Effect of Si on High-Temperature Oxidation of Steel during Hot Rolling
Defect and Diffusion Forum(2008)
摘要
An oxide scale layer always forms at the strip surface during the hot rolling process. As a consequence, de-scaling and pickling operations must be performed prior or after hot rolling. Many surface defects caused by hot rolling are related to oxidation in the reheating furnace. One of these is the melting of eutectic FeO/Fe2SiO4 during reheating over 1170°C giving as a result red scale defects in Si-added steel. On the other hand, steel strip surface oxidation during hot rolling causes an industrial and environmental problem: secondary oxide is removed after roughing, but tertiary oxide scales already start to form before entering the finishing stands. Their properties affect the final steel surface quality and its response to further processing. Furthermore, the addition of alloying elements has an important impact on scale properties. In particular the alloying of silicon effects the region between scale and substrate. It causes peculiar surface properties inherited from its specific oxidation characteristics. Conventional oxidation experiments in air of silicon steels are a valuable tool to study the influence of Si on steel oxidation. After oxidation in air in the temperature range of 900-1250°C it has been observed that Si enhance markedly scale adhesion, especially above 1177°C (the eutectic temperature of FeO-Fe2SiO4 ) and also at lower temperatures. Special attention has been paid on the investigation of the effects of alloying Si on the high-temperature oxidation of steel, for a better understanding of the behaviour of modern steels during hot rolling.
更多查看译文
关键词
oxide scales,hot rolling,silicon,fayalite
AI 理解论文
溯源树
样例
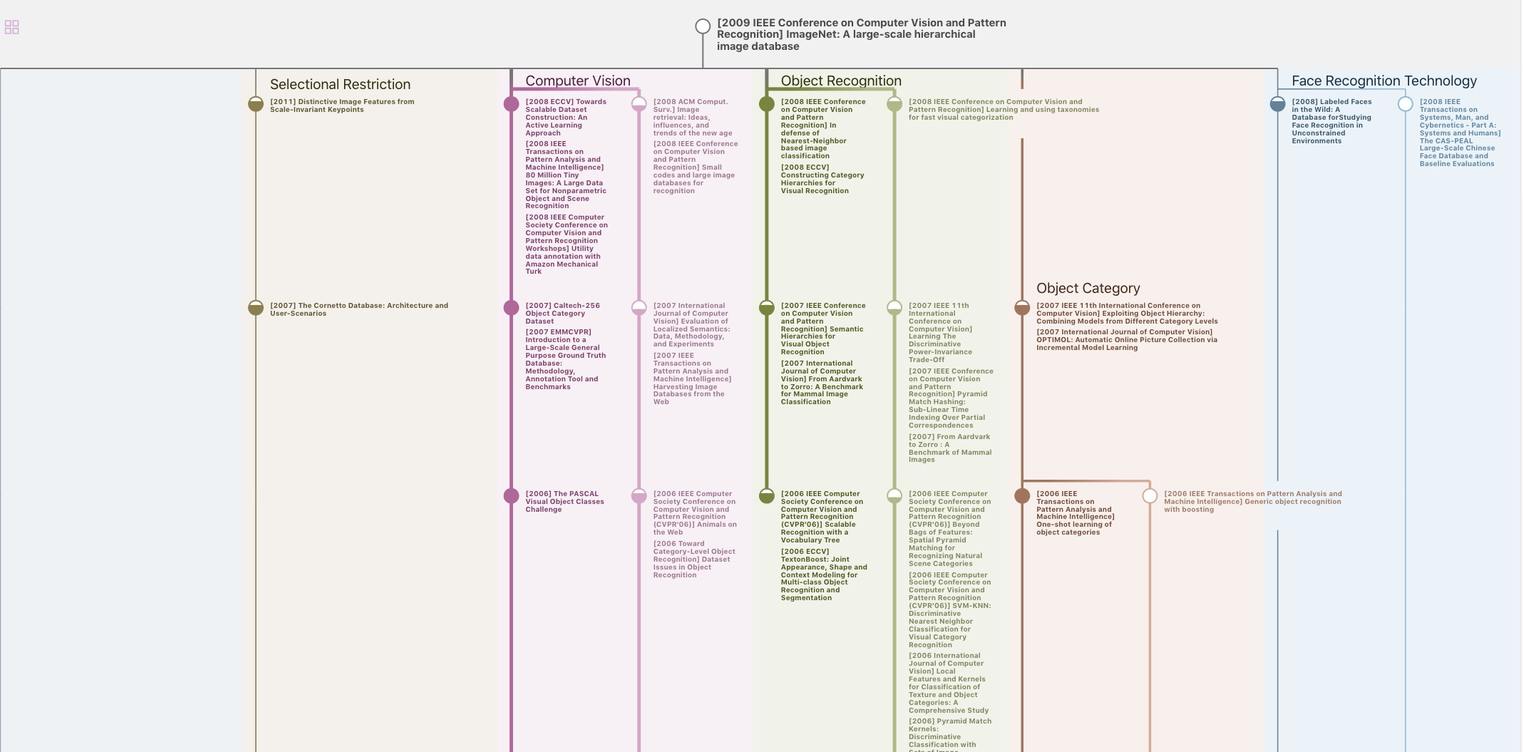
生成溯源树,研究论文发展脉络
Chat Paper
正在生成论文摘要