Thermal and mechanical properties of a nanocomposite of a photocurable epoxy-acrylate resin and multiwalled carbon nanotubes
Materials Science and Engineering: A(2011)
摘要
In this work, thermal and mechanical behaviors of nanocomposites of a photocurable epoxyacrylate resin and multiwalled carbon nanotubes (MWCNT) were investigated. A combination of sonication, and mechanical and magnetic stirring was used to disperse 0.25 wt% and 0.75 wt% of MWCNTs into the resin. Two photocuring cycles using 12 and 24 h UV-A radiation were studied. Nanoindentation was the chosen technique for characterizing the modulus of elasticity and hardness of samples. The curing degree and glass transition temperature of the epoxyacrylate matrix and the nanocomposites were determined by Differential Scanning Calorimetry (DSC). In addition, the Vickers microhardness and nanocomposite morphology were also investigated by Scanning Electronic Microscopy (SEM) and Transmission Electronic Microscopy (TEM). The results indicate an increase in the stiffness and hardness of the material, and a shift in the glass transition temperature. The increase in the elastic modulus is in concordance with the predictions made by two simple models: rule of mixture and Halpin–Tsai equation. A fair agreement between nanoindentation and microhardness measurements is also found. Finally, the importance of curing degree in some of the properties investigated in this study is also discussed. Keywords Carbon nanotubes Nanoindentation Polymers Hardness measurement 1 Introduction Since the discovery of carbon nanotubes (CNT) at the beginning of the last decade, much effort has been made in most areas of science and engineering to use these nanofillers in a variety of applications, especially due to their extraordinary and unprecedented mechanical and transport properties. Reinforcement in polymeric materials is one of the most frequently found applications in the literature [1–6] . In general, reinforcement has been successfully applied in some thermoplastics, especially in high crystalline polymers. In thermosets, epoxy resins have been very often studied as a potential matrix for nanocomposites with CNT. Small quantities of CNT, generally between 0.1 and 5.0% (w/w), are added to the polymeric matrix aiming to improve mechanical and thermal properties [1–6] . Reinforcement and toughness is difficult to obtain at the same time in amorphous polymers. Although the use of low content of MWCNTS covalently combined with polycaprolactone showed improvements for polyvinyl chloride, for instance [7] . Photocurable resins are a very important class of thermosets, especially because of the presence of acrilate, metacrylate or epoxy groups. One of the main advantages of this resin is the rapid cure by means of radiation. In addition, photocurable resins have chemical and corrosion resistance, high modulus, and thermal and dimensional stability [8–11] . Hence, the application of this class of polymer is often found in Aeronautical, Biomedical and Microelectronics industries, especially in those that employ stereolitography [12,13] . Sangermano et al. [14] have obtained high reinforcement by adding single-walled carbon nanotubes (SWCNT) to an epoxy photocurable resin. By varying the composition from 0.025 to 0.1% (w/w), an increase from 197 to 210 °C in T g was achieved. The modulus of elasticity improved from 5.38 GPa to 8.99 GPa by adding 0.025% (w/w) to the resin. As regards hardness, the authors found an increase from 0.32 