The room temperature mechanical properties of hot rolled 7075 aluminum alloy
Materials & Design(2012)
Abstract
Highlights ► The predominant restoration process during rolling at 250 and 350 °C is dynamic recovery. ► The recrystallized grains are evident in the microstructure of the specimens rolled at 450 °C. ► Occurrence of dynamic precipitation during rolling at 350 °C. ► A drop in strength and ductility was realized in the specimens that were rolled at 350 °C. ► The room temperature mechanical properties were improved by increasing the temperature to 450 °C. Abstract The effect of equivalent rolling strain and temperature on the microstructural evolution and mechanical properties of 7075-T7351 aluminum alloy has been studied. This has been carried out using tensile testing method. The results indicated that the predominant restoration process during rolling at 250 and 350 °C is dynamic recovery, and the driving force is not high enough to trigger the dynamic recrystallization. However, the recrystallized grains are clearly evident in the microstructure of the specimens which were rolled at 450 °C. The tensile test results showed that the room temperature strength and ductility were decreased by increasing rolling temperature in the temperature range of 250–350 °C. The room temperature mechanical properties of the alloy were started to improve by increasing the temperature up to 450 °C. The observed trends were explained through considering the microstructural evolution upon hot rolling. Keywords A. Non-ferrous metals and alloys E. Mechanical G. Scanning electron microscopy 1 Introduction The incremental rate of technological developments has dictated an unsaturated demand for new materials with desirable strength to weight ratio. Accordingly this has been the most important subject of the recent researches on development and processing of aluminum alloys. Among the various classes of aluminum alloys, the 7xxx series (Al–Zn–Mg–Cu alloy system) hold superior properties such as low density, higher specific strength and resistance to stress corrosion cracking (SCC) [1] . These outstanding properties have drawn much attention to this series of aluminum alloy. However, its low formability at room temperature is considered as an important shortcoming of this material. Thus, expanding the knowledge on the plastic deformation behavior of the 7xxx series Al alloy would be useful to improve the workability which plays an essential role in the industrialization of component fabrication. In this regard a number of previous investigations have been devoted to assess the high temperature formability of the 7075 alloy, as the most common 7xxx aluminum alloy, in predetermined deformation conditions. The majority of the involved researches have focused on investigating the deformation flow behavior of the experimental alloy during hot tension and hot compression tests [2–4] . According to their results, the Al-7075 alloy may possess a microstructure with finer grain sizes due to the occurrence of restoration processes (dynamic recrystallization and dynamic recovery) during thermo-mechanical treatments. This would enhance the mechanical properties of the material. Furthermore, a good workability was reported for the Al-7075 alloy in a broad temperature range. However, there has been a lack of organized study on the hot deformation behavior of 7075 Al alloy under the conditions encountered in the processing operation such as rolling and the influence of thermo-mechanical parameters on microstructural evolution and subsequent mechanical properties. It should be noted that the ultimate mechanical properties are directly dependent on the final microstructure which in turn is dictated