High heat flux facility GLADIS:
Journal of Nuclear Materials(2007)
摘要
The new ion beam facility GLADIS started the operation at IPP Garching. The facility is equipped with two individual 1.1 MW power ion sources for testing actively cooled plasma facing components under high heat fluxes. Each ion source generates heat loads between 3 and 55 MW/m 2 with a beam diameter of 70 mm at the target position. These parameters allow effective testing from probes to large components up to 2 m length. The high heat flux allows the target to be installed inclined to the beam and thus increases the heated surface length up to 200 mm for a heat flux of 15 MW/m 2 in the standard operating regime. Thus the facility has the potential capability for testing of full scale ITER divertor targets. Heat load tests on the WENDELSTEIN 7-X pre-series divertor targets have been successfully started. These tests will validate the design and manufacturing for the production of 950 elements. 1 Introduction The operation of long pulse fusion experiments requires plasma facing components (PFCs) capable of steady-state operation with high thermal loads of up to 10–20 MW/m 2 and long mean time between necessary replacement. In order to investigate the thermo-mechanical behaviour of such PFCs, extensive tests with heat loads similar to the operational conditions are mandatory. High heat flux (HHF) tests are essential to assess the performance and to define the acceptance criteria for the quality control of industrially manufactured divertor components for fusion experiments such as W7-X and ITER. As an addition to the existing test facilities, which mostly use electron beam heating [1–5] , the IPP Garching has commissioned the HHF test facility GLADIS (Garching Large Divertor Sample Test Facility) of the ion beam type shown in Figs. 1 and 2 . The water-cooled vacuum test chamber (1.5 m diameter, 3.2 m length) is equipped with two H + ion sources. Both ion sources are inclined at 8° to the horizontal axis of the facility. The preferred position of the target is 3 m in the z -direction from the ion sources at the intersection of the beams. So far, only one of the two RF ion sources has been used for heat loading tests with an operating regime of 3–55 MW/m 2 at the target position. A detailed technical description of the design of the main components, the diagnostics, and the control and data acquisition systems can be found in another publication [6] . Ion beams generate homogeneous heating due to the complete absorption of the beam power on the surface of the tested material. They are especially suited for loading of metallic surfaces, e.g. tungsten. In electron beam facilities, reflection and formation of secondary electrons reduces the deposited beam power by up to ∼50% for these materials [7] . A mixed beam of ions and neutrals is used in GLADIS in contrast to other ion beam facilities [8,9] . Since a complex magnetic ion removal system with deflection magnets, ion dumps and cryopumps is unnecessary, the cost of the facility was significantly reduced. However, the operation of the ion source causes an increase of the hydrogen pressure in the main vacuum chamber to 1 × 10 −3 mbar during the pulse. This increase does not affect source performance. The beam dump, integrated in the movable end-door, is able to absorb the full beam power for continuous operation. GLADIS allows effective testing of large components up to 2 m length and can provide up to 8.5 l/s of cooling water. The high perpendicular heat flux allows targets to be installed inclined to the beam and thus lengthening the heated surface up to 200 mm for a heat flux of 15 MW/m 2 in the standard operating regime. Therefore the facility has the potential for the testing of full scale ITER divertor targets [10] . 