to 0.54 GPa. It should be pointed out that the time for loading/unloading appeared to be too short. This has probably induced undesirable conditions for nanoindentation. Zhu et al. [15] have studied a photocurable resin reinforced with 0.5 wt% of MWCNT, reporting an increase of 35% in the modulus of elasticity. Besides sonication and functionalization for improving dispersion of carbon nanotubes the use of block copolymers has been showing interesting results for preparing epoxy nanocomposites [16] . To carry out this work, nanocomposites of a photocurable epoxy-acrylate resin with 0.25% and 0.75% (w/w) MWCNTs were used. Mechanical characterization by nanoindentation was performed to obtain the elastic modulus and hardness. Thermal characterization by DSC was conducted to determine the glass transition temperature and curing degree of the samples. Microhardness, SEM and TEM were also used to study the nanocomposites. Finally, two simple mathematical models were employed to predict Young's modulus of the nanocomposites, and comparisons were made with the experimental results. 2 Experimental Nanocomposites of an epoxy/acrylate photocurable resin, SOMOS 10220 (multiacrylate monomers 45–50%, epoxies 15–25%, polyols 20–35%, and photoinitiators 0.2–5.0%) with 0.25 and 0.75 wt% of MWCNT (Bayer – Baytubes – C150P) were prepared [17] . Dispersion of MWCNTs was carried out using a combination of sonication (model Sonics Vibra Cell, 750 W), and mechanical and magnetic stirring. Samples with 0.5 ± 0.1 mm of thickness were cured for 12 and 24 hrs with UV-A (355 nm) lamps of 800 W/m 2 intensity. Somos ® 10220 photopolymer resins were formulated to stereolitography platforms utilizing solid-state laser systems. This resin type for UV curing was comprised of acrylate monomers, which polymerizes by a free-radical mechanism; and an epoxy system, including reactive liquid monomers, cationic photoinitiators (onium salts) and photosensitizers [18] . Photosensitizers are capable of initiating polymerization in near UV or visible light as a result of a direct interaction between an excited state of the photosensitizer and the initiator starting cationic polymerization of the epoxide [19] . Kinetic studies of the cure reaction of similar resins indicate the radicalar acrylate polymerization is three to four times faster than the cationic epoxy polymerization [20,21] . In order to determine the modulus of elasticity and hardness, a Nanoindenter XP was used with a pyramidal Berkovich indenter. All measurements were an average over six penetrations containing ten cycles of loading/unloading with hold times of 30 s at maximum load. Loading and unloading times were 5 s and the following loads were applied: 0.1, 0.2, 0.4, 0.8, 1.6, 3.2, 6.5, 13.0, 26.0 and 50.0 mN. The heating rate used in DSC and TGA was 10 °C/min. Samples were heated up to 600 °C in a NETZSCH STA 449C. SEM was performed in a Zeiss DSM 940A, and TEM was performed in a JEOL – JEM ExII (120 kV). Microhardness measurements were performed using an HMV-2T Shimadzu. Loads of 245 mN were employed, and all measurements were an average over five indentations in each sample. 