Improving the Thermal Performance of a Forced Convection Air Cooled Solution: Part 1 — Modification of Heat Sink Assembly
PROCEEDINGS OF THE ASME INTERNATIONAL TECHNICAL CONFERENCE AND EXHIBITION ON PACKAGING AND INTEGRATION OF ELECTRONIC AND PHOTONIC MICROSYSTEMS, 2013, VOL 2(2013)
摘要
Forced convection air cooling using heat sinks is one of the most prevalent methods in thermal management of microelectronic devices. Improving the performance of such a solution may involve minimizing the external thermal resistance. (R-ext) of the package. For a given heat sink design, this can be achieved by reducing the thermal interface material (TIM) thickness through promotion of a uniform interfacial pressure distribution between the device and heat sink. In this study, a dual-CPU rackmount server is considered and modifications to the heat sink assembly such as backplate thickness and bolting configuration are investigated to achieve the aforementioned improvements. A full-scale, simplified model of the motherboard is deployed in ANSYS Mechanical, with emphasis on non-linear contact analysis and torque analysis of spring screws, to determine the optimal design of the heat sink assembly. It is observed that improved interfacial contact and pressure distribution is achieved by increasing the number of screws (loading points) and positioning them as close to the contact area as possible. The numerical model is validated by comparison with experimental measurements within reasonable accuracy. Based on the results of numerical analysis, the heat sink assembly is modified and improvement over the base configuration is experimentally quantified through interfacial pressure measurement. The effect of improved interfacial contact on thermal performance of the solution is discussed.
更多查看译文
关键词
Server, back plate, interfacial pressure, TIM performance, mechanical analysis
AI 理解论文
溯源树
样例
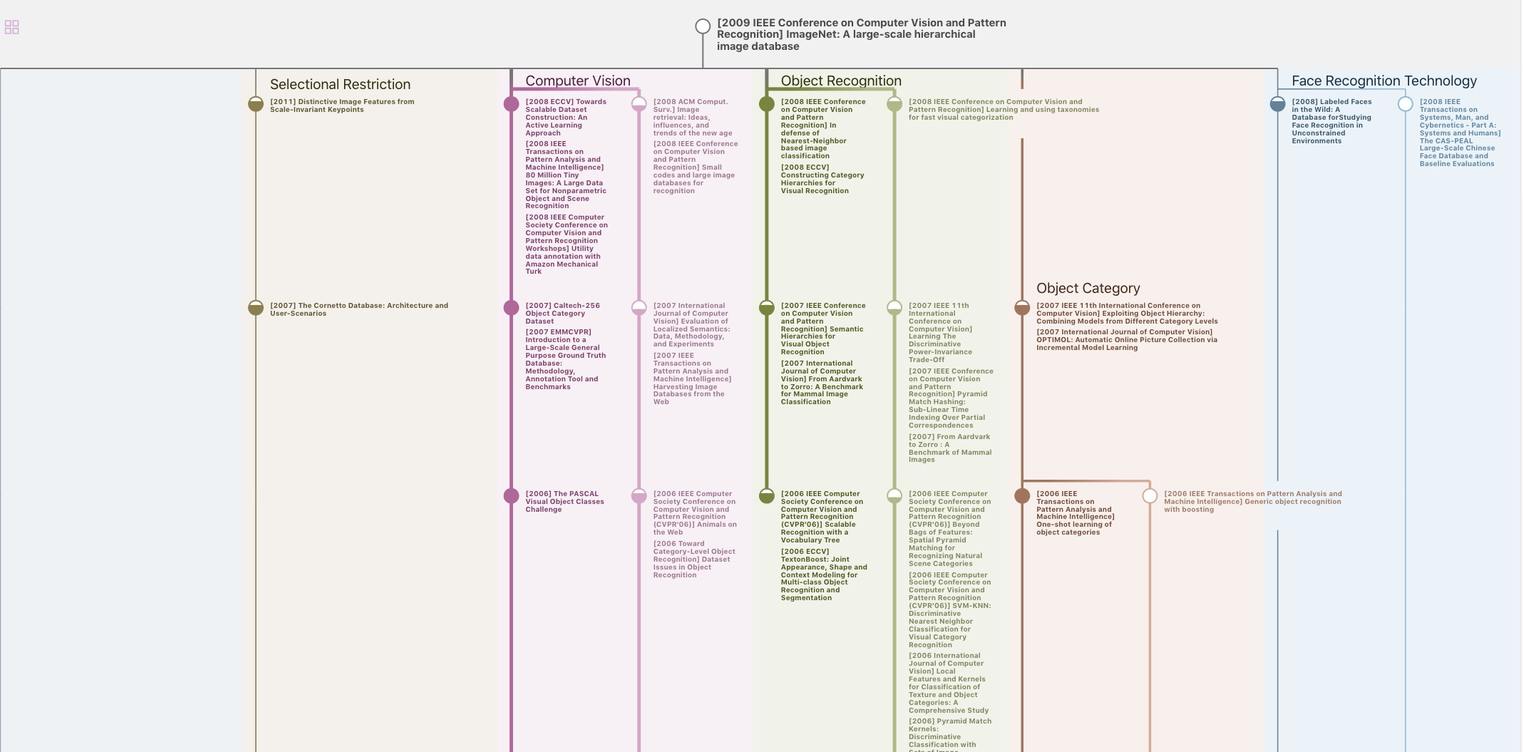
生成溯源树,研究论文发展脉络
Chat Paper
正在生成论文摘要