A novel method for preparation of macroposous lithium nickel manganese oxygen as cathode material for lithium ion batteries
Electrochimica Acta(2011)
摘要
A simple one-step route using gas template method is applied to synthesize macroporous LiNi 0.5 Mn 0.5 O 2 which is characterized by powder X-ray diffraction (XRD), scanning electron microscopy (SEM), Brunauer–Emmett–Telle (BET) surface area, charge–discharge tests and electrochemical impedance spectroscopy (EIS) measurements. The as-synthesized material shows pure crystalline phase of LiNi 0.5 Mn 0.5 O 2 , while the microstructure is comprised of macrospores ranging from 0.2 to 0.5 μm. The first discharge capacity is of 174 mAh g −1 at 0.1 C rate, which is much higher than that of the material synthesized by the conventional solid state reaction method. Furthermore, the macroporous LiNi 0.5 Mn 0.5 O 2 material shows remarkable rate capacity and cycle stability, which may be attributed to the shorter lithium ion diffusion distance and better electrolyte penetration. Keywords Macroporous Rate capacity Lithium manganese nickel oxide Lithium ion battery Cathode materials 1 Introduction Since today's prevalence of microelectronic devices, there is an urgent need for power supplies with higher energy and power densities. Lithium ion battery is a promising candidate that meets these requirements. The positive electrode material plays an important role in the electrochemical performance of a lithium ion battery. Layered LiNi 0.5 Mn 0.5 O 2 attracts a lot of attention because it has advantage such as being cheaper, safer and capable of providing a higher capacity than LiCoO 2 [1] . The main drawback, however, limits its wide application is its poor conductivity [2–5] . Two popular methods to improve the performance of LiNi 0.5 Mn 0.5 O 2 as a cathode material for lithium ion batteries are to coat the particles with electronic conductivity agents such as carbon and to modify its micro-morphology. However, the process of both carbon coating and nano-sized particle synthesis is quite complicated [6–9] . In addition, although nano-particulate positive electrodes can improve rate capacity by decreasing lithium ion diffusion distance, such an improvement is achieved at the expense of volumetric energy density, because lower density of nanoparticulate-based electrodes means greater volume [10–12] . Recently some groups reported that the porous structure can meliorate the rate capacity remarkably. Ergang et al. proved that LiCoO 2 with a macroporous structure was effective in decreasing the solid-state diffusion length within the electrode, thereby improving its rate capacity [10] . Furthermore, Kuthanapillil et al. reported that Li(Ni 1/3 Co 1/3 Mn 1/3 )O 2 with a macroporous structure delivered high storage capacity, superior capacity retention and power rate [12] . These results obviously serve to illustrate the important role of morphology in determining the performance of cathode materials in lithium ion batteries. In this paper, a novel approach is proposed to synthesis layered LiNi 0.5 Mn 0.5 O 2 with a macroporous structure and its electrochemical performance is investigated as a cathode material for lithium ion batteries. 