3 Results and discussion 3.1 Nanoindentation Fig. 1 a shows the variation of the modulus of elasticity with penetration for nanocomposites cured for 12 h. At the higher penetration depths, a modulus of elasticity of 1.81 ± 0.03 GPa was obtained for the neat resin, while for a nanocomposite with 0.25% (w/w), 2.20 ± 0.04 GPa was reached, and with 0.75% of MWCNT, 2.60 ± 0.09 GPa. The latter represents an increase of 42% compared to the neat resin. Fig. 1 b shows that the neat resin presented a modulus of elasticity of 2.20 ± 0.09 GPa, the nanocomposite with 0.25% (w/w) MWCNT has 2.50 ± 0.02 GPa, and 2.05 ± 0.04 GPa for the nanocomposite with 0.75% (w/w) MWCNT. It is worth noting that in both figures the values of elastic modulus are higher near the surface, showing an asymptotic behavior. In addition, similar behavior for hardness was found in both materials. It has been shown in the literature that the effects of reinforcement are smaller in stiffer epoxy matrices. Consequently, results obtained for the nanocomposite cured for 24 h with 0.75% (w/w) MWCNT could be explained [6] . Fig. 1 a and b also shows that near the surface there is a great variation of the properties presenting an asymptotic behavior. A similar behavior was found for hardness measurements. 3.2 Modeling and simulation Regarding hardness (presented in Fig. 2 a and b ) for samples cured for 12 h (0.075 ± 0.001 GPa), an increase of 30% and 77% was found for a nanocomposite with 0.25% (w/w) (0.098 ± 0.002 GPa) and 0.75% (0.133 ± 0.007 GPa) (w/w) of MWCNT, respectively. For samples cured for 24 h (0.114 ± 0.009 GPa), an increase of 20% and a decrease of 9% were found for a nanocomposite with 0.25% (w/w) (0.137 ± 0.002 GPa) and 0.75% (0.094 ± 0.005 GPa) (w/w) of MWCNT, respectively. Two simple models are employed to estimate the Young's modulus of the nanocomposites ( Y c ). The rule of mixtures (Eq. (1) ) and the Halpin–Tsai equation (Eq. (3) ) are applied to the case where carbon nanotubes are randomly oriented in nanocomposites. The required data for such simulations are: the Young's modulus of the nanotubes (considered to vary within 500–750 GPa [22] ), the Young's modulus of the polymeric matrix [set to 1.8 GPa for 12 h and 2.2 GPa for 24 h (experimental data)], the aspect ratio of the CNTs supplied by Bayer [ L / D : length/diameter are respectively L = 10 μm and D = 14.5 nm (Baytubes Datasheet)] and the CNTs volumetric fraction. More details about these equations can be found in Coleman et al. [1] . (1) Y ′ c = ( η 0 ⋅ η 1 ⋅ Y f − Y m ) V f + Y m The parameter η 0 is 0.2 for random fibers in 3D, and η 1 is an efficiency factor given by: (2) η 1 = 1 − tanh ( a ( L / D ) ) a ( L / D ) and a = − 3 E m 2 E m ln V f ⥄ (3) Y ″ c Y m = 3 8 1 + ζ ⋅ η L ⋅ V f 1 − η L ⋅ V f + 5 8 1 + 2 ⋅ η T ⋅ V f 1 − η T ⋅ V f (4) η L = ( Y f / Y m ) − 1 ( Y f / Y m ) + ζ (5) η T = ( Y f / Y m ) − 1 ( Y f / Y m ) + 2 where Y ′ c is the composite modulus by rule of mixture, η 0 is the orientation efficiency factor, η 1 is the length efficiency factor, Y f is the fibre modulus, Y m is the matrix modulus, V f is the fiber volume fraction, Y m is the composite modulus by rule of Halpin–Tsai, and ζ is twice the aspect ratio. In Table 1 , all results for simulations performed in this work are presented. Analyzing Table 1 , it is worth noticing that the simulated values are in fair agreement with the experimental results obtained in this work. Considering Young's modulus of carbon nanotubes is equal to 500 or 750 GPa and a volumetric fraction of 0.25%, agreement is fair for nanocomposites cured for 12 and 24 h with rule of mixture and Halpin–Tsai equation being 2.20 and 2.50 GPa, respectively, as the experimental values. Considering the simulated values with Young's modulus of carbon nanotubes equal 1000 GPa and the content of nanofillers for 0.75%, it can be seen that the Halpin–Tsai equation started to overestimate values. The results obtained from these two simple models are very similar to those obtained using more sophisticated models applied to similar systems [23,24] . Emphasis should be placed on the two hypotheses considered in these models: the homogeneous nanofiller dispersion and its strong adhesion to the matrix. 