2 Operating results 2.1 Ion sources The GLADIS facility uses the two sources previously used to provide radial heating on the W7-AS Stellarator. The current is extracted from a water-cooled 3-grid system originally developed for long pulse heating on the ASDEX tokamak [11] . Two modifications to the sources have been made. The first is the utilization of a cooled Faraday screen in the plasma chamber to allow the pulse length to be extended to CW operation. The second is a re-cabling of the transformer used to isolate the RF generator from the source high voltage that has resulted in a lower temperature rise in the ferrites. These changes allow operations for increased pulse duration (30 s) and higher duty cycle (33%). The primary concern about these modifications is thermal loading of other source components. Pulses of 15 s at full power have been run during X-ray safety tests and 60 s RF only pulses have been made successfully. Currently, for GLADIS operation the source parameters are: H 2 gas flow ⩽ 6 mbar l s −1 , RF power 15–35 kW, high voltage 20–53 kV. The current extracted from the source varies between 5 and 22 A depending on both the RF power and high voltage settings. No ion neutralizer is used in GLADIS giving a beam divergence of 1.5°, slightly higher than previously reported for the originally W7-AS sources [12] . 2.2 Beam profiles 2.2.1 Measurement of beam profiles The power density distribution of the beam was measured at the target plane with an inertially cooled copper calorimeter (see Fig. 1 , marked with (1)). The cross shaped calorimeter has 34 thermally insulated Cu plugs (∅ 10 mm) separated by 15–30 mm. The local power density is calculated from the temperature rise of these individual plugs which are measured by thermocouples in the thermal equilibrium after the pulse. A 2D Gaussian fit to these data provides the beam profiles. Fig. 3 shows the beam profile obtained from a 876 kW pulse. When extrapolated to the maximum achieved beam power (1.15 MW), a central power density of 55 MW/m 2 could be achieved in the target plane. Selected profiles are shown in Fig. 4 to demonstrate the wide operational regime of GLADIS. Greater than 87% to the beam power expected, based on these calculations, has been calorimetrically measured on the water-cooled W7-X targets during long pulses. To increase the maximal power density up to ∼80 MW/m 2 , the target position could be reduced to 1.7 m distance to the ion source (marked in Fig. 3 with (2)). A movable calorimeter is installed to measure and to monitor the beam profiles during test campaigns. A Cu bar, equipped with 17 calorimeter plugs can be vertically moved into the beam close to the installed target. The calorimeter returns to a position outside the vessel after the measurement. 