2 Experimental 2.1 Preparation of LiNi 0.5 Mn 0.5 O 2 Macroporous LiNi 0.5 Mn 0.5 O 2 was synthesized by dissolving LiCH 3 COO·2H 2 O, Ni(CH 3 COO) 2 ·4H 2 O and Mn(CH 3 COO) 2 ·4H 2 O in quantities corresponding to 0.02 mol of stoichiometric LiNi 0.5 Mn 0.5 O 2 in 100 mL of water containing 0.15 mol of formaldehyde (36.5% in water, methanol stabilized), 0.1 mol of resorcinol (99%) and 0.5 × 10 −3 mol of Li 2 CO 3 serve as 5 mol% excess of Li source. The obtained solution was heat-treated at 60 °C until viscous and then baked at 90 °C for 24 h, followed by calcination at 900 °C for 10 h. For comparison, conventional solid state reaction method was used to synthesize LiNi 0.5 Mn 0.5 O 2 by mixing a stoichimetric amount of Mn(CH 3 COO) 2 ·4H 2 O, Ni(CH 3 COO) 2 ·4H 2 O and C 2 H 2 O 4 ·2H 2 O (molar ratio of Ni: Mn: oxalic acid is 1:1:2) and sintering at 900 °C. All the procedures were carried out in ambient atmosphere and all the raw materials are analytical reagents which were purchased from Shanghai Chemical Company and used without any further purification. 2.2 Characterizations The XRD measurement was carried out on a Bruker D8 Advance X-ray diffraction using Cu Kα radiation source ( λ = 1.5406 Å) with a scan rate of 1 ° min −1 from 10 to 80 °. Lattice parameters of the materials and the ratio of Li/Ni exchange in the structure were calculated and refined by Rietveld analysis (Accelrys MS Modeling 3.0.1). Morphological studies were conducted using a JEOL JMS 6390 scanning electron microscope. BET surface area measurement was carried out on an automated surface area and pore size analyzer (QUDRASORB SI, Quantachrome Instruments U.S.). 2.3 Electrochemical measurement To evaluate electrochemical performance, composite electrodes were constructed by mixing the active materials, super P carbon black and polytetrafluoroethylene (PTFE) in the weight ratio of 70:20:10. The mixture was rolled into a thin sheet with uniform thickness and then pressed onto an aluminum mesh. The cathode was circular with a 10 mm diameter and dried under vacuum at 120 °C for 24 h. Typical loading of the active material was 0.0127 g cm −2 . The test cell was assembled in an argon-filled glove box with lithium pellet as anode, a Celgard 2300 sheet as separator and 1 M LiPF 6 in a mixed ethylene carbonate (EC)/dimethyl carbonate (DMC) (1:1 in volume) solution as electrolyte. The charge–discharge measurements were carried out in a potential range from 2.5 to 4.3 V (vs. Li + /Li) using a Land Cycler (Wuhan Land Electronic Co. Ltd.). The electrochemical impedance spectroscopy (EIS) measurements were performed on an electrochemical workstation (CHI 660A, CHI Company). The frequency was ranged from 0.01 to 100,000 Hz with an amplitude of 0.005 V. All the tests were performed at room temperature. 