3.3 Microhardness Table 2 presents the results for microhardness from all samples studied in this work. No significant variations in this property are observed for all the samples studied. The values determined here are in the same order of hardness measured by nanoindentation. 3.4 Differential Scanning Calorimetry (DSC) The DSC technique was used in this work to monitor the curing degree of the nanocomposites and the neat resin. It can be seen observing Figs. 3 and 4 that the curing peaks present in the liquid neat resin have decreased with the increase of the curing time by means of UV-A. The measured curing enthalpy of the liquid neat resin determined experimentally in this work was 147.3 J/g. For the 12 h-UV cured neat resin, the measured enthalpy was 7.4 J/g, while the enthalpy for the sample cured for 24 h was 7.0 J/g. It can be inferred that in both cases the curing degree is quite similar for neat resin. It is also observed that the curing enthalpy increases by increasing the content of MWCNT in the nanocomposites, as also found in the literature [25] . The curing degree was defined in this work according to Eq. (6) : (6) CURE DEGREE ( % ) = E N T H A L P Y R E S I N − E N T H A L P Y S A M P L E E N T H A L P Y R E S I N Only small variations of the cure degree with the UV curing time were observed ( Table 3 ) for all nanocomposites, except for the sample with 0.75 wt% of MWCNT. In this case, the more significant increase in curing degree with longer times is very probably related to the high content of MWCNT that absorbs a significant part of UV-A radiation. This is not observed for samples with lesser amounts (0.25% (w/w)) of MWCNT. There is considerable work in the literature that shows UV shielding effects after the addition of small contents of carbon nanotubes in polymeric matrices [14,26,27] . In our experiments, resin films cured for longer periods had a higher curing degree as you would expect with a higher cross-linking density, and this is indirectly showed by our DSC measurements. According to Putz et al. [28] , a nanocomposite (epoxy/MWCNT) with a smaller curing degree has a higher T g and samples with a higher curing degree presented a decrease in T g . These alterations in T g according to the authors, are explained by cooperative rearranging regions (CCRs). According to Putz et al. a strong polymer–nanofiller interaction will affect the dynamics of the nearest layer of polymer segments, and the change in dynamics can be propagated up to several hundred nanometers into a film. They also argued that in nanocomposites with a lower curing degree, there is a lack of topological constraints; and increasing connectivity (higher curing degree) constraints impose higher activation energy. Therefore, localized motions are impeded, decreasing the CCR size with an increase in cross-link density. Due to this, there are reasons to believe that our data corroborates the explanations given by Putz et al. [28] . Carbon nanotubes can act as electromagnetic shielding, therefore increasing their fraction, and resulting in a lower expected curing degree [14,26,27] . According to the results obtained