2.3 Future improvements A system to routinely measure of beam composition via Doppler shift spectroscopy will be installed. A single line of sight will provide light to a calibrated spectrometer via fibre optic cable. A vacuum lock for target elements up to a length of 800 mm will be installed. This allows the movement and changing of targets without breaking the vacuum of the main chamber. It is planned to increase the beam pulse rate to achieve 60–100 pulses/h. The final rate achieved will depend strongly on the RF power, extraction voltage and duration of the pulse. Beam pulse shape modulation will be explored. Currently it is possible to pulse the beam with a minimum pulse length and interval of 10 μs. In the future, a second RF generator and a new HV power supply will allow for simultaneous independent operation of the two ion sources to increase the loaded target area and power available by superposition of both ion beams. 3 First results of W7-X pre-series target tests The envisaged steady-state operation of W7-X requires the installation of a divertor target (area 19 m 2 ) assembled from 14 different types of actively cooled elements (total 890) [13] . A target element consists of flat tiles made of CFC (Carbon Fibre reinforced Composite) NB31 as plasma facing material bonded onto water-cooled heat sinks made of CuCrZr copper alloy. It is designed to withstand a steady-state heat flux of 10 MW/m 2 and a power load up to 100 kW. Depending on the length of the elements (250–600 mm), 10–24 individual CFC tiles with an active metal casting (AMC ® ) interlayer are bonded to the heat sink. Two different bonding techniques between CFC tiles and heat sink are being evaluated, electron beam welding (EB) and hot isostatic pressing (HIP). Before PLANSEE (Austria) starts the production of the 950 elements (including 60 spare elements), 31 pre-series target elements have to be qualified in GLADIS. They will be tested with at least 100 thermal cycles at 10 MW/m 2 for 10 s to evaluate the low cycle fatigue behaviour of the bonding between CFC and cooling structure. This first HHF test campaign for W7-X focused on the evaluation of the design of the L-shaped CFC tiles front and the selection of the CFC tile bonding technique ( Fig. 5 ). GLADIS is also an essential tool for the qualification of the non-destructive examinations methods and for the definition of the acceptance criteria of the manufactured divertor elements. In the front tiles, the C-fibre planes are oriented 45° to the bonding surface. Heat load tests are mandatory to validate the design of the front tile for the expected maximum heat flux of 3 MW/m 2 in W7-X. Target elements with a length of 700 mm (including water pipes) were inclined 45° to the ion beam axis in GLADIS. The heat load tests with a central power density of 6.5 MW/m 2 in the beam resulted in a heat flux distribution between 5.5 and 2.2 MW/m 2 on the front tile (see Fig. 6 ). Elements manufactured either by EB or HIP have been successfully tested without any delaminations and thus the proposed design has been qualified. The 42 tiles of the first three elements were tested with 100 cycles of 10.5 MW/m 2 , 10 s pulse length and water velocity 8–10 m/s. Initial results show: no tile detachment occurred, but growing hot spots at the edges of several tiles indicate local bonding problems which developed during heat loading. These