Potential and challenges of a solid-shell element for the macroscopic forming simulation of engineering textiles
ESAFORM 2021(2021)
Abstract
Finite element (FE) forming simulation offers the possibility of a detailed analysis of the deformation behaviour of engineering textiles during forming processes, to predict possible manufacturing effects such as wrinkling or local changes in fibre volume content. The majority of macroscopic simulations are based on conventional two-dimensional shell elements with large aspect ratios to model the membrane and bending behaviour of thin fabrics efficiently. However, a three-dimensional element approach is necessary to account for stresses and strains in thickness direction accurately, which is required for processes with a significant influence of the fabric’s compaction behaviour, e.g. wet compression moulding. Conventional linear 3D-solid elements that would be commercially available for this purpose are rarely suitable for high aspect ratio forming simulations. They are often subjected to several locking phenomena under bending deformation, which leads to a strong dependence of the element formulation on the forming behaviour [1]. Therefore, in the present work a 3D hexahedral solid-shell element, based on the initial work of Schwarze and Reese [2,3], which has shown promising results for the forming of thin isotropic materials [1], is extended for highly anisotropic materials. The advantages of a locking-free element formulation are shown through a comparison to commercially available solid and shell elements in forming simulations of a generic geometry. Additionally, first ideas for an approach of a membrane-bending-decoupling based on a Taylor approximation of the strain are discussed, which is necessary for an accurate description of the deformation behaviour of thin fabrics.
MoreTranslated text
Key words
solid-shell
AI Read Science
Must-Reading Tree
Example
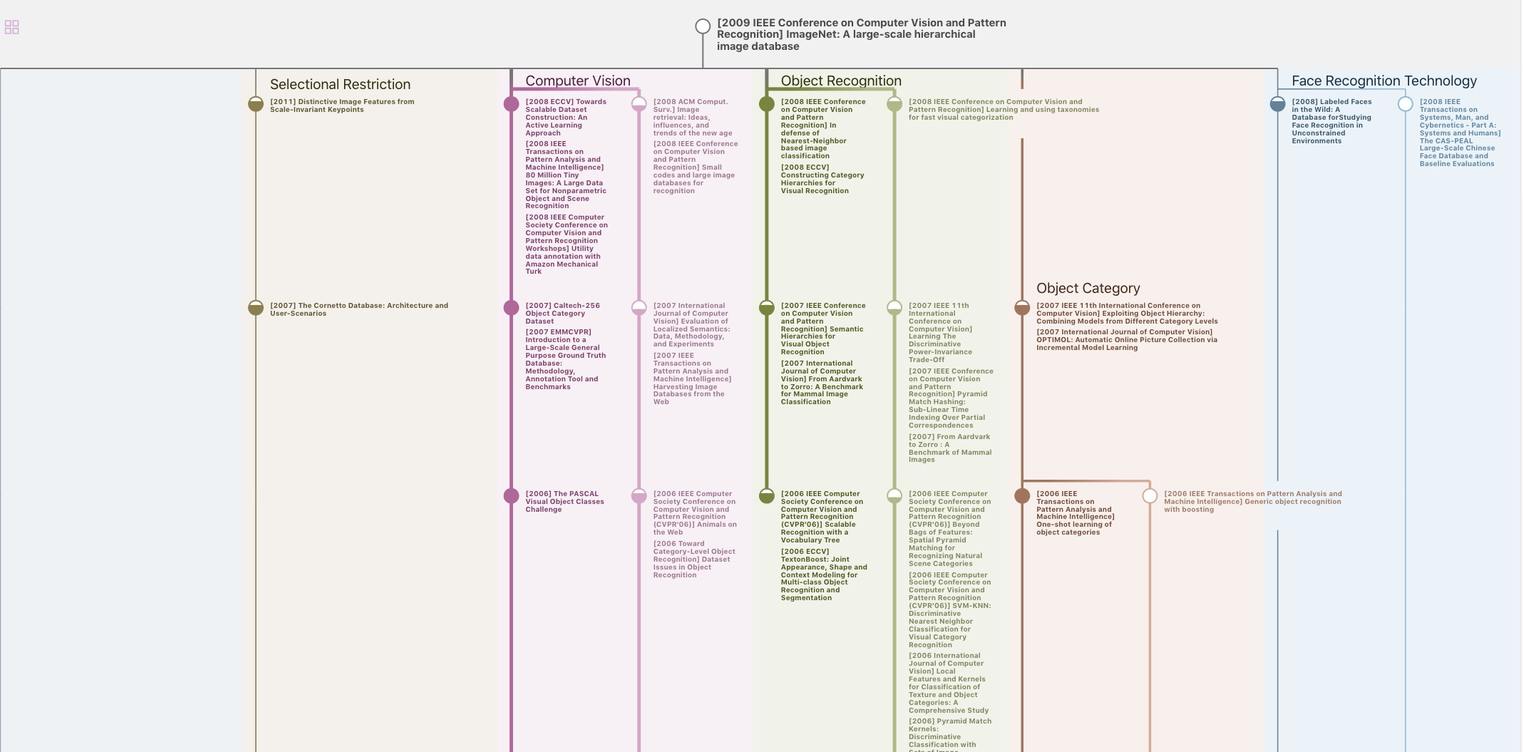
Generate MRT to find the research sequence of this paper
Chat Paper
Summary is being generated by the instructions you defined