in this work, samples cured for 12 h were more affected by UV shielding. In samples cured for 24 h, it is highly probable that this electromagnetic protection was reduced because a similar curing degree was obtained in all samples. Even increasing the amount of MWCNT, the same curing degree is obtained. In the case of samples cured for 24 h, an increase in T g is related to a higher fraction of MWCNT as all three samples had a very similar curing degree. In addition, it should be pointed out that in the work of Loos et al. [6] , similar findings were found, although no theory was used to explain the experimental data. 3.5 Scanning Electronic Microscopy (SEM) and Transmission Electronic Microscopy (TEM) Micrographs of fractured surfaces of nanocomposites are shown in Figs. 5 and 6 . All specimens exhibited a relatively smooth surface indicating a typical, brittle fracture behavior, and no significant changes were observed in the nanocomposites with the addition of MWCNTs. The nanomechanical properties indicated higher values of Young's modulus near the surface in agreement with these micrographs. Observing Figs. 7 and 8 , it is possible to see that a nanocomposite was developed owing to the fact that nanofillers containing at least one dimension smaller than 100 nm (diameter) were present in the matrice. 3.5.1 Nanohardness/Microhardness In reference to the results of nanohardness and microhardness, the difference in the hardness values may be explained by the fact that the nanoindenter measures the hardness at a nanoscale, where the depth of penetration is in the order of nm, while microhardness tests are calculated in the order of μm. Microhardness affects a much wider volume whereas nanohardness is very localized. It should be stressed that the values of both measured hardnesses are in the same order of magnitude. 3.5.2 Nanohardness/Microhardness/DSC A small curing degree effect (decrease) was noted in the measured microhardness, especially in the sample cured for 24 h with 0.75 wt% of MWCNTs. In the nanohardness measurement, the following trends were observed: (a) A lower curing degree in samples cured for 12 h caused an increase of 30% and 77% in 0.25 wt% and 0.75 wt% MWCNTs, respectively. It is possible to see there are effects from the variation of curing degree in nanohardness. (b) A small rise in curing degree was observed in the nanocomposite samples cured for 24 h with 0.25 wt% of MWCNTs, and a decrease of 9% in samples with 0.75 wt% MWCNTs. It should be noted that a lower curing degree with 0.75 wt% MWCNTs produces a sample with equal hardness to a higher curing degree with the same content of carbon nanotubes. These findings are in agreement with Putz et al. [28] . 3.5.3 Nanohardness/Microhardness/Young's modulus/DSC Trends observed in Young's modulus are very similar to trends observed in nanohardness. Once again a higher curing degree caused smaller increases in this property compared to the neat resin. It is possible to notice that higher T g s do not guarantee stiffer materials. The two highest Young's moduli were observed in samples with the two lowest T g s. 4 Conclusions In this work, nanocomposites prepared with MWCNT showed a significant improvement in their nanomechanical properties. Two different contents of MWCNT were employed, and in both cases, nanocomposites with superior nanomechanical properties were produced, except for the nanocomposite with 0.75% (w/w) of MWCNTs cured for 24 h. The highest ratio of reinforcement was observed