Effect Of Mesh Structure In The Kiva-4 Code With A Less Mesh Dependent Spray Model For Dl Diesel Engine Simulations
SAE INTERNATIONAL JOURNAL OF ENGINES(2009)
摘要
Two different types of mesh used for diesel combustion with the KIVA-4 code are compared. One is a well established conventional KIVA-3 type polar mesh. The other is a non-polar mesh with uniform size throughout the piston bowl so as to reduce the number of cells and to improve the quality of the cell shapes around the cylinder axis which can contain many fuel droplets that affect prediction accuracy and the computational time. This mesh is specialized for the KIVA-4 code which employs an unstructured mesh. To prevent dramatic changes in spray penetration caused by the difference in cell size between the two types of mesh, a recently developed spray model which reduces mesh dependency of the droplet behavior has been implemented. For the ignition and combustion models, the Shell model and characteristic time combustion (CTC) model are employed. The calculated spatial distribution of droplets, fuel vapor and soot are compared against high-speed in-cylinder imaging obtained from an optical access diesel engine. Heat release rate, NOx, soot and computational time are also compared between the two types of mesh. The results show that the uniform-sized mesh reduces computational times significantly while maintaining almost the same prediction accuracy as the KIVA-3 type polar mesh.
更多查看译文
关键词
mesh dependent spray model,diesel engine,mesh structure,simulations
AI 理解论文
溯源树
样例
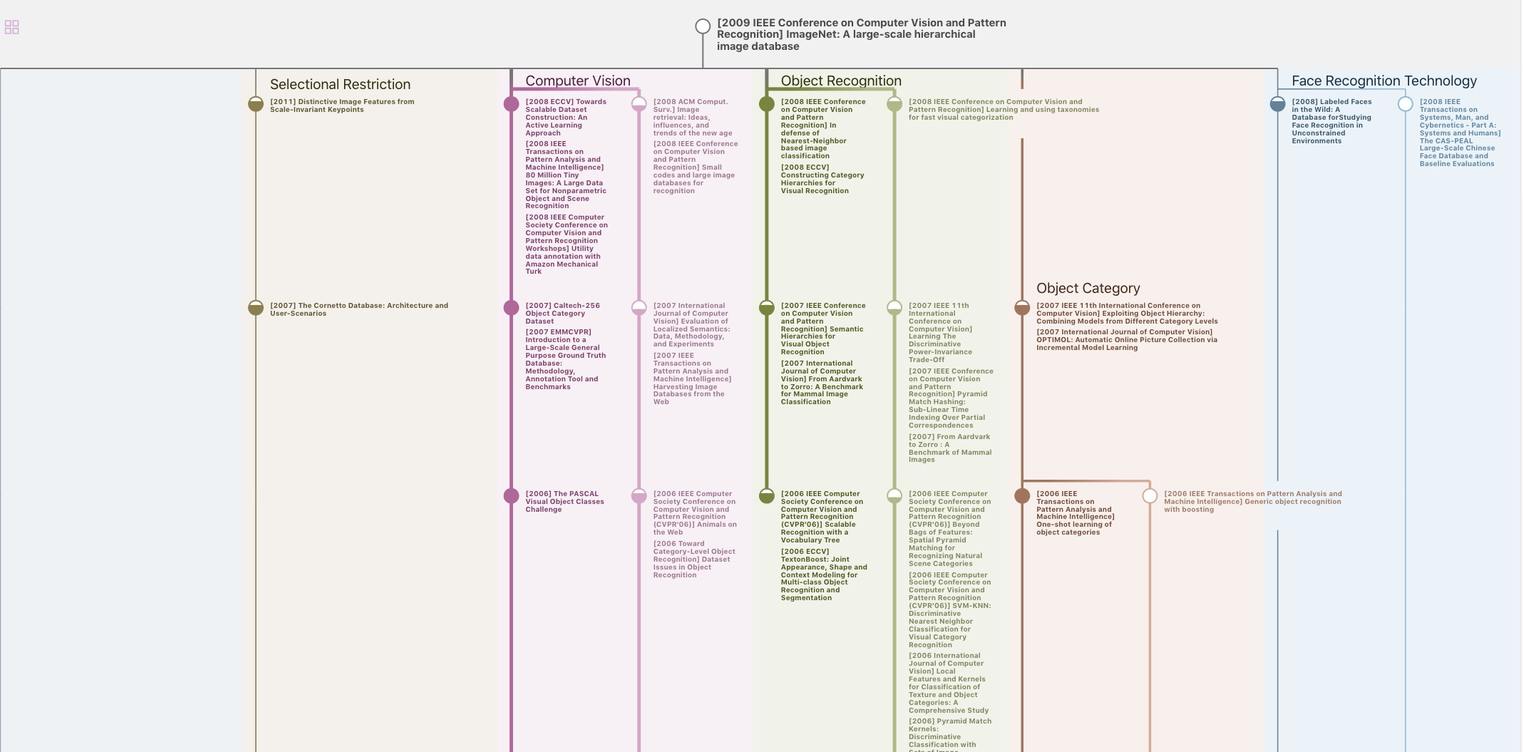
生成溯源树,研究论文发展脉络
Chat Paper
正在生成论文摘要