Influence Of Wafer Thinning Process On Backside Damage In 3d Integration
2013 IEEE INTERNATIONAL 3D SYSTEMS INTEGRATION CONFERENCE (3DIC)(2013)
摘要
Ultra-thinning less than 10 microns of Si wafer is expected to realize small TSV feature which provides low aspect ratio and coupling capacitance. However, a detail of residual surface damage during thinning is unrevealed. In this paper, subsurface damage following wafer thinning from the back of 300 mm wafers using three different types of thinning process was investigated by means of Raman spectroscopy, XTEM, and Positron annihilation analysis, respectively. A coarse grinding generates significant rough subsurface ranged several micron and damage layer including amorphous and plastic-deformed Si along grinding topography. Fine grinding, second step of thinning, reduced those surface roughness and almost removed after thinning at least removal of 50 microns. However, plastic-deformed subsurface layer with a thickness of 100 to 200 nm are still remained which leaves an inside elastic stress layer ranging up to about 10 microns in depth. Chemical-Mechanical Polishing (CMP) process as a final step of thinning enables to remove residual damages such as structural defects and lattice strains after 1-5 microns thick polishing while vacancy-type defects only remain.
更多查看译文
关键词
3D integration,wafer thinning,back grinding,subsurface damage,Raman spectroscopy,TEM
AI 理解论文
溯源树
样例
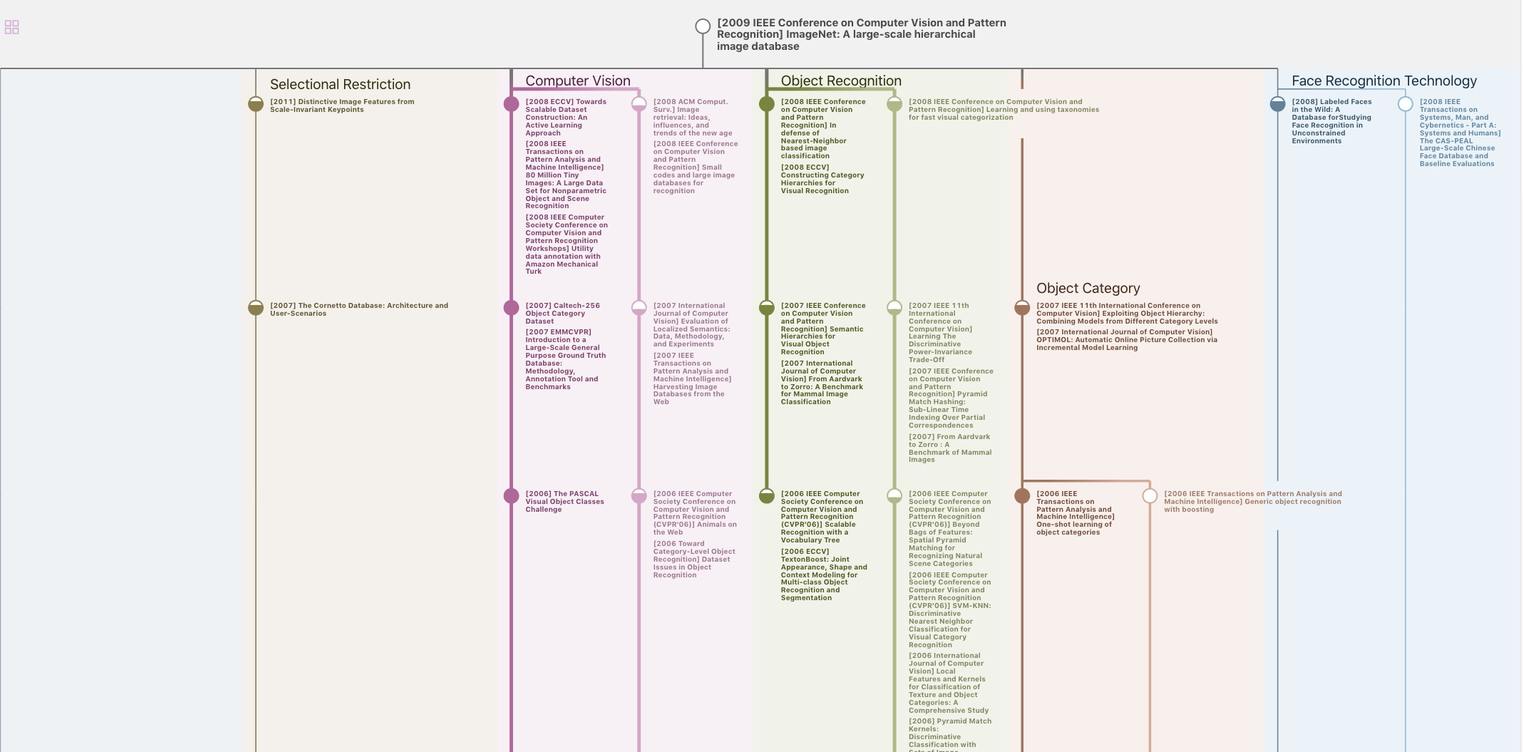
生成溯源树,研究论文发展脉络
Chat Paper
正在生成论文摘要