in a nanocomposite with 0.75% (w/w) of MWCNT cured for 12 h. Predictions made with two simple models presented fair agreement with experimental results obtained in this work in most cases. DSC indicated that a high curing degree was obtained in all samples. An increase in T g 's up to 10 °C were detected when MWCNTs were added to the epoxy-acrylate matrix. SEM micrographs of fractured surfaces indicated a fragile behavior. TEM micrographs showed that nanocomposites were developed. Results of Vickers hardness are in the same order of those obtained by nanoindentation. Finally, it was possible to see that curing degree is a very important variable to be considered in the reinforcement in nanocomposites. Acknowledgments The authors would like to thank the Brazilian Space Agency (AEB Uniespaço) and CNPq for financial support; CAPES-DS for the scholarship to Marcos Nunes dos Santos; ROBTEC for providing the resin; Bayer for providing MWCNTs and for Prof. S.C. Amico for T.E.M. images. References [1] J.N. Coleman U. Khan W.J. Blau Y.K. Gun’ko Carbon 44 2006 1624 1652 [2] M. Micusiki M. Omstova I. Krupa J. Prokes P. Pissis E. Logakis C. Pandis P. Potschke J. Pionteecks J. Appl. Polym. Sci. 113 2009 2536 2551 [3] H. Liu C. Brinson Compos. Sci. Technol. 68 2008 1502 1512 [4] T.W. Chou. L. Gao E.T. Thostenson Z. Zhang J.H. Byun Compos. Sci. Technol. 70 2010 1 19 [5] E.T. Thostenson T.W. Chou Carbon 44 2006 3022 3029 [6] M.R. Loos S.H. Pezzin S.C. Amico C.P. Bergmann L.A.F. Coelho J. Mater. Sci. 43 2008 6064 6069 [7] W. Guojian W. Lijuan Z. Mei C. Zhengmian Compos.: Part A 40 2009 1476 1481 [8] F Boey S.K. Rath A.K. Ng M.J.M. Abadie J. Appl. Polym. Sci. 86 2002 518 525 [9] D.K. Chattopadhyay S.S. Panda K.V.S.N. Raju Prog. Org. Coat. 54 2005 10 19 [10] I.C. Riegel, L.L. Freitas, D. Samios, Polímeros: Ciência e Tecnologia v. jul/set (1999) 58–64. [11] E. Andrzejewska M. Andrzejewska J. Polym. Sci. Part A: Polym. Chem. 36 1998 665 673 [12] P. Klauss, Master Dissertation, Federal Univeristy of Santa Catarina, 2006. [13] J. Stampfl A. Wöss S. Seidler H. Fouad A. Pisaipan F. Schwager R. Liska Macromol. Symp. 217 2004 99 107 [14] M. Sangermano E. Borella A. Priola M. Messori R. Taurino P. Pötschke Macromol. Mater. Eng. 293 2008 708 7134 [15] Y.F. Zhu C. Ma W. Zhang R.P. Zhang N. Koratkar J. Liang J. Appl. Phys. 105 2009 054319 [16] J. Cho I.M. Daniel D.A. Dikin Compos.: Part A 39 2008 1844 1850 [17] Z. Gao E. Grulke A. Ray Colloid Polym. Sci. 285 2007 847 854 [18] C.E. Corcione A. Greco A. Maffezzoli J. Therm. Anal. Calorim. 72 2003 687 693 [19] R. Serra R. Nomen J. Sempere J. Therm. Anal. Calorim. 52 1998 933 943 [20] C. Decker Nucl. Instrum. Methods Phys. Res. Sect. B 151 1999 22 28 [21] G.V. Salmoria P. Klauss A.T.N. Pires J. Roeder V. Soldi Polym. Test. 27 2008 698 704 [22] X.L. Xie Y.W. Mai X.P. Zhou Mater. Sci. Eng. R 49 2005 89 112 [23] A. Muc M. Jamróz Mech. Comp. Mater. 40 2004 101 106 [24] A. Selmi C. Friebel I. Doghri H. Hassis Compos. Sci. Technol. 67 2004 2071 2084 [25] K. Yang M. Gu Y. Jin G. Mu X. Pan Compos.: Part A 39 2008 1670 1678 [26] M. Sangermano S. Pegel P. Pötschke B. Voit Macromol. Rapid Commun. 29 2008 396 400 [27] S. Li H. Chen D. Cui J. Li Z. Zhang Y. Wang T. Tang Polym. Compos. 31 2010 507 515 [28] K.W. Putz M.J. Palmeri R.B. Cohn R. Andrews L.C. Brinson Macromolecules 41 2008 6752 6756
更多查看译文
关键词
Carbon nanotubes,Nanoindentation,Polymers,Hardness measurement
AI 理解论文
溯源树
样例
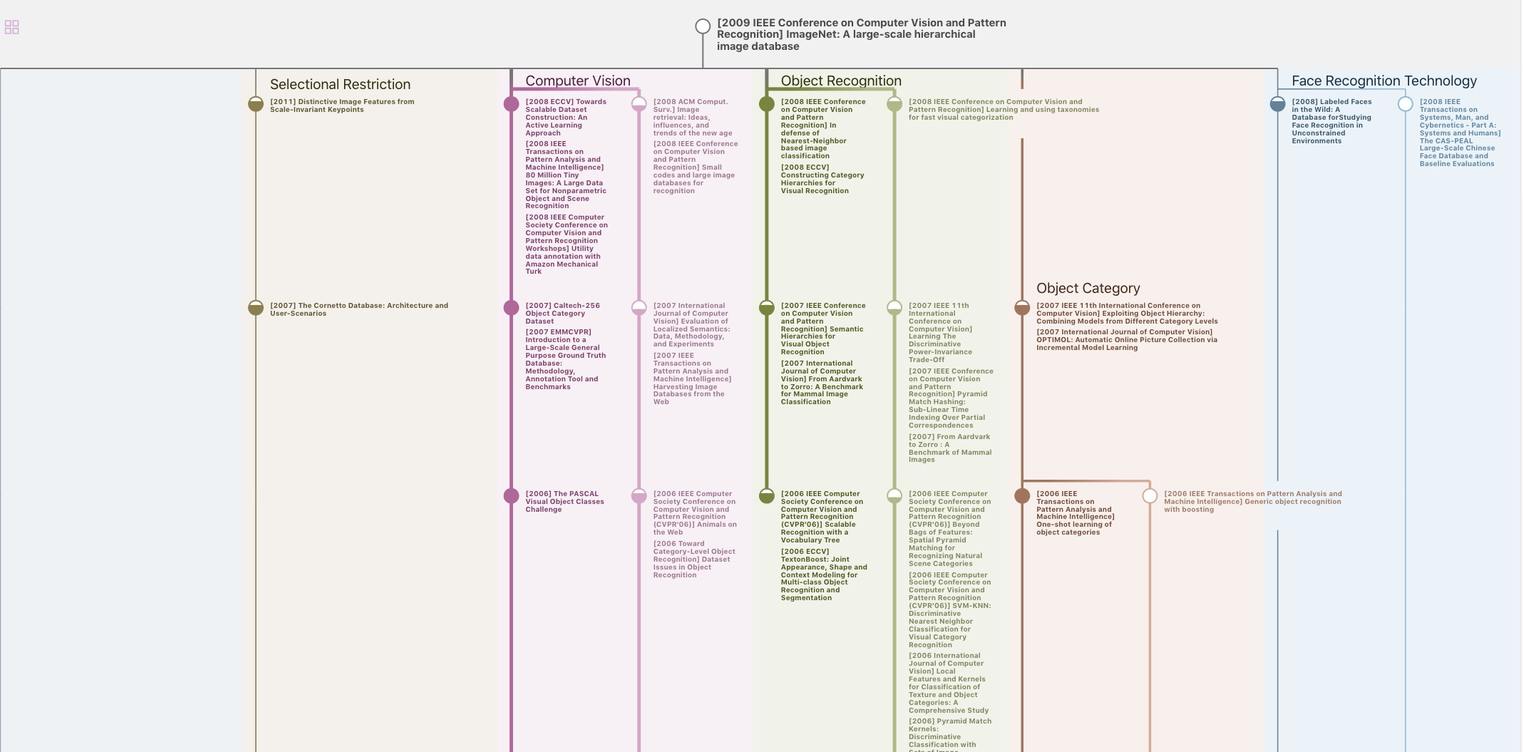
生成溯源树,研究论文发展脉络
Chat Paper
正在生成论文摘要