3 Results and discussion 3.1 Structure characterization Fig. 1 presents powder XRD patterns of the as-synthesized LiNi 0.5 Mn 0.5 O 2 and LiNi 0.5 Mn 0.5 O 2 obtained by conventional solid state reaction method. All the peaks are attributed to layered structure of α-NaFeO 2 with a R-3m space group and no other peaks are observed, which indicates that pure layered LiNi 0.5 Mn 0.5 O 2 was obtained. The sharp peaks indicate excellent crystalline of those materials. The influence of Li/Ni exchange to the lattice structure which has an important relationship to the electrochemical performance of LiNi 0.5 Mn 0.5 O 2 was previously reported [2,13–17] . The intensity ratio of I (0 0 3) / I (1 0 4) is related to the degree of cation mixing in the lattice structure. The higher I (0 0 3) / I (1 0 4) intensity ratio is, the higher degree of Li–M(Ni, Mn) order in their respective layers is [18–20] . The ratio of I (0 0 3) / I (1 0 4) in macroporous LiNi 0.5 Mn 0.5 O 2 is obviously higher than LiNi 0.5 Mn 0.5 O 2 synthesized by the solid state method which indicates that macroporous LiNi 0.5 Mn 0.5 O 2 has a higher degree of Li–M(Ni, Mn) order in their respective layers. To confirm it, Rietveld refinement and calculation of Li/Ni exchange in the lattice structure based on the XRD data was carried out. Based on its α-NaFeO 2 structure model (space group R-3m ), the 3a sites were occupied equally by Mn and Ni and the 3b sites were occupied by Li [21,22] . During the refinement process, the occupancy of the 3a sites by Mn was maintained at 0.5, and the total amount of Li and Ni within the materials was fixed, while the distribution of Li and Ni between the 3a and 3b sites was allowed to vary. The refinement converged on a model in which 7.7 mol% of Ni ions in the transition-metal sites were exchanged for Li, that is, the ion distribution is described by the formula [Li 0.923 Ni 0.077 ] 3b (Li 0.077 Ni 0.423 Mn 0.5 ) 3a O 2 . This model provides an excellent fit to the data, as can be seen in Fig. 2 , corresponding to Rwp of 4.46% and Rp of 3.82%. The refined unit cell parameters in a hexagonal setting were a = 2.8896 and c = 14.2893 Å. These values, the refined structure, and the ratio of Li/Ni exchange are in good agreement with those previously reported [23,24] . The same Rietveld refinement process was carried on LiNi 0.5 Mn 0.5 O 2 synthesized by solid state reaction method and the calculated result is 9.8 mol% of Ni ions in the transition-metal sites were exchanged by Li ion. Obviously, the ratio of Li/Ni exchange in the material synthesized by the gas-template method is smaller than that of the material synthesized by conventional solid state reaction method. The possible reason is that the solution-based method can let the reactants mix and react at the atomic level while the solid state reaction method could not blend the raw materials thoroughly and well-proportioned by using mortar and pestle. 