by the processing history. Consequently, through a proper control of the processing conditions, it may be possible to produce excellent combinations of mechanical properties. The presence of second phase particles is also one of the most important issues on the hot deformation behavior of 7xxx series Al alloys. The 7075 aluminum alloy contains a variety of second phase particles distributing either in the grain interiors or along grain boundaries. The most commonly observed precipitate phases of 7xxx series Al alloys are the Mg(Zn 2 ,AlCu) M (or η ) hexagonal phase, the S (Al 2 CuMg) orthorhombic phase, the Al 32 (Mg,Zn) 49 T phase and Fe rich phases such as Al 7 Cu 2 Fe and Al 3 Fe [5,6] . As is well reported the existence of these particles may introduce a significant effect on the hot workability and also room temperature mechanical properties of the alloy [7,8] . Thus, it can be concluded the effective control of microstructure during thermo-mechanical processing, is also reliant on the complete understanding of the characteristics of these precipitates in the alloy system under consideration. Having all into consideration, the aim of the present work is to investigate the effect of the rolling temperature and rolling reduction on the room temperature mechanical properties of the heat treated 7075 Al alloy with emphasizing on microstructural evolution during hot rolling such as dynamic restoration processes and dynamic precipitation. 2 Experimental procedure The experimental material was 7075-T7351 aluminum alloy (Al–6.2%Zn–2.7%Mg–1.3%Cu, wt%) which was received as hot-rolled plates with different thicknesses of 20 and 50 mm. The backscattered scanning electron microscopy images of the initial microstructure in the as-received condition are shown in Fig. 1 . The results of energy dispersive spectroscopy (EDS) semi-quantitative analysis showed that the Al 7 Cu 2 Fe and S (Al 2 CuMg) phases are extensively distributed in grain interiors and along the grain boundaries. The presence of other precipitates such as η (MgZn 2 ), Al 3 Fe and FeAl 3 Si 2 were also confirmed by X-ray diffraction (XRD) patterns ( Fig. 2 ). The solute redistribution during solidification leads to micro-segregation and the formation of these coarse intermetallic particles, which may significantly influence the properties and productivity of the 7075 aluminum alloys. The as-received 7075 aluminum alloy was rolled at 250 °C, 350 °C, and 450 °C, consisting of 2 and 4 rolling passes with 25% and 20% thickness reduction per pass. The rolling was performed by a Furouzandeh®GL-200 rolling machine. This was furnished by two 10 cm-diameter rolls that rotate at 30 rpm. The rolls were neither lubricated nor heated. The room temperature tensile tests were conducted according to ASTM B557 standard [9] using plate specimens with a transverse section of 1 × 5 mm 2 and a gauge length of 25 mm. In all specimens, the deformation axis was selected to be parallel to the rolling direction. The tensile tests were performed using an Instron 4208 universal testing machine at an initial strain rate of 2 × 10 −3 s −1 . Three tensile tests were carried out on each condition and the elongation-to-failure was measured from the gauge length of the fractured specimen. Optical and scanning electron microscopy (SEM, Cam Scan, MV2300, England) were used to examine the hot-rolled microstructures. Prior to that, the specimens were prepared using standard metallographic methods. X-ray diffraction analysis was also executed on selected specimens to identify the constitutive phases in the related microstructures. For these tests, the high-resolution X-ray diffractometer (model Philips-X’pert, Netherlands) with a rotating copper anode (Cu Kα 1 ) radiation (wavelength, λ = 1.5406 Å) was employed. Scans were collected over a range of 20–120° in 2 θ with an accelerating voltage of 40 kV and a scanning speed of 2°min −1 . All XRD scans were carried out on the midthickness planes of all specimens parallel to the rolling plane. 