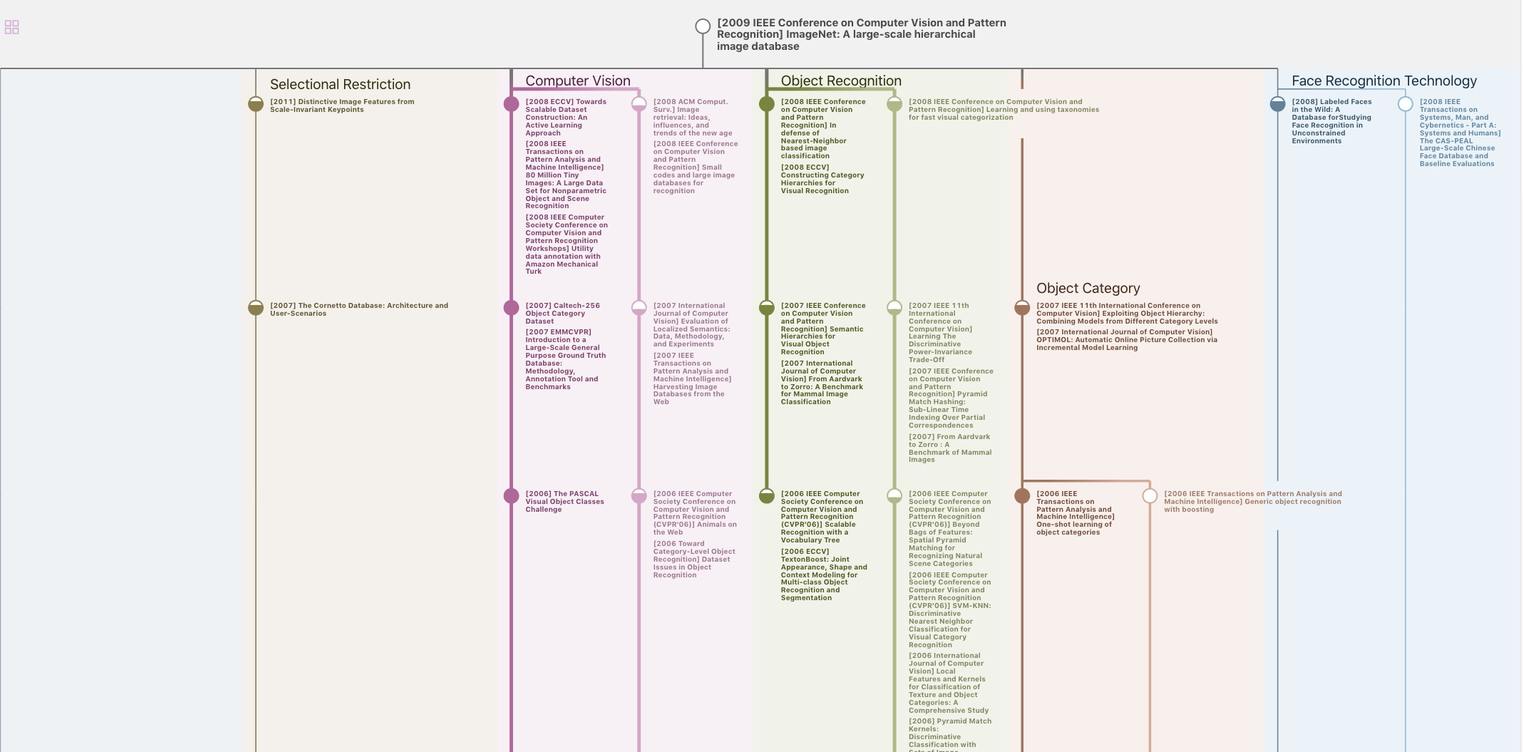
生成溯源树,研究论文发展脉络
Chat Paper
正在生成论文摘要