3.2 Morphology characterization The morphology of the materials was examined by using scanning electron microscopy, which is presented in Fig. 3 . The images indicate a disorder macroporous morphology composed of individual particles of narrow size distribution, in the range of 0.2–0.5 μm, fused together to form agglomerates within which the macroporous range from 1 to 3 μm. The microparticles and multiple macroporous in this material result from the precursors and methods we used. The utilization of a solution-based method provides good mix of the constituent ions at the atomic scale. Resorcinol and formaldehyde will react and generate materials which transform to volatile products on heating and results in the formation of the observed macroporous structure. Compared to the image of LiNi 0.5 Mn 0.5 O 2 obtained by solid state reaction method, although the particle size is similar, the nanoparticle material densely piles up without any pores. Fig. 4 gives the nitrogen adsorption–desorption isotherms of LiNi 0.5 Mn 0.5 O 2 materials synthesized by different methods. The specific surface area of the macroporous LiNi 0.5 Mn 0.5 O 2 is of 8.870 m 2 g −1 which is much higher than the sample synthesized by solid state reaction method (2.929 m 2 g −1 ). The pores and tunnels in the macroporous sample account for the increasing of the specific surface area. 3.3 Electrochemical characterization Fig. 5 presents the first discharge capacity of the LiNi 0.5 Mn 0.5 O 2 samples at 0.1 C rate. Here 140 mAh g −1 is assumed to be roughly equivalent to 1 C. The first discharge capacity of the macroporous LiNi 0.5 Mn 0.5 O 2 is 174 mAh g −1 , higher than that of LiNi 0.5 Mn 0.5 O 2 prepared by solid state reaction method which is only 144 mAh g −1 . The possible reason is that all the precursors in the solution were mixed at the atomic level, resulting in a compositionally homogeneous product and macroporous structure that yields superior performance compared to the conventional solid state reaction method which the raw materials used cannot blend thoroughly by using mortar and pestle. These electrochemical results are accordance with the Rietveld refinement of XRD data, the lower ratio of Li/Ni exchange in the lattice structure, the better electrochemical performance [2,13–17] . Fig. 6 presents the rate capacity of LiNi 0.5 Mn 0.5 O 2 samples cycled between 2.5 and 4.3 V at different discharge rates. Macroporous LiNi 0.5 Mn 0.5 O 2 behaves higher discharge capacity than material synthesized by conventional solid state method at 0.1 C, 0.2 C, 0.5 C, 1 C and 2 C. At 1 C the capacity of macroporous LiNi 0.5 Mn 0.5 O 2 can reach 123 mAh g −1 , while the LiNi 0.5 Mn 0.5 O 2 synthesized by solid state methods degenerates and the capacity drops to 90 mAh g −1 . At 2 C the discharge capacity of the macroporous structure is 108 mAh g −1 , while the discharge capacity of the materials synthesized by solid state reaction method only shows 65 mAh g −1 . The results illustrate that the LiNi 0.5 Mn 0.5 O 2 with macroporous structure exhibits superior rate capability compared with the materials synthesized by solid state reaction method. Similar results have been obtained for LiCoO 2 and Li(Ni 1/3 Co 1/3 Mn 1/3 )O 2 materials with macroporous structure [10,12] . Fig. 7 presents the cycling stability at 0.1 C and Fig. 8 presents the cyclablity of LiNi 0.5 Mn 0.5 O 2 samples at 0.5 C rate. It can be clearly seen that macroporous material behaves larger discharge capacity and better capacity retention. The LiNi 0.5 Mn 0.5 O 2 synthesized