3 Results and discussion Fig. 3 shows the typical tensile true stress–strain curves of the hot rolled specimens under different deformation conditions. As is clearly seen the room temperature mechanical properties of the alloy are influenced by the rolling temperature and total rolling reduction. For further investigation, the variations of ductility (elongation-to-fracture) and tensile strength with rolling temperature are plotted in Fig. 4 . As is observed in Fig. 4 , the elongation-to-fracture is increased with rolling temperature in the range of 250–450 °C. At 350 °C however a drop in the ductility value is realized. A similar trend is recognized for the ultimate tensile strength variation with rolling temperature. The ultimate tensile strength of the hot-rolled specimens varies between 270 and 530 MPa. Surprisingly, a significant increase is observed at 450 °C in comparison to the as received material with almost no reduction in ductility, which may be well attributed to the occurrence of dynamic recrystallization during rolling at this temperature. The observed trends would be explained through considering the microstructural evolution upon hot rolling. Fig. 5 shows the developed microstructures after applying the thermo-mechanical processing cycles. According to Fig. 5 b and e, the obtained microstructures upon hot rolling at 350 °C are consisted of the elongated grains without nucleation of new grains in the microstructure (the microstructure is pancaked). As is seen the preferred recovery at the vicinity of grain boundaries has led to the formation of serrated boundaries (indicated by arrows in Fig. 5 b and e). As is well established [10] the presence of serrated boundaries is a reliable indication of the occurrence of dynamic recovery during hot rolling. Accordingly, it can be concluded that at these conditions the predominant restoration process is dynamic recovery, and therefore the driving force is not high enough to trigger the dynamic recrystallization. The similar microstructures were also observed in the specimens rolled at 250 °C ( Fig. 5 a and d). The extent of recovery at this temperature is lower than that of 350 °C. This is rationalized considering the effect of temperature on the restoration processes. As the latter processes are thermally activated ones, those are delayed as the deformation temperature decreased. The recrystallized grains are clearly evident in the microstructure of the specimens which were rolled at 450 °C. As is indicated by arrows in Fig. 5 c and f, the most of the recrystallized grains were nucleated through grain boundaries bulging mechanism which is a characteristic feature of discontinuous dynamic recrystallization (DDRX). This is an interesting observation since it has been well established that the presence of high densities of several types of fine precipitates in aluminum alloys (such as the present experimental alloy) may act as effective obstacles to the dislocation movement and hence preventing the occurrence of DDRX. In the present work however the occurrence of DDRX is rationalized as is follows. Considering the solutionizing temperature range of the experimental alloy which starts from 480 °C, the precipitates are soft and easy to be cut through by dislocations during the deformation at 450 °C. The dislocations are then released and added to the dislocation pile-ups at the grain boundaries. Therefore, due to