Microporous Coatings and Enhanced Critical Heat Flux for Downward Facing Boiling During Passive Emergency Reactor Cooling
JOURNAL OF PRESSURE VESSEL TECHNOLOGY-TRANSACTIONS OF THE ASME(2017)
Abstract
During a reaction-initiated accident (RIA) or loss of coolant accident (LOCA), passive external-cooling of the reactor lower head is a viable approach for the in-vessel retention (IVR) of Corium; while this concept can certainly be applied to new constructions, it may also be viable for operational systems with existing cavities below the reactor. However, a boiling crisis will inevitably develop on the reactor lower head owing to the occurrence of critical heat flux (CHF) that could reduce the decay heat removal capability as the vapor phase impedes continuous boiling. Fortunately, this effect can be minimized for both new and existing reactors through the use of a cold-spray-delivered, microporous coating that facilitates the formation of vapor microjets from the reactor surface. The microporous coatings were created by first spraying a binary mixture with the sacrificial material then removed via etching. Subsequent quenching experiments on uncoated and coated hemispherical surfaces showed that local CHF values for the coated vessel were consistently higher relative to the bare surface. Moreover, it was observed for both coated and uncoated surfaces that the local rate of boiling and local CHF limit varied appreciably along the outer surface. Nevertheless, the results of this intriguing study clearly show that the use of cold spray coatings could enhance the local CHF limit for downward facing boiling by more than 88%. Moreover, the cold-spray process is amenable to coating the lower heads of operating reactors.
MoreTranslated text
Key words
downward-facing boiling,CHF limit,cold spray,microporous coating,IVR
AI Read Science
Must-Reading Tree
Example
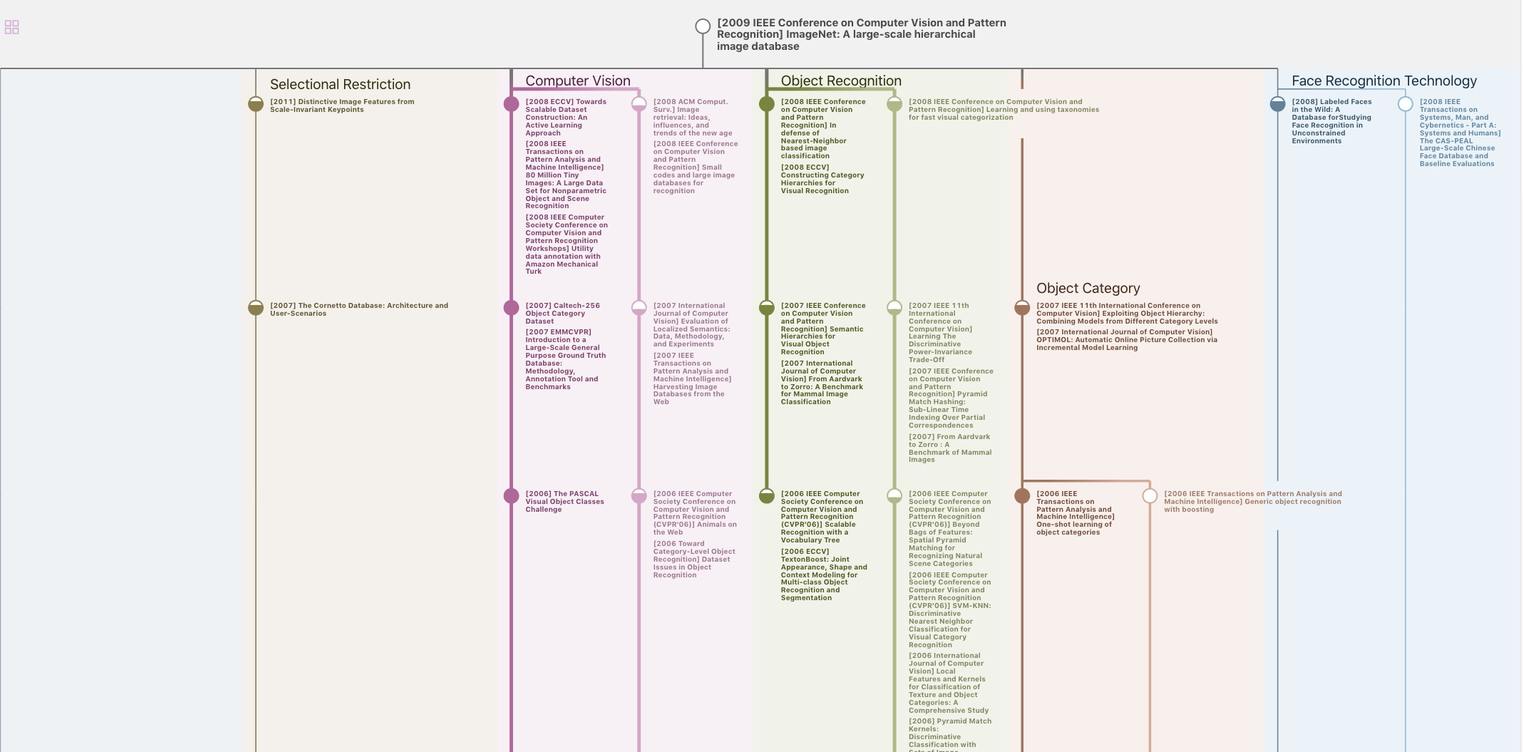
Generate MRT to find the research sequence of this paper
Chat Paper
Summary is being generated by the instructions you defined