Remote robotic underwater grinding system and modeling for rectification of hydroelectric structures
Robotics and Computer-Integrated Manufacturing(2013)
摘要
A submersible grinding robot has been designed to automate the dam gate metallic structure repair process. In order to measure and control the amount of material removed during the process, an empirical approach for modeling the material removal rate (MRR) of the underwater grinding application is proposed and presented in this paper. The objective is to determine the MRR in terms of the process parameters such as cutting speed and grinding power over a range of variable wheel diameters. Experiments show that water causes drag and a significant loss of power occurs during grinding. An air injector encasing the grinding wheel has been prototyped, and it is shown that power loss can be reduced by up to 80%. A model, based on motor characterization and empirical relations among system and process parameters, is developed for predicting MRR which will be used for the robotic grinding control system. A validation is carried out through experiments, and confirms the good accuracy of the model for predicting the depth of cut for underwater grinding. A comparative study for dry and underwater grinding is also conducted through experiments and shows that the MRR is higher for underwater grinding than in dry conditions at low cutting speeds.
更多查看译文
关键词
empirical approach,hydroelectric structure,empirical relation,power loss,control system,low cutting speed,process parameter,dry condition,repair process,significant loss,material removal rate
AI 理解论文
溯源树
样例
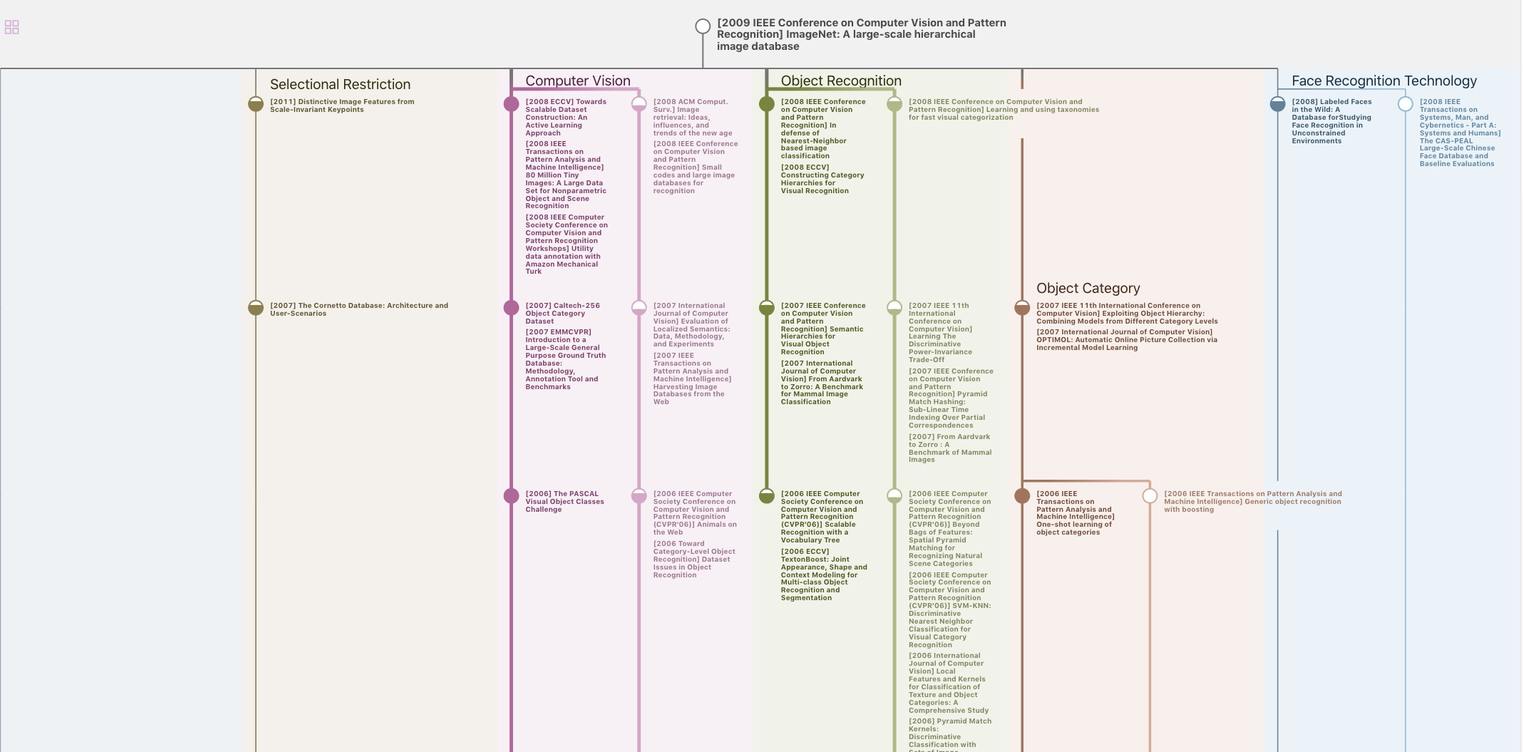
生成溯源树,研究论文发展脉络
Chat Paper
正在生成论文摘要