the remarkable dislocation density variation across a grain boundary, the grain boundary may start to bulge into the grain with the higher dislocation density. It is worth to note that these results are in a good agreement with a number of previous investigations on Al–Zn–Mg–Cu alloys which have reported the occurrence of dynamic recovery and dynamic recrystallization during hot compression tests under similar thermo-mechanical conditions [11–14] . The SEM micrographs of the specimens rolled at different temperatures of 250, 350 and 450 °C with rolling reduction of 50% are depicted in Fig. 6 . As is seen in Fig. 6 a, there are some gray colored second phases with elliptical morphology in the microstructure. The Cu-rich nature of these precipitates was verified through the SEM/EDS analysis. Increasing the rolling temperature to 350 °C results in the formation of white precipitates in the microstructure ( Fig. 6 b). These white second phases with irregular jagged shape and serrated boundaries are Fe-rich precipitates, mostly with the nominal composition of Al 7 Cu 2 Fe [7] . It is anticipated that these Fe-rich phases were dynamically precipitated during hot rolling at this temperature. As is also observed in Fig. 5 b and e, the amount of precipitates in the microstructure is increased by increasing the rolling temperature up to 350 °C. For further investigation the XRD patterns of the rolled specimens at 250, 350 and 450 °C (with rolling reduction of 80%) are illustrated in Fig. 7 . The XRD peaks could be identified due to α (Al) solid solution (labeled Al), MgZn 2 (labeled η ), Al 2 CuMg (labeled S), Al 7 Cu 2 Fe, Al 3 Fe and FeAl 3 Si 2 . As is seen the rolled microstructure at 250 °C is mostly consisted of MgZn 2 , Al 7 Cu 2 Fe, Al 3 Fe and Al 2 CuMg precipitates ( Fig. 7 a). Finely dispersed Al 2 CuMg and MgZn 2 precipitates may hinder the easy movement of the grain boundaries and stabilize the subgrain structure formed during rolling thereby decreasing the rate of recrystallization [15] . The previous works have shown that deliberately forming fine precipitates prior to hot deformation may lead to almost complete suppression of recrystallization in 7xxx alloys, even after high levels of deformation [15] . Fig. 7 b shows that by increasing the temperature to 350 °C, an appreciable volume fraction of Fe rich phases such as Al 7 Cu 2 Fe and FeAl 3 Si 2 were precipitated in the microstructure. Moreover, the presence of some Fe rich phases such as FeAl 3 Si 2 was detected only at 350 and 450 °C. As was expected the XRD results confirm the precipitation of Fe-rich phases during hot rolling at 350 °C. It is worth to note that the high recovery rates operative during hot rolling of the alloy at 350 °C may introduce a significant effect on dynamic precipitation of Fe-rich phases. The previous reported results indicated that during climbing, the dislocations drag solute atoms from solid solution, which by rapid diffusion along the core nucleate precipitates on the dislocations [16,17] . At 450 °C, the majority of precipitates in the microstructure were MgZn 2 , Al 2 CuMg, Al 7 Cu 2 Fe, FeAl 3 and FeAl 3 Si 2 . The more amounts of MgZn 2 precipitates were also monitored at this temperature ( Fig. 7 c). The observed precipitates in the microstructure of 7075 Al alloy at different conditions (as-received and rolled at various temperatures) are listed in Table 1 . Considering above discussion, the variation of room temperature mechanical properties in the specimens which were rolled at different temperatures may be rationalized considering the occurrence of dynamic precipitation and dynamic restoration processes during hot rolling. As was observed in Fig. 4 , the room