Solid Modeling Of In-Process Workpiece Geometry For Hole Milling
PROCEEDINGS OF THE ASME INTERNATIONAL DESIGN ENGINEERING TECHNICAL CONFERENCES AND COMPUTERS AND INFORMATION IN ENGINEERING CONFERENCE 2012, VOL 2, PTS A AND B(2012)
Abstract
Capturing the in-process workpiece geometry generated during machining is an important part of tool path verification and increasingly the physics-based simulation of cutting forces used in Virtual Machining. Swept volume generation is a key supporting methodology that is necessary for generating these in-process states. Hole milling is representative of one class of milling operation where the swept volume is continuously intersecting. Due to this it is impossible to decompose the tool path into non-intersecting regions which is typically the approach used in solid model based swept volume generation. In this paper an approach to generating NURBS based solid models for self-intersecting swept volumes generated during hole milling is presented. NURB surfaces are generated that compactly represent the surfaces of the swept volume. This utilizes the geometry of the helical curve as opposed to a linearly interpolated tool path that is used for more generic approaches to generating swept volumes. Examples applying the approach to various types of cutter geometries used in milling are presented.
MoreTranslated text
Key words
Virtual Machining,Cufter/Workpiece Engagements,Helical Milling,Swept Volumes
AI Read Science
Must-Reading Tree
Example
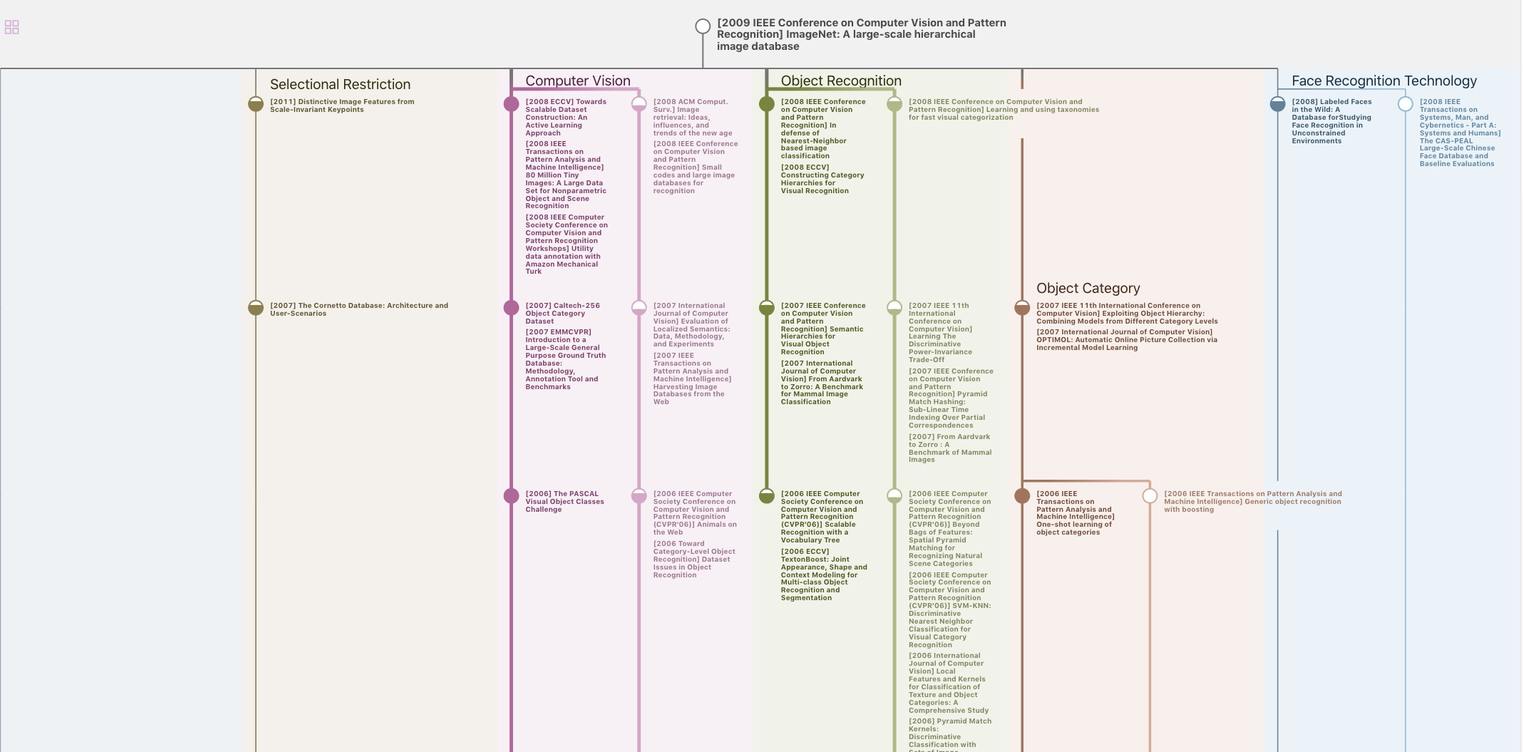
Generate MRT to find the research sequence of this paper
Chat Paper
Summary is being generated by the instructions you defined