by solid state reaction method drops greatly at 0.5 C rate, the first discharge capacity is of 126 mAh g −1 , after 40 cycles the discharge capacity is only 92 mAh g −1 , while the first discharge capacity of the macroporous LiNi 0.5 Mn 0.5 O 2 is 153 mAh g −1 at 0.5 C and after 40 cycles, the discharge capacity still keeps at 137 mAh g −1 . Obviously, the macroporous materials not only have a larger discharge capacity but also better capacity retention, the macroporous structure LiNi 0.5 Mn 0.5 O 2 owns a significant advantage over on the aspects of rate capability and cyclability which could be account for that the macroporous structure materials has less Li/Ni exchange ratio and can absorb more electrolyte thus shortening the diffusion distances of lithium ions. 3.4 Lithium ion diffusion coefficient calculation The intercalation and de-intercalation mechanism of LiNi 0.5 Mn 0.5 O 2 can be described as: (1) LiNi 0.5 M n 0.5 O 2 ⇄ discharge charge x L i + + x e − + L i ( 1 − x ) N i 0.5 M n 0.5 O 2 Fig. 9 shows the EIS curves of both macroporous LiNi 0.5 Mn 0.5 O 2 and the one prepared by solid state reaction method. For both of them, a semicircle in high frequency region and a line in low frequency region were observed. The lithium ion diffusion coefficient can be calculated from the formula as following: (2) D = R 2 T 2 2 A 2 n 4 F 4 C 2 σ 2 where A is the surface area of the electrode, n is the number of the electrons per molecule attending the electronic transfer reaction, F is the Faraday constant, C is the concentration of lithium ion in LiNi 0.5 Mn 0.5 O 2 electrode, R is the gas constant, T is the room temperature in our experiment, σ is the slope of the line Z ′ ∼ ω −1/2 which can be obtained from the line of Z ′ ∼ ω −1/2 (shown in Fig. 8 ), respectively. (3) C = n V = ( m / M ) V = ( ρ V / M ) V = ρ M where the constant values of F and R are 96,500 C mol −1 and 8.314 J K −1 mol −1 , respectively. A is the electrode area which is 0.785 × 10 −4 m 2 , n is 2, T is 298 K, C can be calculated from the density and the molecular weight of the materials synthesized by different methods, which are 1.2 × 10 4 mol m −3 . Deduction process is provided in Eq. (3) . The calculated lithium diffusion coefficient D (cm 2 s −1 ) of macroporous material is 3.17 × 10 −13 cm 2 s −1 , however that of the material synthesized by the conventional solid state method is only 1.41 × 10 −13 cm 2 s −1 . Obviously, the material with macroporous structure has a greater lithium ion diffusion coefficient, which may be attributed to the smaller Li/Ni exchange ratio in the lattice structure [2] . Both the larger Li ion diffusion coefficient and the shorter pathway for Li ion transfer may account for better electrochemical performance of the macroporous cathode. This result is consistent with the charge and discharge results. Macroporous material with larger lithium ion diffusion coefficient has higher capacity when charged and discharged at higher rates and possesses better rate performance. 