Extrusion of hybrid sheet metals
Journal of Materials Processing Technology(2012)
Abstract
This study focused on the extrusion of hybrid sheet metals. Co-extrusion of profiles having sheet metals as reinforcing elements are a promising alternative to the more common rotation-symmetric composite rods or wire reinforced profiles. The influence of non-rotation-symmetric die geometry was investigated by extruding aluminum alloy billets with three different types of sheet metals as core material and the aluminum alloy (AlMgSi1 EN AW-6082) as sleeve material. The hybrid sheet metals were analyzed by non-destructive testing using ultrasonic testing and X-ray inspection. The steel (DC 06) and the titanium (titanium grade 1) cores fractured during extrusion, while the magnesium alloy core (AZ31) showed a uniform deformation. A new deformation mode in co-extrusion has been found for the titanium grade 1 core which most likely fractured due to a combination of tensile and shear stresses caused by the material flow of the non-symmetrical cross-section of the profile. The DC 06 core predominantly fractured due to tensile stresses. Microstructural analysis showed a decrease in thickness for all cores, with AZ31 showing the highest reduction and DC 06 the lowest. It was found that no intermetallic phases occurred having a DC 06 or titanium grade 1 core. However, EDX line scans indicated the start of diffusion processes at the interphase of EN AW-6082 and DC 06. An intermetallic phase could be observed for the specimens having an AZ31 core, EDX line scans showed this to be the Al3Mg2 (β) phase.
MoreTranslated text
Key words
Extrusion,Hybrid materials,Sheet metal,Non-destructive testing,Intermetallic phase,Characterization
AI Read Science
Must-Reading Tree
Example
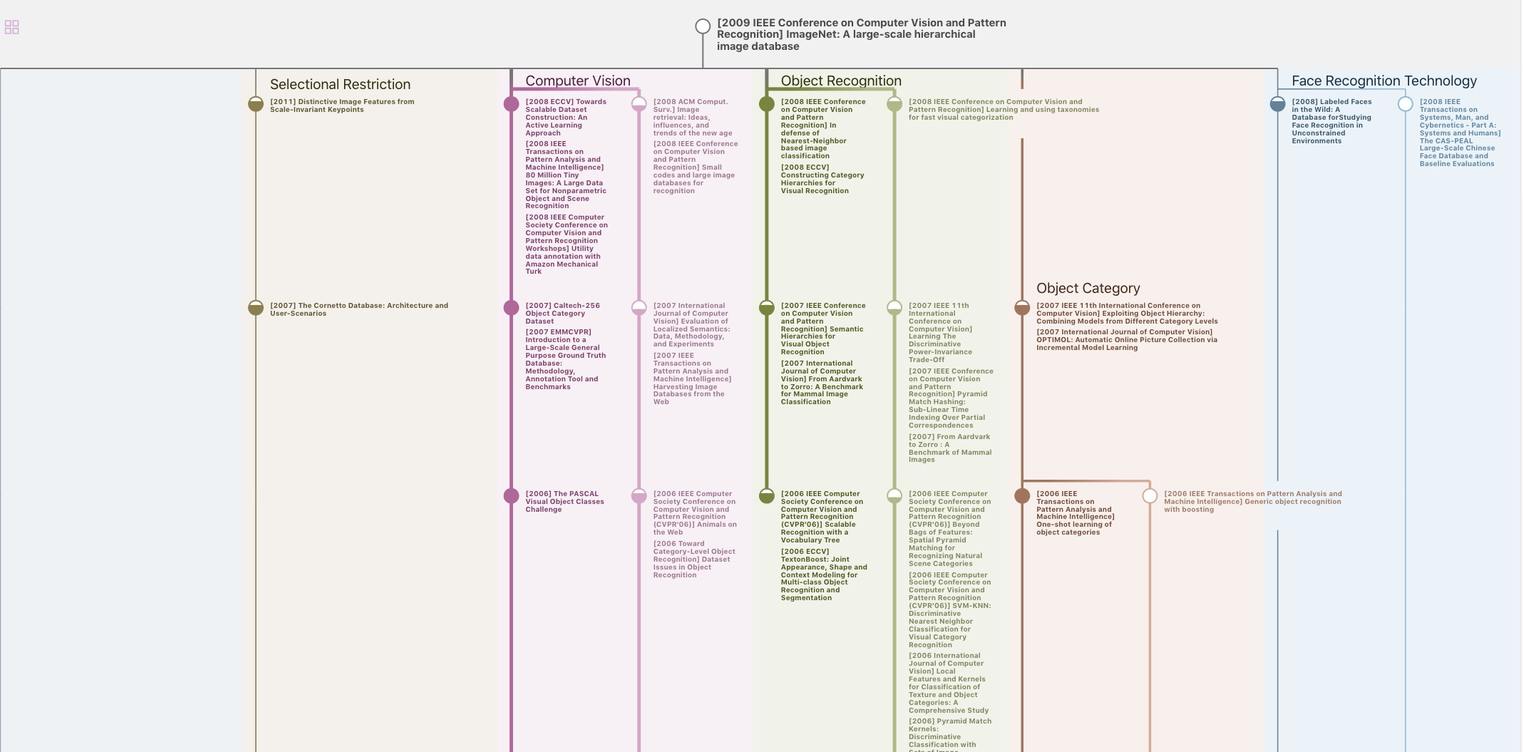
Generate MRT to find the research sequence of this paper
Chat Paper
Summary is being generated by the instructions you defined