Tool electrode wear compensation in block divided EDM process for improving accuracy of diffuser shaped film cooling holes
INTERNATIONAL JOURNAL OF ADVANCED MANUFACTURING TECHNOLOGY(2019)
摘要
Diffuser shaped film cooling holes are increasingly being applied in the turbine blades of advanced aeroengines. It is a difficult problem to machine this kind of cooling holes due to their complicated shape and superalloy material. Currently, die-sinking electrical discharge machining (EDM) is regarded as an available process for machining the diffuser holes. However, the change of tool electrode shape caused by the electrode wear and difficult renew of dielectric fluid affect the processing precision. The worn tool electrode has to be replaced with a fresh one after machining one or several holes. The replacing procedure is time consuming to break the machining process. In the previous work, a novel block divided EDM process was proposed to efficiently machine the diffuser holes, but the machining accuracy needs to be further improved. In this research, the block divided EDM process firstly is analyzed and simulated in detail to know the key factor affecting the machined accuracy. Furthermore, a self-repair method and a profile error compensation method of the tool electrode wear are proposed for improving the processing accuracy. The self-repair method is to plan and control the rotation motion of the tool electrode for maintaining its shape. The profile error compensation method is to modify the Z coordinate of the tool electrode for decreasing the machining error. Machining experiments verified that the proposed methods can meet the accuracy requirements of the film cooling holes with diffusion angle error < 0.1° and average profile error < 10 μm.
更多查看译文
关键词
Block divided EDM process,Diffuser shaped film cooling hole,Tool electrode wear and self-repair,Error compensation
AI 理解论文
溯源树
样例
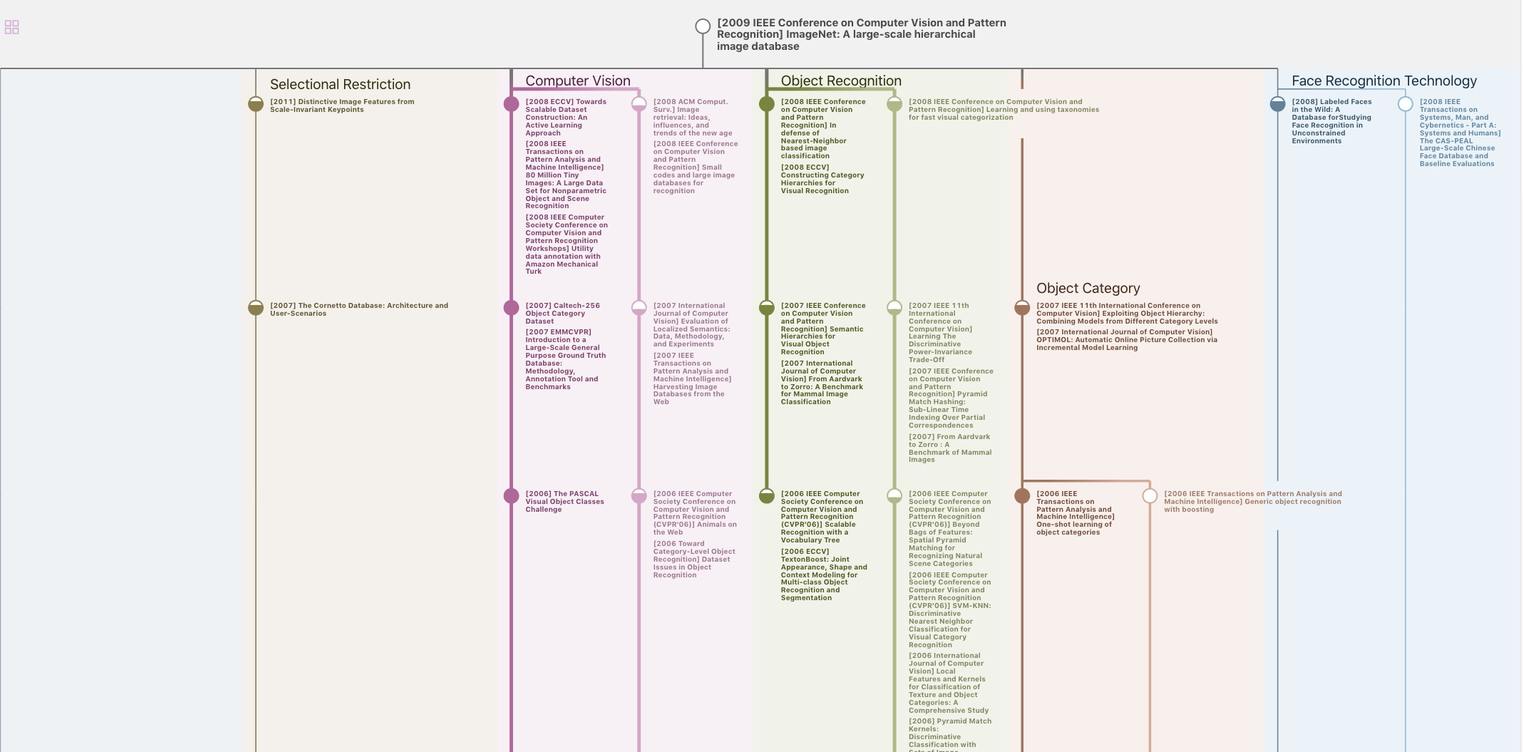
生成溯源树,研究论文发展脉络
Chat Paper
正在生成论文摘要