temperature strength of the experimental alloy was decreased with increasing the rolling temperature up to 350 °C. The latter may be attributed to the higher extent of recovery at 350 °C than that of 250 °C. The dislocation density of the alloy which was rolled at 250 °C is much higher and distributes less uniformly, compared to the alloy processed at 350 °C. Consequently, the dislocations interacting with each other and forming tangles during subsequent tensile test at room temperature are much more severe for the alloy made by the rolling at 250 °C than those of the alloy made by the rolling at 350 °C. Accordingly, decreasing of ultimate tensile strength with increasing rolling temperature (up to 350 °C) seems to be reasonable through considering the effect of dislocation structures as barriers to the dislocation movement. On the other hand, the observed ductility drop in the specimens which were rolled at 350 °C may be well attributed to the dynamic precipitation of Fe-rich secondary phases during hot rolling. As was noted above, these phases are mostly consisted of Al 7 Cu 2 Fe, FeAl 3 and FeAl 3 Si 2 precipitates. In accordance with the present results, a number of previous researchers have also reported that the presence of Fe-rich precipitates in the microstructure of 7075 Al alloy may have a detrimental effect on the room temperature mechanical properties of the alloy [8,18] . This may be justified as follows. The Fe-rich phases are favorite sites for the nucleation and growth of micro cavities. In fact, the lower levels of ductility at these brittle sites may result in the nucleation and formation of cavities around the precipitates thereby increasing the length of the micro-cracks [19] . This in turn decreases the elongation-to-fracture which can be tolerated by the specimen. As was shown in Figs. 3 and 4 , the mechanical properties of the experimental alloy were improved upon rolling at 450 °C. This is related to the occurrence of dynamic recrystallization and its resulting grain refinement. The increased density of high angle grain boundaries (as obstacles to the dislocation movements) due to the grain refinement was considered as the major reason of the improved ultimate tensile strength. In addition, as was observed in XRD pattern the more amounts of M-phase (MgZn 2 ) precipitates were monitored at this temperature. This is in accord with previous results which believed that during heat up and the pre-heat to 450 °C prior to rolling, copious precipitation of Mg(Zn 2 ,AlCu) occurred within the grains [20] . Thus the observed increase in ultimate tensile strength may also be attributed to the lattice strain interactions between these needle shaped precipitates and dislocations during tensile test at room temperature. On the other hand, at essentially constant volume fraction of the second phase, the higher the density of high angle grain boundaries the lesser the amount of precipitates along them. Consequently the strain concentration at the grain boundaries is reduced and thus the formation of grain boundary voids is prolonged [21] . Therefore, the rather significant increase in the strength and ductility of the specimens rolled at 450 °C in contrast to that of 250 and 350 °C appears to be logical. 