locations are clearly visible in the infrared (IR) thermography after 20–40 thermo-mechanical cycles of the element. This observation proves that 100 thermal cycles are sufficient to judge the quality of the CFC tiles and of the bonding to the component. In principle, both bonding techniques are suitable for manufacturing. However, elements manufactured by HIP show a more homogeneous surface temperature distribution and less bonding defects during heat loading. The IR measured surface temperature of the loaded CFC tiles increased on average by 50–150 °C during the cycling for tiles without visible defects or hot spots. The average surface temperature of 860 °C of the HIP elements increased to 1000 °C after cycling and from 1020 to 1100 °C for the EB element, respectively. 4 Conclusions The high heat flux test facility GLADIS routinely operates providing a beam power between 150 kW and 1.1 MW from one ion source. The beam pulses are highly reproducible and so far over six months of operation have been achieved with no interruption due to the sources themselves. Presently, one ion source allows high power operation with pulse lengths up to 15 s. The measured beam profiles are in good agreement with the theoretical calculations. First tests demonstrated that GLADIS is an useful tool for the qualification of industrial manufactured divertor targets with heat loads similar to the operating conditions. No tile detachment occurred, but hot spots at the edges were observed for several tiles. So far, only a few of the W7-X pre-series elements have been tested completely, thus any definitive conclusion is premature. The observation of beginning and growing of hot spots on the surface after a few cycles proves that 100 thermal cycles provide valuable information to judge the quality of the most critical parts of the elements, the CFC tiles and the bonding to the CuCrZr cooling structure. References [1] R. Duwe, W. Kühnlein, H. Münstermann, in: Proceedings of the 18th Symposium on Fusion Technology, Karlsruhe, 22–26 August 1994, p. 355. [2] M. Diotalevi, M. Febvre, Ph. Chappuis, in: Proceedings of the 19th Symposium on Fusion Technology, Lisbon, 16–20 September 1996, p. 491. [3] D. Youchison et al., in: R.D. Boyd, A.J. Ghajar (Eds.), Heat Transfer in High Heat Flux Systems, ASME Book No. G00956, New York, 1994. [4] M. Akiba Plasma Dev. Oper. 1991 202 [5] V.K. Gagen-Torn, I.R. Kirillow, V.L. Komarov, et al., in: Proceedings of the 18th Symposium on Fusion Technology, Karlsruhe, Germany, 22–26 August 1994, p. 363. [6] H. Greuner Fusion Eng. Des. 75–79 2005 345 [7] M. Roedig Fusion Eng. Des. 61&62 2002 135 [8] M. Lochter R. Uhlemann J. Linke Fusion Technol. 19 4 1991 2101 [9] H.D. Falter et al., in: Proceedings of the 13th Symposium on Fusion Technology, Varese, Italy 1984, p. 571. [10] S. Fouquet J. Schlosser M. Merola A. Durocher F. Escourbiac A. Grosman M. Missirlian C. Portafaix Fusion Eng. Des. 81 2006 265 [11] J.-H. Feist et al., in: 10th Symposium on Fusion Engineering Proceedings, Philadelphia, 1983, p. 1494. [12] N. Rust et al., in: 29th EPS Conference on Plasma Physics and Controlled Fusion, ECA, vol. 26B, Montreux, 17–21 June 2002, p. 4045. [13] J. Boscary Nucl. Fusion 43 2003 831
更多查看译文
AI 理解论文
溯源树
样例
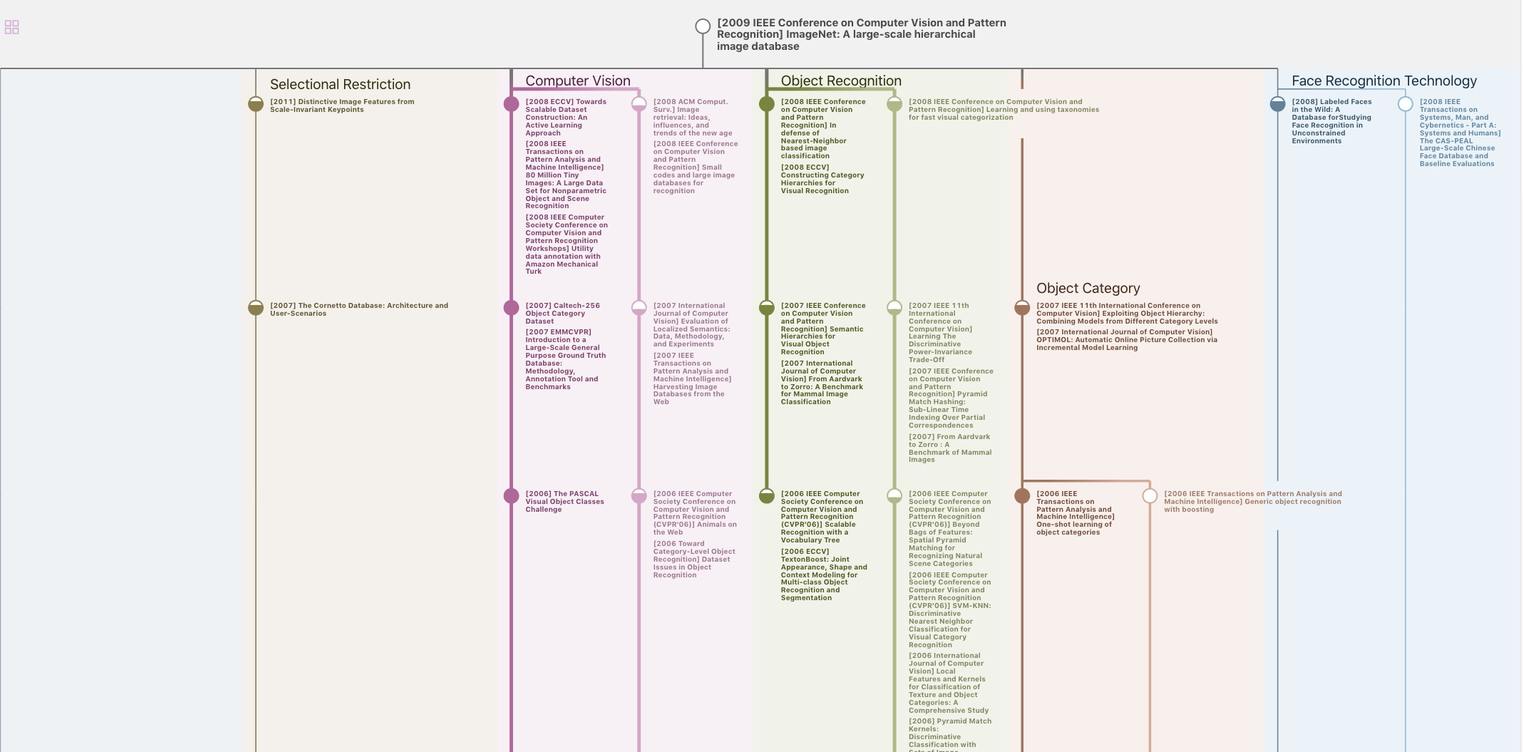
生成溯源树,研究论文发展脉络
Chat Paper
正在生成论文摘要