Integrated optimization design for a radial turbine wheel of a 100 kW-class microturbine
JOURNAL OF ENGINEERING FOR GAS TURBINES AND POWER-TRANSACTIONS OF THE ASME(2012)
摘要
The aerodynamic performance, structural strength, and wheel weight are three important factors in the design process of the radial turbine. This paper presents an investigation on these aspects and develops an optimization design approach for radial turbine with consideration of the three factors. The aerodynamic design for the turbine wheel with an inlet diameter of 230 mm for the 100 kW-class microturbine unit is carried out first as the original design. Then, the cylinder parabolic geometrical design method is applied to the wheel modeling and structural design, but the maximum stress predicted by finite element analysis greatly exceeds the yield limit of material. Further, the wheel weight is above 7.2 kg, thus, bringing some critical difficulties for bearing design and turbine operation. Therefore, an integrated optimization design method for radial turbine is studied and developed in this paper with focus on the wheel design. Meridional profiles and shape lines of the turbine wheel are optimized with consideration of the whole wheel weight. Main structural modeling parameters are reselected to reduce the wheel weight. Trade-off between aerodynamic performance and strength performance is highly emphasized during the optimization design. The results show that the optimized turbine wheel gets high aerodynamic performance and acceptable stress distribution with a weight less than 3.8 kg. [DOI: 10.1115/1.4004162]
更多查看译文
关键词
optimization,design
AI 理解论文
溯源树
样例
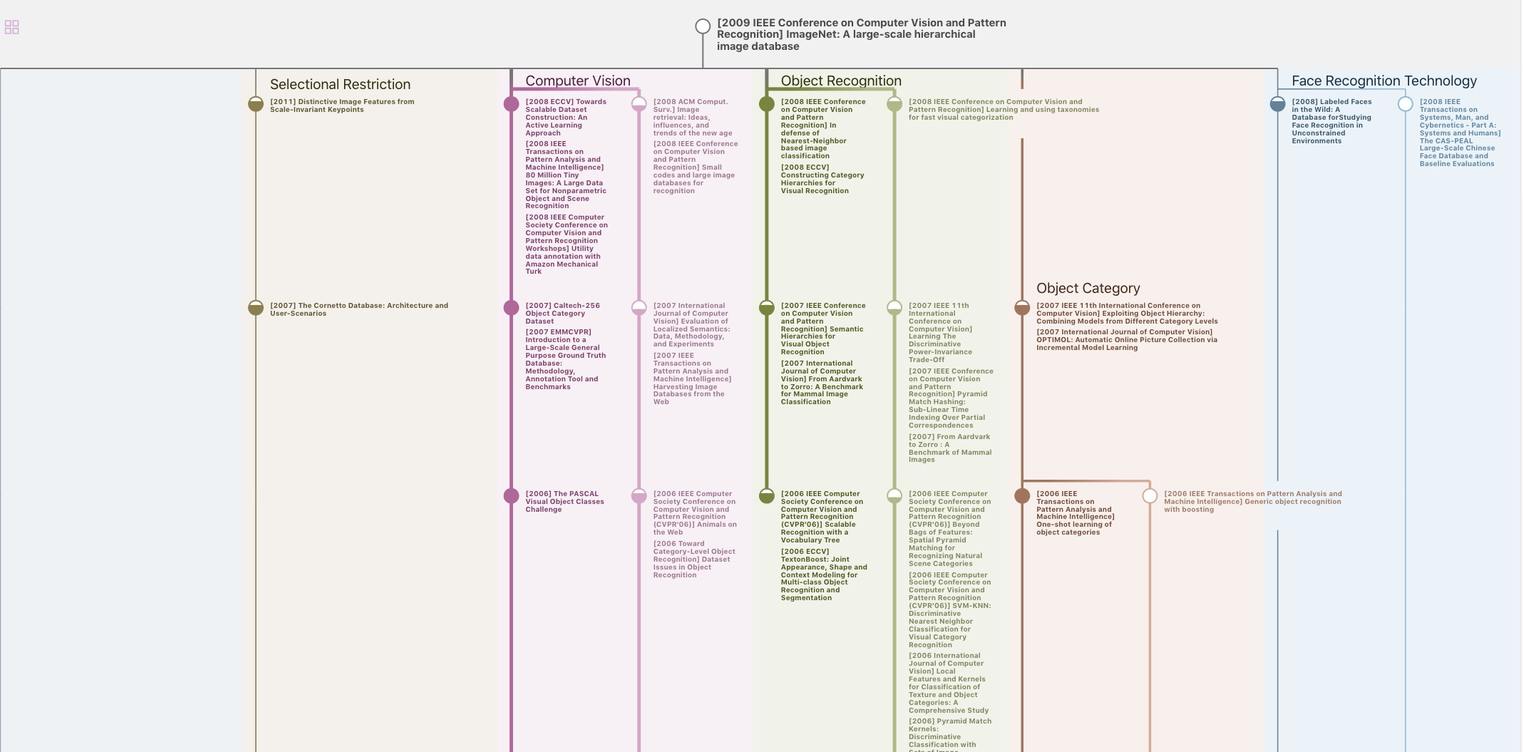
生成溯源树,研究论文发展脉络
Chat Paper
正在生成论文摘要