4 Conclusion In the present study, the microstructural evolution and the room temperature mechanical properties of the 7075 Al alloy was investigated upon rolling at different conditions. The results indicated that the room temperature mechanical properties of the alloy are significantly influenced by the rolling temperature in the temperature range of 250–450 °C. A drop in strength and ductility was realized in the specimens that were rolled at 350 °C. This was attributed to the occurrence of dynamic recovery and dynamic precipitation of Fe-rich phases during hot rolling. The room temperature ductility and strength were started to improve again by increasing the temperature up to 450 °C. The latter was related to the occurrence of dynamic recrystallization and precipitation of fine M-phase during rolling at 450 °C. References [1] J.P. Immarigeon R.T. Holt A.K. Koul L. Zhao W. Wallace J.C. Beddoes Lightweight materials for aircraft applications Mater Charact 35 1995 41 67 [2] M. Rajamuthamilselvan S. Ramanathan Hot deformation behaviour of 7075 alloy J Alloy Compd 509 2011 948 952 [3] Q. Guo-zheng L. Ke-wei Z. Jie C. Bin Dynamic softening behaviors of 7075 aluminum alloy Trans Nonferrous Metal Soc China 19 2009 537 541 [4] M.R. Rokni A. Zarei-Hanzaki A.A. Roostaei H.R. Abedi An investigation into the hot deformation characteristics of 7075 aluminum alloy Mater Des 32 2011 2339 2344 [5] M. Conserva P. Fiorini Interpretation of quench-sensitivity in Al–Zn–Mg–Cu alloys Metall Trans 4 1973 857 [6] D. Godard P. Archambault E. Aeby-Gautier G. Lapasset Precipitation sequences during quenching of the AA 7010 alloy Acta Mater 50 2002 2319 [7] F. Xi-gang J. Da-ming M. Qing-chang Z. Bao-you W. Tao Evolution of eutectic structures in Al–Zn–Mg–Cu alloys during heat treatment Trans Nonferrous Metal Soc China 16 2006 577 581 [8] M. Kamiya T. Yakou Role of second-phase particles in chip breakability in aluminum alloys Int J Mach Tool Manuf 48 2008 688 697 [9] ASTM B557-02. Standard test methods of tension testing wrought and cast aluminum- and magnesium-alloy products. ASTM. 2002; 2(Pt 2):4. [10] F.J. Humphreys M. Hatherly Recrystallization and related annealing phenomena 1996 Pergamon Oxford, UK p. 54–9 [11] J. Adrien E. Maire R. Estevez J.C. Ehrstrom T. Warner Influence of the thermomechanical treatment on the microplastic behaviour of a wrought Al–Zn–Mg–Cu alloy Acta Mater 52 2004 1653 1661 [12] G. Lin X. Zheng W. Yang D. Feng P. Dashu Study on the hot deformation behavior of Al–Zn–Mg–Cu–Cr aluminum alloy during multi-stage hot compression Acta Metall Sin 22 2009 110 116 [13] G.Y. Lin Z.F. Zhang H. Zhang D.S. Peng J. Zhou Study on the hot deformation behaviors of Al–Zn–Mg–Cu–Cr aluminum alloy Acta Metall Sin 21 2008 109 115 [14] Z.M. EI-Baradie M. EI-Sayed Effect of double thermo-mechanical treatments on the properties of 7075 A1 alloy J Mater Process Technol 62 1996 76 80 [15] Denzer DK, Liu J. Method of producing un-recrystallized aluminum products by heat treating and further working. United States patent US 5061387; October 1991. [16] M. Song Y. He D. Xiao B. Huang Effect of thermomechanical treatment on the mechanical properties of an Al–Cu–Mg alloy J Mater Des 30 2009 857 861 [17] U. Dahmen K.H. Westmacott The mechanism of φ ′ precipitation on climbing dislocations in Al–Cu Scripta Metall 17 1983 1241 1246 [18] I. Kirman The Relation between microstructure and toughness in 7075 aluminum alloys Mater Trans 1471 2 1970 1761 [19] R. Hertzberg Deformation and fracture mechanics of engineering material 2nd ed. 1983 John Wiley p. 37–49 [20] J.D. Robson Microstructural evolution in aluminium alloy 7050 during processing Mater Sci Eng A 382 2004 112 121 [21] B. Mintz S. Yue J.J. Jonas Hot ductility of steels and its relationship to the problem of transverse cracking during continuous casting Int Mater Rev 36 1991 187 217
MoreTranslated text
Key words
A. Non-ferrous metals and alloys,E. Mechanical,G. Scanning electron microscopy
AI Read Science
Must-Reading Tree
Example
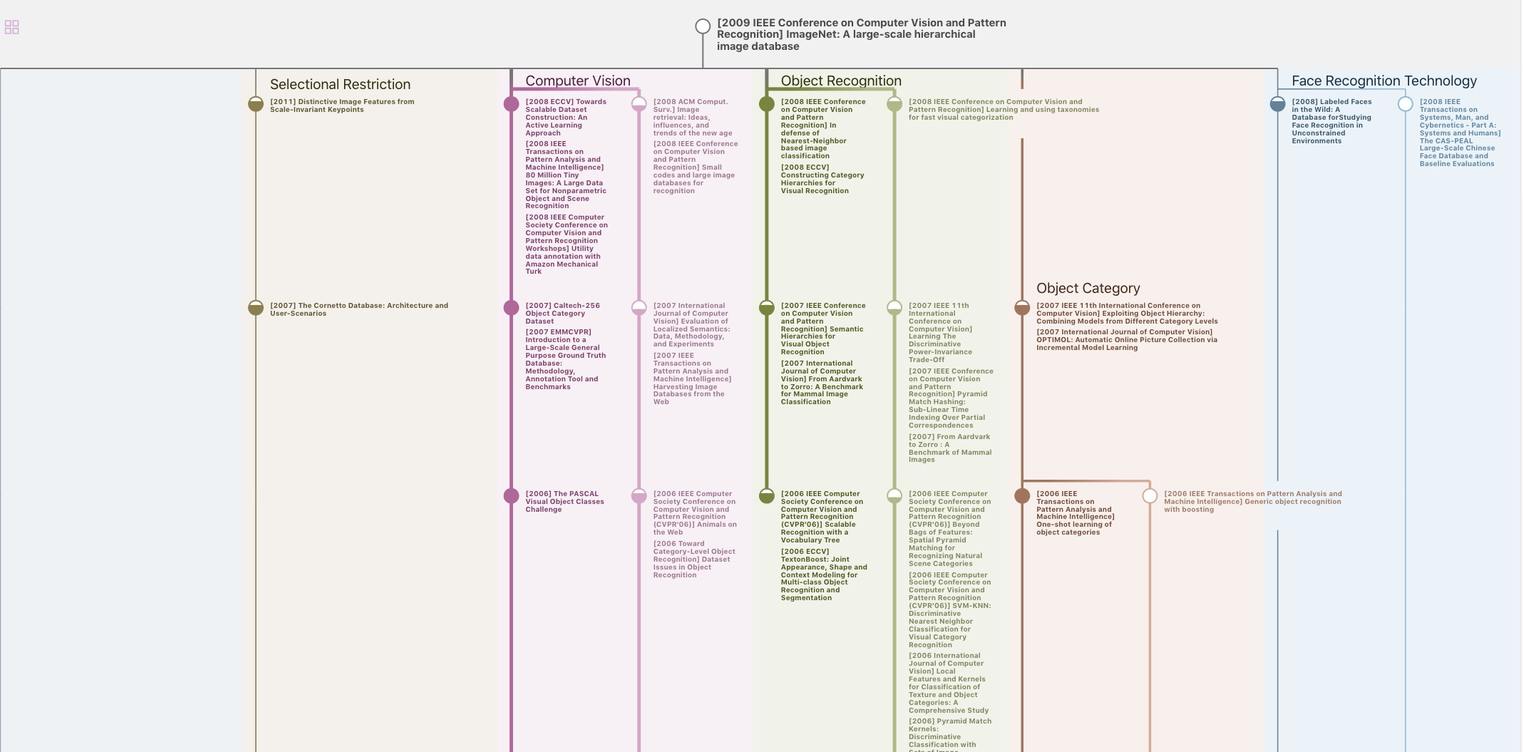
Generate MRT to find the research sequence of this paper
Chat Paper
Summary is being generated by the instructions you defined