4 Conclusions A simple approach was successfully used to synthesize pure R-3m phase and well-crystallized LiNi 0.5 Mn 0.5 O 2 with macroporous structure. One step reaction and some cheap reaction vessels can meet the synthesized requirement. This simple synthesized method has a potential industrial applicability in the future. Electrochemical test results show that LiNi 0.5 Mn 0.5 O 2 with macroporous structure displays a higher discharge capacity, better cycle stability and much better rate capability than that of LiNi 0.5 Mn 0.5 O 2 synthesized by the conventional solid state reaction method. The excellent electrochemical performance could be attributed to its lower Li/Ni exchange ratio and larger lithium ion diffusion coefficient. Meanwhile, the macroporous structure can provide more pores for increasing the electrode–electrolyte interface area which means better electrolyte penetration. Acknowledgments This work is financially supported by a Grant from the National Basic Research Program of China (“973” Program, no. 2009CB220100 ), the National High Technology Research and Development Program of China (“863” Program, no. 2009AA033701 ) and Science & Technology Commission of Shanghai Municipality ( 08DZ2270500 ), China. References [1] T. Ohzuku Y. Makimura Chem. Lett. 8 2001 744 [2] K.S. Kang Y.S. Meng J. Breger C.P. Grey G. Ceder Science 311 2006 977 [3] S.H. Kang J. Kim M.E. Stoll D. Abraham Y.K. Sun K. Amine J. Power Sources 112 2002 41 [4] A. Manthiram J. Choi W. Choi Solid State Ionics 177 2006 2629 [5] B.L. Cushing J.B. Goodenough Solid State Sci. 4 2002 1487 [6] A.M. Hashem A.E.A. Ghany K. Nikolowski H. Ehrenberg Ionics 16 2010 305 [7] X. Wang F. Zhou X.M. Zhao Z.D. Zhang M.R. Ji C.M. Tang T. Shen H.G. Zheng J. Cryst. Growth 267 2004 184 [8] Y.K. Zhou H.L. Li J. Mater. Chem. 12 2002 681 [9] N. Yabuuchi Y. Koyama N. Nakayama T. Ohzuku J. Electrochem. Soc. 152 2005 A1434 [10] N.S. Ergang J.C. Lytle H. Yan A. Stein J. Electrochem. Soc. 152 2005 A1989 [11] L. Li W.H. Meyer G. Wegner M.W. Mehrens Adv. Mater. 17 2005 984 [12] M.S. Kuthanapillil P.G. Bruce Adv. Mater. 18 2006 2330 [13] Q. Wu X.L. Li M. Yan Z.Y. Jiang Electrochem. Commun. 5 2003 878 [14] M.S. Islam R.A. Davies J.D. Gale Chem. Mater. 15 2003 4280 [15] J. Breger Y.S. Meng Y. Hinuma S. Kumar K. Kang S.H. Yang G. Ceder C.P. Grey Chem. Mater. 18 2006 4768 [16] Y.K. Sun Y.C. Bae S.T. Myung J. Appl. Electrochem. 35 2005 151 [17] M.V. Reddy G.V. Subba Rao B.V.R. Chowdari Electrochim. Acta 50 2005 3375 [18] Y. Hinuma Y.S. Meng K. Kang G. Ceder Chem. Mater. 19 2007 1790 1800 [19] M. Yoshio Y. Todorov K. Yamato H. Noguchi J. Itoh M. Okada T. Mouri J. Power Sources 74 1998 46 [20] S.H. Park Y.K. Sun Electrochim. Acta 50 2004 431 [21] B.J. Hwang T.H. Yu M.Y. Cheng R. Santhanam J. Mater. Chem. 19 2009 4536 [22] Y. Makimura T. Ohzuku J. Power Sources 119–121 2003 156 [23] J. Guo L.F. Jiao H.T. Yuan H.X. Li M. Zhang Y.M. Wang Electrochim. Acta 51 2006 3731 [24] S.B. Schougaard J. Breger M. Jiang C.P. Grey J.B. Goodenough Adv. Mater. 18 2006 905
更多查看译文
关键词
Macroporous,Rate capacity,Lithium manganese nickel oxide,Lithium ion battery,Cathode materials
AI 理解论文
溯源树
样例
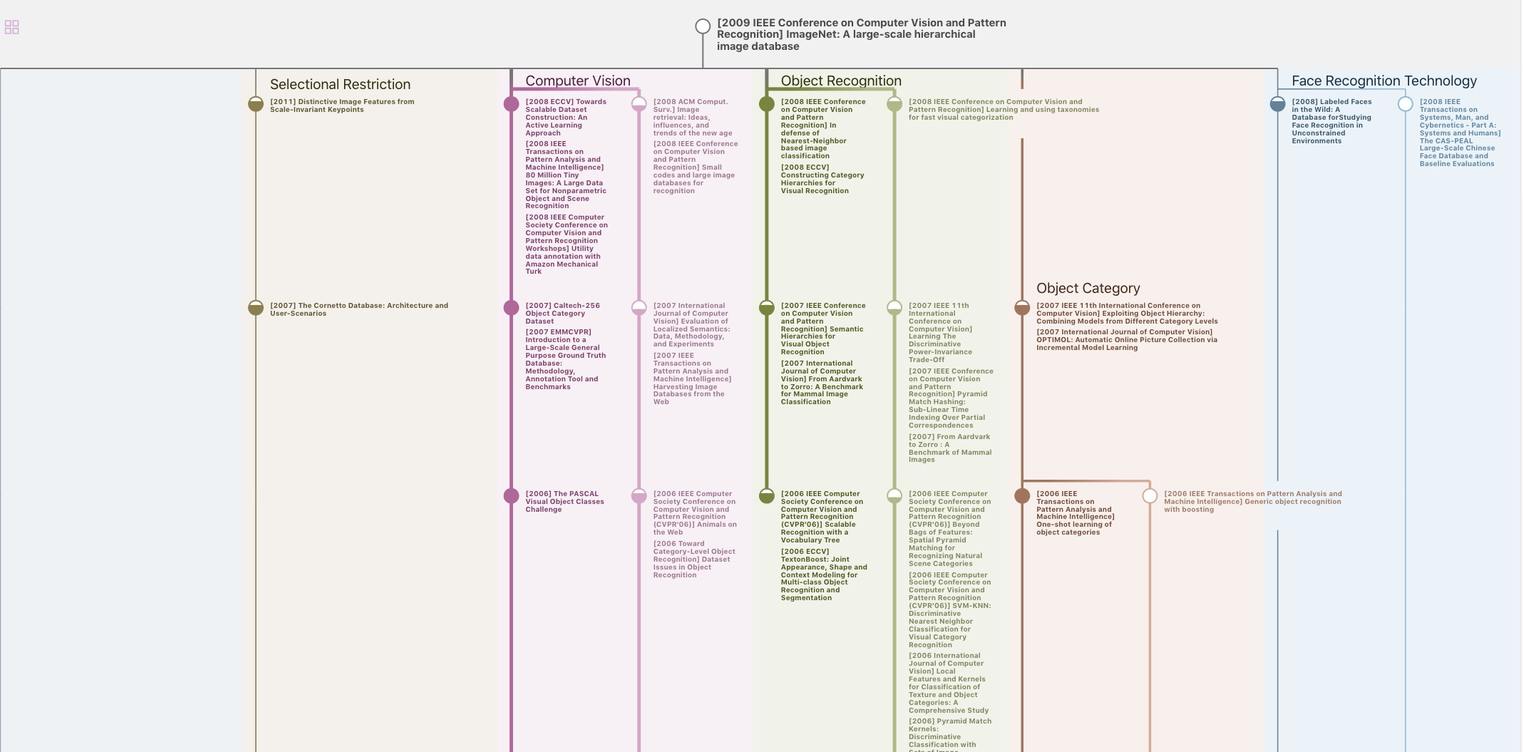
生成溯源树,研究论文发展脉络
Chat Paper
正在生成论文摘要